# Unlocking the Hidden Power: Exploring Versatile Applications of Hole Magnets
**Summary:** Hole magnets, seemingly simple devices, possess a remarkable range of applications across diverse industries and everyday life. This article delves into the hidden power of these magnetic components, uncovering their unique advantages, exploring their various uses from manufacturing and healthcare to crafting and home improvement, and providing insights into selecting the right hole magnet for your specific needs. Discover how these often-overlooked tools can revolutionize your projects and solve complex problems with their robust holding power and convenient mounting options.
## The Underestimated Strength and Adaptability of Hole Magnets
Hole magnets, also known as countersunk magnets or recessed magnets, are permanent magnets designed with a pre-drilled hole, typically accommodating screws, bolts, or rivets. This seemingly simple feature unlocks a world of versatility compared to their counterparts. The presence of the hole allows for secure mechanical fastening in addition to magnetic attraction, creating exceptionally strong and reliable bonds, especially in situations where adhesives might fail or be impractical. This combined approach offers a superior solution for applications requiring both strong holding force and permanent or semi-permanent mounting.
Their adaptability shines in their ability to be seamlessly integrated into various assemblies. They can be easily attached to non-magnetic materials, such as wood, plastic, or aluminum, providing a magnetic surface where none existed before. This characteristic makes them invaluable in creating custom fixtures, jigs, and holding systems for a wide variety of industries and hobbies. The range of available sizes, materials (such as neodymium, ferrite, and alnico), and coatings ensures that there’s a hole magnet to suit nearly any application.
## Revolutionizing Manufacturing and Assembly Processes
In manufacturing, hole magnets are instrumental in streamlining production processes. They are commonly used in holding workpieces during machining, welding, and assembly, significantly improving accuracy and efficiency. For instance, in automotive manufacturing, these magnets are employed in holding body panels in place during welding, ensuring precise alignment and reducing the need for complex clamping systems. This contributes to faster cycle times and reduces the risk of manufacturing errors.
Furthermore, hole magnets are used in creating magnetic fixtures that hold components securely while automated machinery performs tasks. This reduces the need for manual intervention, increasing productivity and minimizing the risk of worker injury. Their consistent holding force allows for repeatable results, ensuring high-quality output and minimizing waste. The ability to quickly attach and detach components using these magnetic fixtures also contributes to greater flexibility in production lines, allowing for rapid changes in manufacturing processes as needed.
## Hole Magnets in Innovative Healthcare Applications
The use of hole magnets extends into the healthcare industry, primarily in applications requiring secure attachment of medical devices and instruments. They can be found in prosthetic limbs, providing a safe and reliable connection between the prosthetic and the patient’s body. The ease of use and secure attachment are crucial for patients’ comfort and independence. Magnets are less bulky and more easily manipulated than traditional locking mechanisms.
Beyond prosthetics, hole magnets play a crucial role in creating specialized equipment for assisting patients with limited mobility. For example, they’re used to secure adjustable supports and customized medical devices to wheelchairs or hospital beds allowing patients to safely reach objects. In medical imaging, they contribute to the precise positioning of patients and devices during procedures such as MRI and X-rays. The non-invasive nature of magnetic attachment minimizes patient discomfort and enhances the accuracy of diagnostic procedures. As medical technology continuously advances, the application of hole magnets will continue to grow accordingly.
## Elevating Crafting and DIY Projects with Magnetic Solutions
For hobbyists and DIY enthusiasts, hole magnets offer a wealth of creative possibilities. They are commonly used in crafting, making it easier to attach embellishments to clothing, create magnetic closures for boxes and bags, and build interactive displays. The ability to effortlessly attach and detach components simplifies the crafting process and allows for greater experimentation and creativity. Magnetic closures can replace fiddly buttons or zippers, allowing for easier opening and closing and providing a cleaner, more modern style.
In DIY projects, hole magnets come in handy for creating custom organizers, tool holders, and temporary mounting solutions. For instance, they can be used to create a magnetic tool rack in a garage or workshop, allowing tools to be easily accessed and stored. They can also be used to temporarily attach decorations or signage, providing a flexible and damage-free alternative to nails or screws. The ease of use and versatility of hole magnets make them an essential part of any maker’s toolkit.
## Transforming Home Improvement with Reliable Magnetic Fasteners
Home improvement projects often require secure and reliable fastening solutions, and hole magnets can provide just that. They are used to install cabinet hardware, hang pictures, create magnetic door closures, and secure temporary fixtures. The ease of installation and removal makes them an ideal choice for projects where flexibility and convenience are essential. When adding hooks or other decorative elements to furniture or walls, magnets can prevent holes where they are not needed long term.
Furthermore, hole magnets can be used to address common household problems. They can be used to create a magnetic knife rack in the kitchen, keeping knives safely and conveniently within reach. They can also be used to secure shower curtains, preventing water from splashing onto the floor. Their ability to combine strong holding force with easy installation makes them a valuable asset in any home improvement project.
## Selecting the Right Hole Magnet: Material, Size, and Coating
Choosing the right hole magnet involves careful consideration of the application’s specific requirements. Important factors include the required holding force, the operating temperature, the type of material to which the magnet will be attached, and the environmental conditions it will be exposed to. The most common magnet materials are neodymium, ferrite, alnico, and samarium cobalt, each offering different strengths and properties.
Neodymium magnets offer the highest holding force for their size, making them ideal for applications where space is limited but great strength is required. Ferrite magnets are more cost-effective and resistant to corrosion, making them a suitable choice for outdoor or humid environments. Alnico magnets offer excellent temperature stability, making them ideal for applications where high temperatures are a concern. Additionally, coatings such as nickel, epoxy, and zinc can enhance the magnet’s resistance to corrosion and wear. The size of the hole and the overall dimensions of the magnet must also be carefully considered to ensure compatibility with screws/bolts and integration within the assembly.
## Understanding Magnetic Strength and Pull Force Ratings
The pull force of a hole magnet is an essential specification determining its ability to hold objects securely. This rating, typically measured in pounds or kilograms, refers to the maximum force required to pull the magnet directly away from a flat steel surface. However, several factors can influence the actual holding force achieved in a real-world application. Surface finish, air gaps, and the angle of applied force all play a role.
A rough or uneven surface will reduce the holding force due to reduced contact area. Any air gap between the magnet and the steel surface will also significantly decrease the holding force, as magnetic force decreases exponentially with distance. The angle at which the force is applied also matters; a shear force (sideways force) will typically result in a much lower holding capability compared to a direct pull-off force. Therefore, when selecting a hole magnet, it is important to consider these factors and choose a magnet with a pull force rating that is significantly higher than the expected load to ensure a secure and reliable hold.
## Exploring Different Types of Hole Magnets: Countersunk, Threaded, and More
Beyond the basic design, hole magnets are available in various configurations to suit different mounting and attachment needs. Countersunk hole magnets feature a tapered hole that allows screws to sit flush with the magnet’s surface, providing a clean and professional appearance. Threaded hole magnets have a threaded hole that allows them to be securely attached to bolts or threaded rods, creating a more robust and adjustable connection.
Additionally, specialized hole magnets such as pot magnets with countersunk holes and rubber-coated magnets with holes are available for specific applications. Rubber-coated magnets offer increased friction and protection against scratches, making them suitable for use on delicate surfaces. Selection of proper magnet size and coating is extremely important to maximize the usefulness of the magnet. Choosing the correct type of hole magnet is crucial for ensuring optimal performance and ease of integration in any project
## Maximizing the Lifespan and Performance of Hole Magnets
Proper care and maintenance are essential for maximizing the lifespan and performance of hole magnets. Avoid exposing them to extreme temperatures, which can weaken their magnetic properties. Store them in a clean and dry environment to prevent corrosion, especially for magnets lacking protective coatings. Be mindful of impact forces, as repeated impacts can cause demagnetization or physical damage.
Also, keep magnets away from sensitive electronic devices, such as pacemakers, credit cards, and computer hard drives, as the magnetic field can interfere with their operation. When handling strong magnets, exercise caution to avoid pinching fingers or damaging the magnets themselves. Taking these precautions will help ensure that your hole magnets provide reliable and consistent performance for many years to come.
## Conclusion
Hole magnets, with their inherent versatility, are transformative components that provide a wide range of applications in industries like manufacturing, health care, crafting, DIY, and even home improvement. This article highlights unique characteristics of hole magnets, describing their strength and how they can adapt to varied solutions. It also details how the lifespan and performance of the magnets can be maximized. Armed with this knowledge, enthusiasts and professionals can confidently select and implement them for various projects. The insights presented in this article underscore the essential role of hole magnets in making processes simpler, better, and more efficient.
## Frequently Asked Questions (FAQ)
### H3: What type of hole magnet offers the strongest magnetic pull?
**Answer:** Neodymium hole magnets offer the strongest magnetic pull for their size compared to other materials like ferrite, alnico, or samarium cobalt. Their high coercivity and remanence make them ideal for applications where space efficiency and holding force are paramount. However, their susceptibility to corrosion in humid environments should be considered, and appropriate coatings like nickel or epoxy should be selected when necessary.
### H3: Can temperature affect the strength of a hole magnet?
**Answer:** Yes, temperature can significantly impact the strength of a hole magnet. Each magnetic material has a Curie temperature, the point at which it loses its magnetization. Neodymium magnets, while strong, have a relatively lower Curie temperature than alnico magnets, making them more susceptible to demagnetization at high temperatures. Understanding the operating temperature range is crucial when selecting a magnet for specific application.
### H3: How do I choose the right size hole magnet for my project?
**Answer:** Selecting the right size of hole magnet depends on the required holding force, the available space, and the type of material to which the magnet will be attached. Consider the weight of the object you need to hold, the surface finish of the mounting surface, and any potential air gaps. It’s always best to overestimate the required holding force to ensure a secure and reliable hold. Refer to magnet specification charts and consult with magnet suppliers for specific recommendations.
### H3: What is the best way to attach a hole magnet to a non-metallic surface?
**Answer:** The best ways to attach a hole magnet to a non-metallic surface include epoxy adhesives, screws and bolts through the hole (often with countersinking), and mounting brackets. Epoxy adhesives provide a strong and permanent bond, while screws and bolts allow for mechanical fastening. Mounting brackets can be designed to provide additional support and stability. The specific method will depend on the application’s requirements and the type of non-metallic material.
### H3: Are there any safety precautions I should take when handling hole magnets?
**Answer:** Yes, several safety precautions should be taken when handling hole magnets, especially strong neodymium magnets. Avoid pinching fingers between magnets or between a magnet and a metal surface. Keep magnets away from sensitive electronic devices like pacemakers and credit cards. Wear eye protection to prevent injury from flying debris if the magnet chips or breaks. Store magnets safely to prevent accidental attraction to metal objects.
### H3: What coatings are available for hole magnets, and what are their benefits?
**Answer:** Common coatings for hole magnets include nickel, epoxy, zinc, gold, and chrome. Nickel is a popular choice for its good corrosion resistance and attractive appearance. Epoxy coatings provide excellent protection against moisture and chemicals. Zinc is a cost-effective option for general corrosion resistance. Gold and chrome coatings offer aesthetic appeal and enhanced durability. The choice of coating will depend on the environment in which the magnet will be used and the desired level of protection.
### H3: Can I use hole magnets outdoors?
**Answer:** Yes, you can use hole magnets outdoors, but it’s essential to choose magnets with appropriate corrosion resistance. Ferrite magnets are naturally resistant to corrosion and are well-suited for outdoor applications. Neodymium magnets, if used outdoors, should have a protective coating such as epoxy or nickel to prevent rust and deterioration. Regularly inspect magnets used outdoors for any signs of corrosion and replace them as needed.
### H3: Where can I purchase high-quality hole magnets?
**Answer:** High-quality hole magnets can be purchased from various sources, including specialized magnet suppliers, hardware stores, and online retailers like Amazon, McMaster-Carr, and Grainger. When selecting a supplier, prioritize those with a reputation for quality and reliability. Be sure to review product specifications and customer reviews before making a purchase. Some suppliers also offer custom magnet fabrication services to meet specific needs.
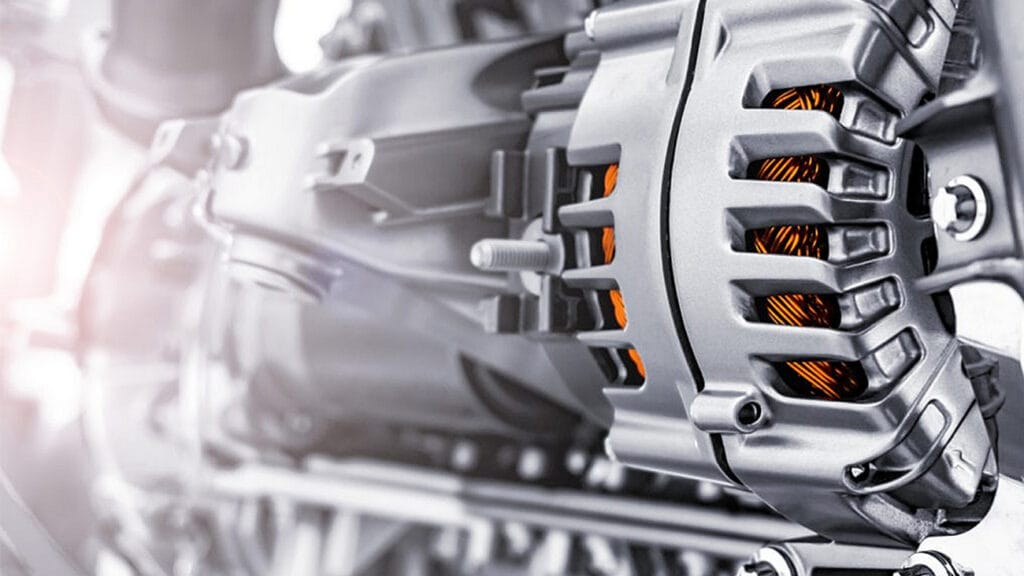