# Unlocking the Potential of Hole Magnets: A Comprehensive Guide to Applications, Materials, and Best Practices
This guide provides a deep dive into the world of hole magnets, exploring their unique properties, diverse applications, the materials they’re made from, and best practices for using them effectively. Whether you’re an engineer, hobbyist, or simply curious about magnets, this comprehensive resource will unlock the potential of hole magnets for your projects.
## 1. Understanding the Unique Properties of Hole Magnets
Hole magnets, also known as countersunk magnets or ring magnets, differ from standard magnets due to their central aperture. This seemingly simple alteration significantly expands their functionality and application possibilities. The presence of a hole allows for mechanical fastening, easier alignment, and creative mounting options, making them incredibly versatile.
The hole doesn’t just serve as a physical feature; it also affects the magnetic field. While the overall magnetic strength might be slightly reduced compared to a solid magnet of the same size (primarily due to the removed magnetic material), the field distribution changes. This altered distribution can be advantageous in specific applications, allowing for more focused or directional magnetic force. Understanding this nuanced difference is crucial for optimal application design.
Furthermore, the shape and size of the hole influence the holding force. A shallow countersunk hole, for example, will allow a flat-head screw to sit flush, maximizing the surface contact between the magnet and the mounting surface. Understanding the interplay between hole geometry, magnet material, and the intended application is key to selecting the right hole magnet for the job.
## 2. Exploring Diverse Applications Across Industries
Hole magnets find applications in a vast array of industries, demonstrating their adaptability and usefulness. From simple household solutions to complex industrial machinery, their unique properties make them invaluable components.
In the manufacturing sector, they’re often used in jigs and fixtures, providing strong and reliable holding forces for parts during assembly. Their ability to be easily mounted with screws simplifies the creation of custom holding solutions for specialized machinery. Imagine robotic arms equipped with hole magnets securely gripping and manipulating metal parts, or custom-built shelving systems that rely on magnetic latches concealed behind elegant hardware.
Beyond manufacturing, hole magnets are essential in signage and display systems. They offer a discreet and powerful way to attach signs to metal surfaces without requiring permanent fixings. This is particularly useful in retail environments where displays need to be frequently changed. Consider exhibition stands with magnetically attached panels, or retail displays that can be easily rearranged thanks to strategically placed hole magnets. The possibilities are practically limitless.
## 3. Delving into the Materials Used in Hole Magnet Production
The choice of material significantly impacts the performance and suitability of a hole magnet for a given application. The most common materials used include neodymium, ferrite, samarium cobalt, and alnico. Each boasts distinct characteristics regarding strength, temperature resistance, and cost.
Neodymium magnets, also known as NdFeB magnets, are the strongest type of permanent magnet available. Their high magnetic energy product allows for smaller magnets to deliver impressive holding forces. This makes them ideal for applications where size and weight are critical constraints. However, they are more susceptible to corrosion and have a lower temperature resistance compared to other materials.
Ferrite magnets offer a more economical alternative. They’re less powerful than neodymium magnets but exhibit excellent corrosion resistance and operate well at higher temperatures. These properties make them suitable for outdoor applications and environments with potentially corrosive substances. They are commonly used in motors, loudspeakers, and various fastening applications.
Samarium Cobalt (SmCo) magnets boast exceptional temperature stability and excellent resistance to corrosion. Although more expensive than neodymium and ferrite, their performance in harsh environments justifies the added cost in specialized applications, particularly in aerospace and defense industries.
Alnico magnets, an alloy of aluminum, nickel, and cobalt, retain their magnetism at extremely high temperatures, making them ideal for applications such as sensors and high-temperature motors. While not as strong as neodymium or samarium cobalt, they offer unparalleled temperature stability.
## 4. Selecting the Right Size and Strength for Your Project
Choosing the appropriate size and strength of a hole magnet is critical for achieving the desired performance and avoiding potential problems. Factors such as the weight of the object being held, the material of the mounting surface, and the required holding force must be carefully considered.
A magnet that is too small or too weak will fail to provide adequate holding force, potentially leading to slippage or detachment. Conversely, a magnet that is excessively strong may be difficult to detach, causing damage to the mounting surface or the object being held. Calculating the required holding force involves understanding the weight being supported and any additional forces acting upon it (e.g., wind, vibrations).
The type of mounting surface also plays a significant role. A smooth, flat surface will provide better contact and higher holding force compared to a rough or uneven surface. The material of the mounting surface also matters; ferrous materials (containing iron) will interact strongly with the magnet, while non-ferrous materials will not be attracted.
Consider using a force gauge to experimentally measure the holding force of a magnet in your specific application. This will provide valuable data to inform your selection and minimize the risk of under or over-sizing the magnet.
## 5. Mastering Mounting Techniques for Optimal Performance
Proper mounting is crucial for maximizing the holding power and ensuring the longevity of hole magnets. Several techniques can be employed, depending on the application and the desired level of permanence.
Screws are the most common method for mounting hole magnets. Using screws that fit snugly into the countersunk hole ensures a secure and flush fit, maximizing the contact area between the magnet and the mounting surface. The type of screw head (e.g., flat head, pan head) should match the countersink angle of the magnet for optimal performance.
Adhesive bonding offers an alternative method for mounting magnets, particularly when drilling holes is not feasible. Ensure the adhesive is compatible with both the magnet material and the mounting surface. Roughening the surfaces before applying the adhesive can improve bonding strength. Consider using epoxy adhesives for high-strength and durable bonds.
Mechanical retention, such as using a press-fit or interference fit, can also be employed for mounting magnets into housings or enclosures. This technique requires precise machining to ensure a tight fit and prevent the magnet from dislodging.
## 6. Addressing Common Challenges: Corrosion and Demagnetization
Two primary challenges that can affect the performance of hole magnets are corrosion and demagnetization. Understanding these challenges and implementing preventative measures is crucial for maintaining the long-term functionality of magnets.
Corrosion can degrade the magnetic properties and structural integrity of magnets, particularly neodymium magnets. Protective coatings, such as nickel, zinc, or epoxy, can significantly enhance corrosion resistance. Selecting magnets made from inherently corrosion-resistant materials, such as ferrite or samarium cobalt, is another effective strategy.
Demagnetization occurs when a magnet is exposed to excessive heat, strong opposing magnetic fields, or physical shock. The Curie temperature, the temperature at which a magnet loses its magnetism, varies depending on the material. Operating magnets within their specified temperature range is essential to prevent irreversible demagnetization. Avoid exposing magnets to strong electrical currents or powerful external magnetic fields.
For applications involving potentially harsh environments, consider using magnets with higher temperature ratings and enhanced corrosion protection. Regular inspection of magnets can help identify early signs of corrosion or demagnetization, allowing for timely replacement or preventative maintenance.
## 7. Customization Options: Meeting Specific Project Needs
While standard hole magnets are readily available, customization options allow for tailoring magnets to meet specific project requirements. These options include custom sizes, shapes, hole geometries, and coatings.
Custom sizes and shapes enable the creation of magnets that perfectly fit within existing designs or accommodate specific spatial constraints. Complex shapes can be achieved through machining or molding processes.
Custom hole geometries, such as tapered holes or threaded holes, can facilitate specific mounting configurations or allow for the integration of other components.
Custom coatings provide enhanced protection against corrosion, abrasion, or other environmental factors. Different coating materials and thicknesses can be selected based on the specific application requirements.
Consulting with a magnet manufacturer can provide valuable insights into the available customization options and help determine the optimal solution for your project.
## 8. Safety Considerations When Working with Hole Magnets
Working with strong magnets, especially neodymium magnets, requires certain safety precautions to prevent injuries and damage to equipment.
Pinch points are a primary concern. Strong magnets can rapidly attract to each other or to ferrous materials, potentially trapping fingers or skin between them. Always handle magnets with care and wear gloves to protect your hands. Keep magnets away from children.
Magnets can interfere with electronic devices, such as pacemakers and credit cards. Keep magnets away from sensitive electronic equipment. Avoid exposing magnets to strong electrical currents, as this can generate heat and potentially damage the magnet.
When shipping magnets, follow all applicable regulations regarding packaging and labeling to prevent interference with navigation systems or other sensitive equipment. Use appropriate shielding materials to minimize the external magnetic field.
Properly store magnets to prevent accidental attraction and potential damage. Keep magnets away from flammable materials, as friction between magnets can generate sparks.
## 9. The Future of Hole Magnet Technology: Innovations and Trends
The field of magnet technology is constantly evolving, with ongoing research and development focused on improving performance, reducing costs, and expanding the range of applications. Emerging trends include the development of stronger and more temperature-resistant magnet materials, the integration of magnets with sensors and other electronic components, and the use of additive manufacturing (3D printing) to create custom magnet shapes and geometries.
Researchers are actively exploring new alloys and processing techniques to enhance the magnetic properties of existing materials and develop entirely new classes of magnets. The goal is to create magnets that are both stronger and more stable, capable of operating in extreme environments.
The integration of magnets with sensors and other electronic components opens up new possibilities for smart devices and automated systems. For example, magnets can be used to trigger sensors to detect position, movement, or magnetic fields.
Additive manufacturing offers a completely new approach to magnet design and fabrication. 3D printing allows for the creation of complex magnet shapes and geometries that were previously impossible to manufacture using traditional methods. This technology enables the creation of custom magnets tailored to specific application requirements.
## 10. Sourcing High-Quality Hole Magnets: Finding Reliable Suppliers
Sourcing high-quality hole magnets from reputable suppliers is essential for ensuring optimal performance and longevity. Look for suppliers that offer a wide range of magnet materials, sizes, and shapes, and that have a proven track record of providing reliable products.
Consider suppliers that offer technical support and assistance in selecting the right magnet for your application. A knowledgeable supplier can provide valuable insights into magnet properties, mounting techniques, and safety considerations.
Request material certifications and test reports to verify the quality and performance of the magnets. These documents should provide information about the magnet’s magnetic properties, dimensions, and material composition.
Compare prices from different suppliers, but prioritize quality over cost. A cheaper magnet may not perform as well or last as long as a higher-quality magnet, potentially leading to costly replacements or repairs.
Check online reviews and testimonials to get a sense of the supplier’s reputation and customer service. A reliable supplier will have a history of providing excellent products and support to its customers.
**Συμπεράσματα**
Hole magnets offer a unique combination of strength and versatility, making them indispensable components in a wide range of applications. By understanding their properties, selecting the right materials, mastering mounting techniques, and addressing potential challenges, you can unlock the full potential of hole magnets for your projects. Staying informed about the latest innovations and sourcing magnets from reputable suppliers will ensure that you have access to the best possible products and support.
## FAQ
### What is the difference between a hole magnet and a regular magnet?
A hole magnet has a hole through its center, which allows for mechanical fastening with screws or bolts. This allows for easier mounting and integration into various systems compared to standard magnets that rely solely on adhesive or friction.
### What are the main applications of hole magnets?
Hole magnets are used in a variety of applications, including:
* Manufacturing: Jigs, fixtures, and automated machinery.
* Signage and Displays: Attaching signs and displays to metal surfaces.
* DIY Projects: Securing objects, creating magnetic latches, and building custom tools.
* Holding: Door catches, cabinet closures and much more
### Which magnet material is best for high-temperature applications?
Alnico magnets have the highest temperature resistance, making them suitable for applications where the magnet will be exposed to high temperatures, such as sensors and high-temperature motors.
### How do I choose the right size and strength of hole magnet?
Consider the weight of the object you need to hold, the material of the surface it will attach to, and any additional forces acting on the connection like vibrations or wind. Opt for a test fit to determine the actual holding force after installation.
### How can I protect hole magnets from corrosion?
Use magnets coated with corrosion-resistant materials like nickel, zinc, or epoxy. Alternatively, choose magnets made from inherently corrosion-resistant materials like ferrite or samarium cobalt. Proper cleaning and maintenance can also help prevent corrosion.
### What are the safety precautions I should take when working with hole magnets?
Be careful not to pinch your skin between magnets or between a magnet and a metal object, and keep magnets away from children and electronic devices. Store magnets carefully to prevent them from attracting to each other or to other metal objects, which could cause damage or injury.
### Can hole magnets be customized?
Yes, hole magnets can be customized in terms of size, shape, hole geometry, and coating material. This allows for tailoring magnets to meet specific project requirements.
### How is the magnetic field affected by drilling a hole in a magnet?
Drilling a hole in a magnet will reduce the overall strength of the magnet because you have removed some of the magnetic material. The magnetic field lines will also be altered around the hole due to the change in shape. The size and position of the hole will affect the magnetic performance differently.
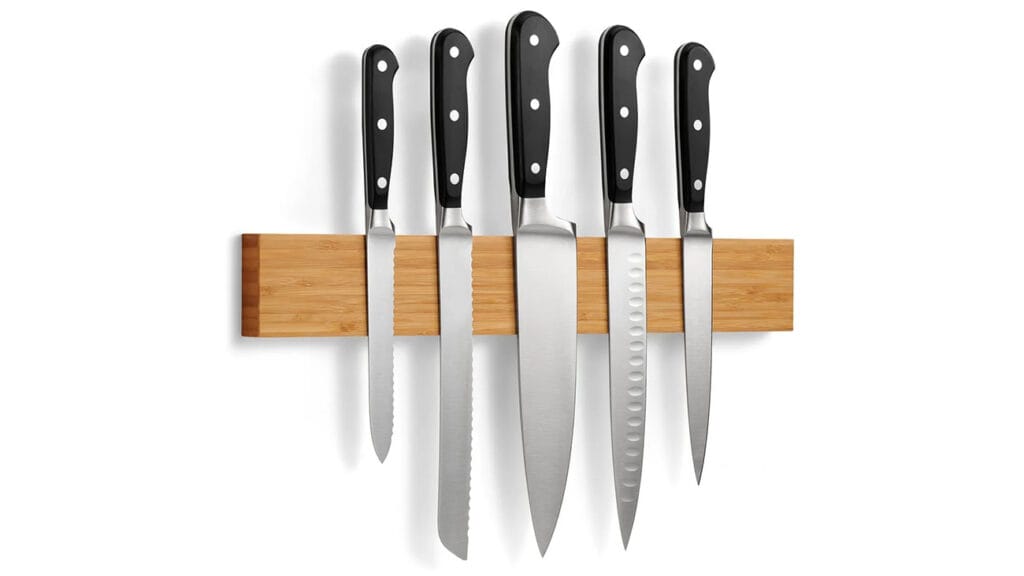