# Unlocking Efficiency: The Indispensable Role of Soft Magnetic Cores in Optimizing Power Conversion
Welcome to an in-depth exploration of a critical component in modern power electronics: **soft magnetic cores**. In our pursuit of ever-more-efficient power conversion across diverse applications – from your smartphone charger to massive industrial grids – these seemingly simple materials play an indispensable role. This article dives deep into the technical intricacies and application-specific nuances of soft magnetic cores, revealing why understanding them is paramount for engineers and anyone interested in the future of energy. Prepare to enhance your knowledge and discover how these materials are at the heart of optimizing power conversion.
## What Exactly Are Soft Magnetic Cores and Why Are They So Crucial for Power Conversion?
At the core (pun intended!) of efficient power conversion lies the ability to manipulate electromagnetic energy effectively. This is where soft magnetic cores come into play. But what are they, and why are they so fundamentally important?
Soft magnetic cores are materials engineered to exhibit specific magnetic properties that make them ideal for use in electromagnetic devices. Unlike hard magnets which retain their magnetism, soft magnetic materials are easily magnetized and demagnetized. Think of them as highly responsive conduits for magnetic flux. This characteristic is absolutely crucial for power conversion components like inductors and transformers, which are the workhorses of any power electronic circuit. Without efficient magnetic components, we simply cannot achieve the high efficiencies and compact designs demanded by modern applications. The ability to efficiently channel and concentrate magnetic fields, minimize energy losses, and operate reliably under diverse conditions makes soft magnetic cores utterly indispensable.
## How Do Different Types of Soft Magnetic Materials Impact Power Conversion Efficiency?
Now that we understand the fundamental importance of soft magnetic cores, it’s critical to recognize that not all materials are created equal. The world of soft magnetic materials is diverse, each offering a unique set of properties that directly influence power conversion efficiency. How do these differences manifest and what are some key material types?
The efficiency of power conversion is significantly affected by core losses, which are energy dissipated as heat within the magnetic core itself. Different materials exhibit varying levels of these losses, primarily categorized as hysteresis losses and eddy current losses. **Ferrites**, for instance, are ceramic materials offering high resistivity, effectively minimizing eddy current losses, especially at higher frequencies. This makes them excellent for high-frequency switch-mode power supplies found in computers and consumer electronics. On the other hand, **silicon steel laminations**, a classic material, are known for their high saturation magnetization and lower cost. While they exhibit higher eddy current losses at higher frequencies, they are still widely used at lower frequencies, such as in grid transformers. **Powder cores**, composed of fine magnetic particles bonded with a non-magnetic material, offer a distributed air gap, leading to lower core losses and better performance under DC bias, making them suitable for inductors in various power converters. Understanding these material nuances – from **amorphous alloys** with their exceptional low losses to **nanocrystalline materials** pushing performance boundaries – is key to selecting the optimal core material and maximizing power conversion efficiency for a specific application.
**Table 1: Comparison of Common Soft Magnetic Core Materials**
| Material Type | Relative Cost | Saturation Magnetization (Bs) | Core Loss (at moderate frequency) | DC Bias Performance | Applications |
|———————–|—————|——————————|———————————–|———————–|——————————————-|
| Silicon Steel | Low | High | Moderate | Good | Line frequency transformers, large inductors |
| Ferrite | Moderate | Moderate | Low (high frequency) | Fair | High frequency SMPS transformers & inductors|
| Powder Cores (Iron) | Low | Moderate | Moderate | Excellent | Inductors, PFC chokes |
| Powder Cores (Sendust)| Moderate | Moderate | Low-Moderate | Excellent | High performance inductors, filters |
| Amorphous Alloys | High | Moderate | Very Low | Good | High efficiency transformers, PFC chokes |
| Nanocrystalline | Very High | Moderate | Very Low | Excellent | High performance, compact designs |
## How Do Core Geometry and Size Influence the Performance of Power Conversion Circuits?
Material properties are just one piece of the puzzle. The **geometry and size** of a soft magnetic core significantly impact its performance within a power conversion circuit. How exactly do these physical attributes play a role?
The shape and dimensions of the core directly affect the magnetic path length, cross-sectional area, and ultimately, the inductance and saturation characteristics of the component. For instance, a **toroidal core**, with its closed magnetic path, minimizes external magnetic fields (EMI) and offers high inductance per turn, making it ideal for sensitive applications and high-density designs. **E-cores and U-cores**, with their gapped structures, are often used for transformers and inductors where a specific air gap is needed to control inductance and prevent saturation under DC bias. The core size is also critical. A larger core can handle more power without saturating, but it also increases size, weight, and potentially cost. Conversely, a smaller core might lead to saturation at higher power levels and increased core losses due to higher flux density. Furthermore, thermal management becomes more challenging with smaller cores as heat dissipation becomes concentrated. Choosing the right core geometry and size is a delicate balancing act, dictated by the specific voltage, current, frequency, and power requirements of the application. Sophisticated simulation tools and careful calculations are essential to optimize these parameters and ensure efficient and reliable power conversion.
**Diagram 1: Common Soft Magnetic Core Geometries**
(Imagine a simple diagram here showing Toroidal, E-Core, U-Core, and Pot Core shapes with labels and arrows indicating magnetic flux path for each. In text format, I can describe them:
* **Toroidal Core:** Ring-shaped, magnetic flux circulates within the ring.
* **E-Core:** E-shaped ferrite core, typically used in pairs to form a closed magnetic path with a gap in the center leg.
* **U-Core:** U-shaped ferrite core, similar to E-core used in pairs.
* **Pot Core:** Cup-shaped core enclosing the winding, offering excellent shielding.)
## What Role Does Air Gap Play in Optimizing Inductor and Transformer Performance?
The seemingly insignificant **air gap** in a magnetic core is a powerful design tool for optimizing inductor and transformer performance. Why is this seemingly deliberate imperfection so important?
Introducing an air gap into the magnetic path, particularly in inductors, dramatically alters the magnetic characteristics. The air gap, being far less magnetically permeable than the core material, becomes the dominant factor in determining the effective permeability of the magnetic circuit. This significantly reduces the overall permeability and consequently decreases the inductance for a given number of turns. However, this reduction in permeability has a crucial benefit: it increases the **saturation current**. Saturation occurs when the magnetic core can no longer accommodate increasing magnetic flux, leading to a sharp drop in inductance and potentially component failure. By introducing an air gap, we effectively “linearize” the inductance profile over a wider range of DC current. This is particularly critical in inductors that need to handle DC bias currents, such as those in buck and boost converters. In transformers, air gaps are sometimes intentionally introduced to manage leakage inductance or to adjust magnetizing inductance for specific circuit requirements. The precise size and placement of the air gap are critical design parameters that must be carefully calculated and controlled during manufacturing to achieve the desired inductor or transformer performance.
**List 1: Benefits of Air Gaps in Magnetic Cores**
* **Increased Saturation Current:** Prevents inductance roll-off at high DC currents.
* **Linear Inductance Profile:** Inductance remains relatively constant over a wider current range.
* **Controlled Inductance Value:** Allows for finer inductance adjustments in design.
* **Improved DC Bias Handling:** Essential for inductors in power converter circuits.
## How Do Core Losses Impact Overall Power Converter Efficiency and Thermal Management?
As we’ve touched upon, **core losses** are a significant factor in power conversion. But how do they directly translate into reduced efficiency and thermal management challenges?
Core losses represent energy dissipated as heat within the soft magnetic core material due to the alternating magnetic field. These losses are broadly categorized into hysteresis losses (due to magnetic domain reorientation) and eddy current losses (due to circulating currents induced within the core material). Higher core losses directly translate to reduced power converter efficiency, meaning more input power is wasted as heat instead of being converted into useful output power. This wasted energy not only increases operating costs but also presents significant **thermal management challenges**. Excessive heat within the core and surrounding components can lead to performance degradation, reduced reliability, and even device failure. Effective cooling solutions, such as heat sinks, forced air cooling, or liquid cooling, may be necessary to dissipate this heat, adding to system complexity, size, and cost. Therefore, minimizing core losses through careful material selection, optimized core design, and appropriate operating frequency is paramount for achieving high efficiency and reliable operation in power conversion systems. Lower core losses mean less heat generation, higher efficiency, and potentially smaller and more cost-effective thermal management solutions.
**Statistics and Facts:**
* Core losses can account for a significant portion (sometimes up to 20-30%) of total losses in high-frequency power converters.
* For every 10°C increase in operating temperature, the lifespan of electronic components can be reduced by half.
* Selecting a low-loss core material can improve power converter efficiency by several percentage points.
## What Are the Key Considerations When Selecting Soft Magnetic Cores for High-Frequency Applications?
Modern power electronics increasingly operate at **high frequencies** to reduce component size and improve transient response. However, high frequencies impose specific demands on soft magnetic cores. What are the crucial selection criteria for these applications?
Operating at higher frequencies exacerbates core losses, especially eddy current losses, which increase proportionally to the square of the frequency. Therefore, for high-frequency applications, **minimizing core losses becomes even more critical**. Materials with high resistivity, such as ferrites and some specialized powder cores, are often preferred to reduce eddy current losses. The **frequency dependence of core losses** must be carefully considered; datasheets typically provide core loss curves at different frequencies. **Saturation magnetization** also plays a vital role. At higher frequencies, the core may experience faster flux changes, potentially leading to saturation if the flux density exceeds the material’s saturation limit. **Temperature stability** is another key factor, as core losses and permeability can vary with temperature. The core material should maintain stable performance over the expected operating temperature range. **Skin effect** in windings also becomes more pronounced at higher frequencies, necessitating the use of Litz wire or other techniques to minimize AC resistance. In summary, selecting soft magnetic cores for high-frequency applications requires a meticulous evaluation of core losses across frequency and temperature, saturation characteristics, and compatibility with winding techniques suitable for high-frequency currents.
## How Can Advanced Soft Magnetic Materials Push the Boundaries of Power Conversion?
The relentless drive for higher efficiency and power density is fueling innovation in **advanced soft magnetic materials**. What cutting-edge materials are emerging and how are they revolutionizing power conversion?
Researchers are continuously developing novel soft magnetic materials with enhanced properties that push the boundaries of power conversion. **Nanocrystalline alloys**, produced through specialized rapid solidification processes, exhibit exceptionally low core losses and high permeability even at high frequencies and temperatures. Their fine grain structure minimizes hysteresis and eddy current losses, enabling high-efficiency, compact designs. **Amorphous alloys**, with their disordered atomic structure, also boast very low core losses, particularly at higher frequencies, and are increasingly being used in high-performance transformers and inductors. Efforts are also underway to improve traditional materials like **ferrites** by optimizing their composition and processing techniques to further reduce losses and enhance saturation magnetization. **Metal composite materials (MCMs)** are gaining traction, offering a blend of metallic properties with the distributed air gap advantages of powder cores, potentially bridging the gap between ferrite and powder core performance. These advanced materials are enabling power converters to operate at higher frequencies with significantly reduced losses, paving the way for smaller, lighter, and more efficient power electronic systems across various applications, from electric vehicles to renewable energy integration.
**Case Study 1: Nanocrystalline Cores in Electric Vehicle Chargers**
Electric vehicle chargers demand high efficiency and power density. By replacing conventional ferrite cores with nanocrystalline cores in the charging circuits, manufacturers have achieved:
* **Increased Efficiency:** Efficiency improvements of 1-2% at high power levels, reducing energy waste and heat generation.
* **Reduced Size and Weight:** Smaller and lighter charger designs due to higher operating frequency enabled by lower losses.
* **Improved Thermal Performance:** Lower core losses translate to less heat dissipation, simplifying thermal management and enhancing reliability.
## What Design Techniques Can Further Optimize the Performance of Soft Magnetic Core Based Components?
Beyond material selection, **design techniques** play a crucial role in maximizing the performance of soft magnetic core-based components. What are some key optimization strategies that engineers employ?
Optimizing the design of inductors and transformers involves a multi-faceted approach. **Finite Element Analysis (FEA) simulations** are powerful tools for analyzing magnetic flux distribution within the core, identifying areas of flux concentration, and optimizing core geometry to minimize leakage inductance and core losses. **Winding optimization** is equally important. Techniques like interleaving windings, using Litz wire in high-frequency applications, and minimizing parasitic capacitances can significantly improve performance and reduce losses. Careful consideration of **thermal management** during the design phase is crucial. This includes optimizing core and winding geometry for better heat dissipation, selecting appropriate mounting techniques, and incorporating heat sinks or cooling solutions where necessary. **Planar magnetics** are another design innovation, offering low profile designs, improved thermal performance, and high repeatability, especially beneficial in high-density power converters. Furthermore, advanced control techniques implemented in power converter controllers can also mitigate some imperfections in magnetic components, improving overall system performance. Optimal design is an iterative process involving simulation, prototyping, and testing to fine-tune parameters and achieve the best balance between performance, size, cost, and reliability.
**Diagram 2: Finite Element Analysis (FEA) Simulation of Magnetic Flux in an E-Core Transformer**
(Imagine a simple color-coded diagram here showing an E-core transformer in cross-section, with flux lines visualized using colors. Areas of high flux density could be highlighted in red, lower density in blue, demonstrating how FEA helps visualize flux distribution and identify potential design improvements.)
## How Do Soft Magnetic Cores Contribute to the Reliability and Longevity of Power Electronic Systems?
While efficiency is paramount, **reliability and longevity** are equally critical for power electronic systems operating in diverse and often demanding environments. How do soft magnetic cores influence these aspects?
The choice and proper application of soft magnetic cores directly impact the reliability and lifespan of power converters. **Operating temperature** is a major factor affecting long-term reliability. Lower core losses, as discussed earlier, lead to lower operating temperatures, reducing thermal stress on the core material, windings, and surrounding components. **Material stability** over temperature and time is also crucial. Some materials may exhibit changes in permeability or increased losses with prolonged exposure to elevated temperatures or humidity. Selecting materials with proven long-term stability is essential, especially in harsh operating conditions. **Saturation avoidance** is another critical aspect. Operating the core close to or in saturation can lead to increased core losses, overheating, and eventual degradation of the magnetic properties. Proper core sizing and air gap design are vital to prevent saturation even under transient overload conditions. Furthermore, the **mechanical integrity** of the core and its mounting are important, particularly in vibration-prone environments. Cracking or damage to the core can significantly degrade performance. By carefully considering these factors during the design and material selection process, engineers can ensure that soft magnetic cores contribute significantly to the overall reliability and longevity of power electronic systems.
## What are Some Emerging Applications Where Optimized Soft Magnetic Cores Are Making a Significant Impact?
The benefits of optimized soft magnetic cores are being realized across a rapidly expanding range of **emerging applications**. Where are these materials making the most significant impact beyond traditional power supplies?
Beyond traditional power supplies and motor drives, optimized soft magnetic cores are playing a pivotal role in enabling advancements in several exciting fields:
* **Renewable Energy Systems:** In solar inverters and wind turbine converters, high-efficiency transformers and inductors based on advanced soft magnetic materials are crucial for maximizing energy capture and grid integration.
* **Electric Vehicles (EVs):** On-board chargers, DC-DC converters, and traction inverters in EVs demand high power density and efficiency. Advanced cores are enabling smaller, lighter, and more efficient power electronic systems in electric vehicles, extending driving range and reducing charging times.
* **Wireless Power Transfer (WPT):** Soft ferrite cores with specific permeability characteristics are essential for efficient magnetic resonant WPT systems used in charging smartphones, wearables, and even electric vehicles wirelessly.
* **High-Speed Data Centers:** Power supplies for data centers require extremely high efficiency to minimize energy consumption. Low-loss soft magnetic cores contribute significantly to reducing energy waste and improving the overall energy efficiency of data centers.
* **Medical Devices:** Compact and highly efficient power converters are crucial for portable and implantable medical devices. Advanced soft magnetic cores enable smaller, lighter, and more efficient power solutions for these critical applications.
* **Aerospace and Defense:** Weight and size are paramount in aerospace applications. High-performance soft magnetic cores contribute to developing compact and lightweight power electronic systems for aircraft, satellites, and defense equipment.
These emerging applications highlight the growing importance of soft magnetic cores as enablers of innovation across diverse sectors, driving efficiency, performance, and miniaturization in power electronics.
## FAQ Section: Common Questions About Soft Magnetic Cores
**What is permeability and why is it important for soft magnetic cores?**
Permeability is a measure of how easily a material can be magnetized, essentially its ability to concentrate magnetic flux. In soft magnetic cores, high permeability is desirable because it allows for the creation of strong magnetic fields with fewer winding turns and lower magnetizing current. This leads to higher inductance, reduced component size, and improved efficiency, particularly in transformers and inductors.
**How do I choose between ferrite and powder cores for my inductor application?**
The choice depends largely on the application requirements, particularly frequency and DC bias. Ferrites excel at high frequencies due to their low core losses but are more susceptible to saturation under DC bias. Powder cores generally handle DC bias better due to their distributed air gap and can operate at moderate to high frequencies, although ferrite typically has lower high-frequency losses. Consider frequency, DC current, desired inductance stability, and cost when making this decision.
**Are soft magnetic cores susceptible to temperature changes and how can I mitigate this?**
Yes, the properties of soft magnetic cores, including permeability and core losses, can be temperature-dependent. Ferrites, for example, often exhibit a Curie temperature beyond which they lose their ferromagnetic properties. To mitigate temperature effects, choose materials with good temperature stability within the operating range, design for lower operating temperatures by minimizing losses, and consider using temperature compensation circuits if necessary. Datasheets provide temperature characteristics of core materials to aid in selection.
**What is ‘skin effect’ and how does it relate to soft magnetic core components at high frequencies?**
Skin effect is a phenomenon where AC current tends to flow primarily on the surface of a conductor at higher frequencies, reducing the effective cross-sectional area and increasing AC resistance. In windings of soft magnetic core components operating at high frequencies, skin effect can significantly increase winding losses. To mitigate skin effect, Litz wire (composed of many individually insulated thin strands) is often used for windings, as it provides a larger effective surface area for current flow.
**Can I use too large of a soft magnetic core? What are the drawbacks?**
While a larger core might seem intuitively better for handling power, it also comes with drawbacks. Larger cores are heavier, more expensive, and take up more space. They can also increase parasitic capacitances in windings and may not be optimal for high-frequency applications due to increased eddy current losses associated with larger volumes of core material. Over-designing with an excessively large core is generally inefficient and adds unnecessary cost and size to the system. Optimal core size is always a balance of performance, cost, and size constraints.
## Conclusion: Key Takeaways on the Indispensable Role of Soft Magnetic Cores
* **Soft magnetic cores are fundamental to efficient power conversion**, enabling the creation of inductors and transformers that are essential in virtually all power electronic circuits.
* **Material selection is critical**, with Ferrites, Silicon Steel, Powder Cores, Amorphous Alloys, and Nanocrystalline materials offering diverse properties for different applications.
* **Core geometry and size significantly influence performance**, impacting inductance, saturation, and EMI characteristics.
* **Air gaps are a powerful design tool** for controlling inductance and improving DC bias performance, particularly in inductors.
* **Core losses directly impact efficiency and thermal management**, necessitating careful material selection and design optimization to minimize heat generation.
* **Advanced soft magnetic materials and design techniques** are continuously pushing the boundaries of power conversion, enabling higher efficiency, power density, and reliability in a wide range of applications.
* **Optimized soft magnetic cores are enablers of innovation** in emerging fields such as renewable energy, electric vehicles, wireless power transfer, and more.
As we continue to demand more from our power electronic systems – higher efficiency, smaller size, greater reliability – the indispensable role of soft magnetic cores will only become more pronounced. Understanding their nuances and leveraging their potential is crucial for anyone involved in the design, development, and application of power conversion technology.
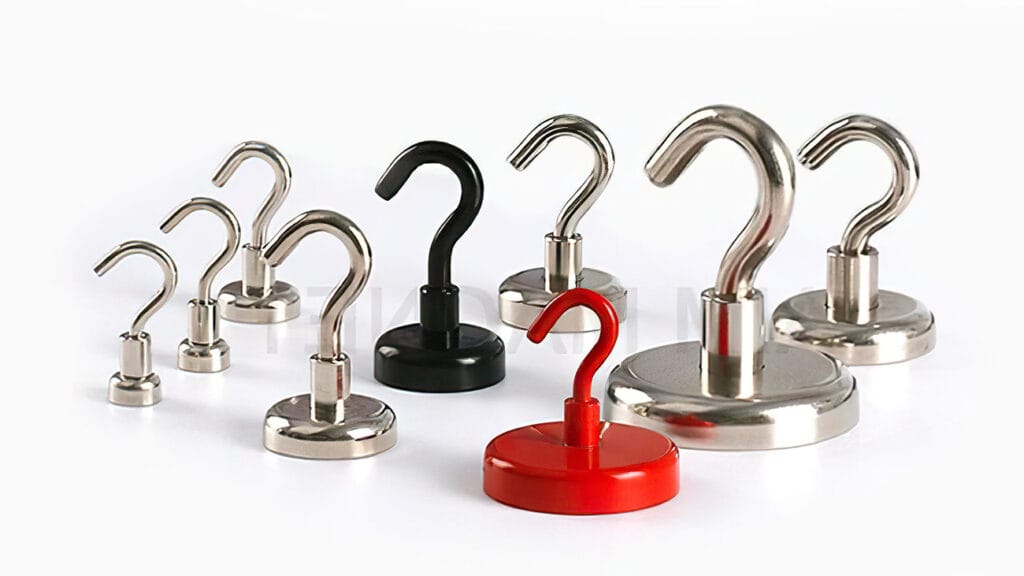