# Ferrite vs. Rare Earth Magnets: A Deep Dive into Strengths, Weaknesses, and Applications
**Summary:** This article provides a comprehensive comparison between ferrite and rare earth magnets, exploring their distinct properties, strengths, weaknesses, and suitable applications. Whether you’re an engineer choosing magnets for a specific project, a student learning about magnetism, or simply curious about the technology behind common devices, this guide will offer valuable insights to help you understand the differences and make informed decisions. We’ll delve into their magnetic force, cost-effectiveness, temperature resistance, and more.
## Understanding the Basics: Ferrite and Rare Earth Magnet Composition
Ferrite magnets, also known as ceramic magnets, are composed primarily of iron oxide (Fe2O3) and barium or strontium carbonate. The manufacturing process involves sintering these materials, which is a heat treatment process that fuses the particles together without melting them. This results in a relatively inexpensive and chemically stable magnet. Ferrite magnets are characterized by their dark gray color and are commonly found in applications such as loudspeakers, electric motors, and magnetic separators. The aligned magnetic domains within the ferrite structure contribute to its overall magnetic properties.
Rare earth magnets, on the other hand, are composed of alloys containing rare earth elements like neodymium (Nd) or samarium (Sm). The two main types are neodymium magnets (NdFeB) and samarium cobalt magnets (SmCo). Neodymium magnets are the most powerful type of permanent magnet available commercially, offering superior magnetic strength compared to ferrite magnets. Samarium cobalt magnets offer a better performance in high temperature environments compared to neodymium magnets, although they are generally more expensive and slightly weaker in strength compared to neodymium magnets at room temperature. The complex crystalline structure of rare earth alloys combined with the strong magnetic moments of the rare earth elements provide their exceptional magnetic properties.
## Magnetic Strength: A Comparison of Gauss and Coercivity
The magnetic strength of a magnet is determined by several factors, including its remanence (Br), coercivity (Hc), and energy product (BHmax). Remanence refers to the residual magnetism remaining in a magnet after the applied magnetizing force is removed. Coercivity represents the magnet’s resistance to demagnetization by an external magnetic field. The energy product, BHmax, is a measure of the amount of energy that a magnet can store and is directly related to its overall performance.
Rare earth magnets, particularly neodymium magnets, possess significantly higher remanence, coercivity, and energy product values compared to ferrite magnets. This translates to a much stronger magnetic field strength for a given size. For example, a small neodymium magnet can exert a force that far exceeds that of a much larger ferrite magnet. While ferrite magnets are suitable for applications where moderate magnetic strength is sufficient, rare earth magnets are preferred for applications requiring maximum magnetic force in a compact form factor. Think of tiny, powerful motors in electronics and highly efficient energy generation.
## Cost Considerations: Affordability and Price Volatility
Cost is a crucial factor in magnet selection. Ferrite magnets are generally much more cost-effective than rare earth magnets. This is due to the relatively inexpensive raw materials and simpler manufacturing processes involved in their production. The widely abundant nature of iron oxide compared to the relatively scarcer rare earth elements greatly contributes to this cost difference. For high-volume applications where magnetic strength is not the primary concern, ferrite magnets often provide the most economical solution.
Rare earth magnet prices, especially for neodymium magnets, are subject to greater price volatility due to geopolitical factors and fluctuations in the supply and demand of rare earth elements. China controls a significant portion of the world’s rare earth element production, which can influence global prices. In contrast, the cost of ferrite magnets tends to be more stable, making them a more predictable choice from a budgetary perspective, especially in long-term production planning or when designing products intended for mass market sale to price-conscious customers.
## Temperature Sensitivity: High-Heat Performance Evaluation
Temperature significantly impacts the performance of magnets. As temperature increases, the magnetic properties of any permanent magnet diminish. This phenomenon, known as thermal demagnetization, occurs because increased thermal energy can disrupt the alignment of magnetic domains within the material. The Curie temperature is the temperature at which a magnet completely loses its magnetism.
Ferrite magnets exhibit good temperature stability and can operate effectively at higher temperatures compared to some grades of neodymium magnets. While neodymium magnets offer superior strength at room temperature, their performance can degrade significantly at elevated temperatures. Samarium cobalt magnets, another type of rare earth magnet, offer better temperature stability than neodymium magnets but are typically more expensive and slightly weaker at room temperature. Selecting the right magnet for high-temperature applications requires careful consideration of operating conditions and magnetic performance requirements. Certain specialized neodymium alloys can be formulated to improve high-temperature performance, but this typically comes at a higher cost.
## Corrosion Resistance: Environmental Durability Analysis
Corrosion resistance is an important consideration, especially for magnets used in harsh environments. Ferrite magnets possess excellent corrosion resistance due to their ceramic nature. They are generally inert to most chemicals and resistant to oxidation. This makes them suitable for applications where magnets are exposed to moisture, salt spray, or other corrosive agents.
Rare earth magnets, particularly neodymium magnets, are more susceptible to corrosion than ferrite magnets. Neodymium reacts readily with oxygen and other elements, leading to degradation of the magnet’s surface and eventual loss of magnetic performance. To mitigate this issue, neodymium magnets are typically coated with protective layers such as nickel, epoxy, or zinc. The effectiveness of these coatings depends on the specific environment and the quality of the coating application. Samarium cobalt magnets exhibit better corrosion resistance than neodymium magnets due to the inherent chemical stability of the samarium cobalt alloy.
## Applications: Matching Magnets to Real-World Uses
The distinct properties of ferrite and rare earth magnets dictate their suitability for various applications. Ferrite magnets are widely used in loudspeakers, electric motors (especially in lower-power applications), magnetic separators, and holding magnets. Their affordability and adequate magnetic strength make them a practical choice for these applications. Magnetic separators are used in mining, food processing and recycling to separate ferrous metals from non-ferrous.
Rare earth magnets are employed in applications requiring high magnetic strength in a compact size. Examples include hard disk drives, magnetic resonance imaging (MRI) machines, wind turbine generators, electric vehicle motors, and high-performance audio equipment. The superior magnetic performance of rare earth magnets enables the miniaturization of devices and improves their efficiency. Think of the powerful torque generated by small DC motors in electric vehicles that could not be possibly achieved with a ferrite magnet of the same dimensions. Modern medical imaging devices also rely on the exceptional magnetic fields produced by rare earth magnet systems.
## Manufacturing Processes: Sintering vs. Other Techniques and Tolerances
Ferrite magnets are typically manufactured using a powder metallurgy process called sintering. This involves mixing iron oxide and barium or strontium carbonate powders, compacting them under high pressure, and then heating them to a high temperature (typically between 1100°C and 1300°C) in a controlled atmosphere. The sintering process fuses the particles together, forming a solid, dense magnet. Ferrite magnets produced through sintering have relatively loose dimensional tolerances compared to machined metal components.
Rare earth magnets, both neodymium and samarium cobalt, are also manufactured using powder metallurgy techniques, but the process is more complex and involves tighter controls. The raw materials are melted together, rapidly cooled to form a fine powder, and then compacted and sintered in a similar manner to ferrite magnets. However, rare earth magnet manufacturers often employ additional steps such as hot pressing or die upsetting to improve the density and magnetic properties of the final product. Grinding or machining are often required to achieve the required precise dimensions and tolerances. The precision required in the rare earth magnet manufacturing process contributes to their higher cost.
## Shape and Size Limitations: Design Constraints
The manufacturing processes and material properties impose certain limitations on the shapes and sizes of magnets that can be produced. Ferrite magnets are relatively brittle and difficult to machine. As a result, they are typically manufactured in simple shapes such as blocks, rings, and discs. The limitations in machinability make it difficult to produce intricate or complex shapes with ferrite magnets. Large ferrite magnets are also more prone to cracking during the sintering process.
Rare earth magnets can be manufactured in a wider range of shapes and sizes compared to ferrite magnets. While they also exhibit some degree of brittleness, they can be more easily machined using specialized techniques such as wire EDM (electrical discharge machining). This allows for the production of magnets with complex geometries and tight tolerances. The ability to create small, strong magnets with intricate shapes is a key advantage of rare earth magnets in applications where space is limited.
## Environmental Impact: Sustainability and Responsible Sourcing
The environmental impact of magnet production is a growing concern. Ferrite magnet production generally has a lower environmental impact compared to rare earth magnet production. The raw materials for ferrite magnets are relatively abundant and the manufacturing process consumes less energy. However, concerns exist about the mining and processing of iron ore and the potential for air and water pollution during the sintering process. Waste recycling of ferrite magnets is becoming more common.
Rare earth magnet production has a greater environmental impact due to the energy-intensive mining and processing of rare earth elements. The extraction of rare earth elements can generate significant amounts of toxic waste and can lead to environmental degradation if not managed properly. Responsible sourcing of rare earth elements is crucial to minimizing the environmental impact of rare earth magnet production. Developing more efficient recycling technologies for rare earth magnets is also essential for promoting sustainability. Many industries are striving to establish more robust closed-loop recycling of rare earth containing components to reduce the dependence on the environmentally sensitive mining of new ores.
## Conclusion
Choosing between ferrite and rare earth magnets involves careful consideration of magnetic strength, cost, temperature sensitivity, corrosion resistance, application requirements, and environmental impact. Ferrite magnets offer a cost-effective solution for applications where moderate magnetic strength is sufficient, while rare earth magnets provide superior performance for applications requiring maximum magnetic force in a compact size. Understanding the strengths and weaknesses of each type of magnet allows engineers and designers to make informed decisions that balance performance, cost, and sustainability. The selection process should also account for the environmental conditions and potential long-term degradation of the magnet materials. As technology advances, new magnet materials and manufacturing processes continue to emerge, further expanding the range of available options. A good engineering practice is to regularly review the advancements in magnet alloys and fabrication technologies to ensure that the optimal magnet solution is being implemented.
## FAQ
### How do I determine if a magnet is ferrite or neodymium without special equipment?
While not foolproof, you can try a few simple tests. Neodymium magnets are significantly stronger than ferrite magnets of the same size. If a small magnet has surprising strength, it’s likely a neodymium magnet. Also, neodymium magnets often have a metallic sheen and are usually coated with nickel or other materials, whereas ferrite magnets are typically dark gray and have a more matte finish. You can also try scratching the magnet on a rough surface. Ferrite magnets tend to leave a dark streak, while neodymium magnets leave a lighter, metallic streak if the coating is compromised.
### Are all rare earth magnets created equal?
No. There are primarily two categories of rare earth magnets: neodymium (NdFeB) and samarium cobalt (SmCo). Neodymium magnets are typically stronger but have lower temperature resistance and corrosion resistance compared to samarium cobalt magnets. Within each category, different grades exist with varying magnetic properties and performance characteristics. The specific composition and manufacturing process determine the final properties of the magnet.
### Can I reuse or recycle magnets?
Yes, magnets can be reused and recycled, although the recycling process for rare earth magnets is more complex and costly than for ferrite magnets. Reusing magnets in new applications is often the most cost-effective and environmentally friendly option. Several companies specialize in recycling rare earth magnets, recovering the rare earth elements for use in new magnets or other applications. Increased recycling efforts are crucial for reducing the environmental impact of rare earth magnet production.
### Which type of magnet is better for electric motors?
The choice between ferrite and rare earth magnets for electric motors depends on the specific application requirements. Ferrite magnets are often used in lower-power motors where cost is a major consideration. Rare earth magnets, particularly neodymium magnets, are preferred for high-performance motors that require high power density and efficiency. Electric vehicle motors and servo motors typically utilize rare earth magnets to achieve their desired performance characteristics. The efficiency gains provided by rare earth magnets can significantly improve the range and performance of electric vehicles.
### What are the limitations of ferrite magnets?
The main limitations of ferrite magnets are their relatively low magnetic strength compared to rare earth magnets and their brittleness. They are also susceptible to demagnetization at high temperatures. However, ferrite magnets offer excellent corrosion resistance and are a cost-effective option for many applications where high magnetic strength is not required.
### How do coatings affect the performance of neodymium magnets?
Coatings protect neodymium magnets from corrosion, which can significantly degrade their performance and lifespan. Common coatings include nickel, epoxy, and zinc. The type and quality of the coating affect its durability and resistance to different environmental conditions. A well-chosen and properly applied coating is essential for maintaining the long-term performance of neodymium magnets.
### Are there any health concerns associated with handling rare earth magnets?
While rare earth magnets themselves are generally not toxic, the strong magnetic fields they produce can interfere with medical devices such as pacemakers. It is important to handle rare earth magnets with care and avoid placing them near sensitive electronic equipment or medical implants. Swallowing small neodymium magnets can also pose a serious health hazard, especially for children.
### What are some emerging technologies in magnet materials?
Research and development efforts are focused on developing new magnet materials with improved performance, lower cost, and reduced environmental impact. Examples include nanocomposite magnets, bonded magnets with enhanced properties, and magnets based on alternative rare earth elements. The development of more sustainable and cost-effective magnet materials is crucial for meeting the growing demand for magnets in various industries.
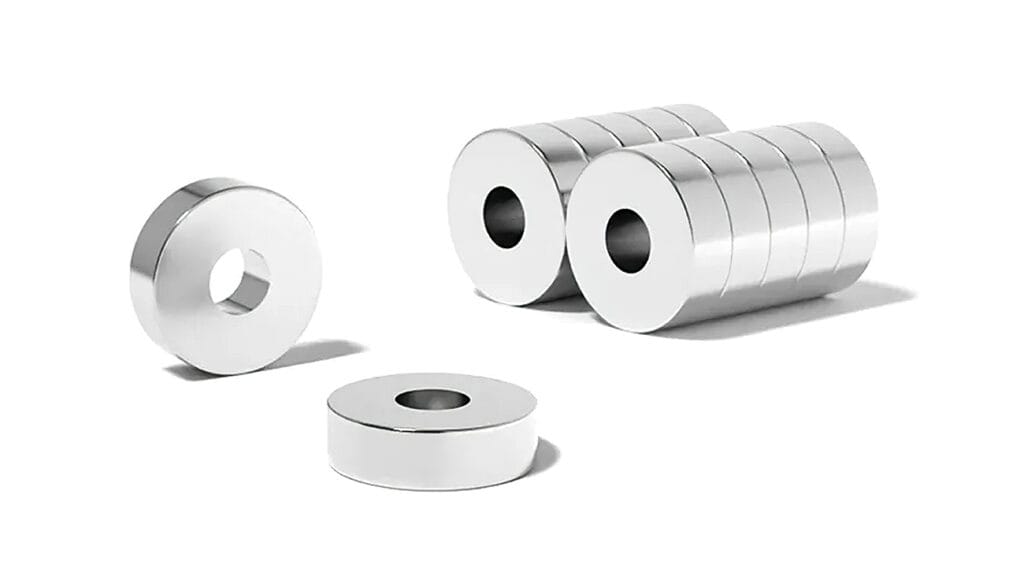