# Samarium Cobalt Hole Magnets: Unmatched Performance Where Heat is a Factor
**Summary:** This article delves into the world of Samarium Cobalt (SmCo) hole magnets, exploring their unique characteristics and unparalleled performance capabilities, particularly in high-temperature environments. Discover why SmCo hole magnets are the ideal solution for applications demanding robust magnetic force and exceptional resistance to demagnetization in challenging conditions, and learn how to choose the right one for your specific needs.
## Understanding Samarium Cobalt Magnet Technology
Samarium Cobalt magnets, discovered in the late 1960s, represent a significant advancement in permanent magnet technology. They are composed of an alloy of Samarium (Sm) and Cobalt (Co), often with additions of iron, copper, or other elements to fine-tune their magnetic properties. These magnets are characterized by exceptionally high coercivity, a measure of their resistance to demagnetization, and high Curie temperatures, the point at which a magnet loses its magnetism.
The manufacturing process for SmCo magnets involves powder metallurgy techniques. The raw materials are meticulously blended, finely ground into a powder, compacted under intense pressure (often pressing in a magnetic field to align the magnetic domains), and then sintered at high temperatures. Sintering fuses the powder particles together, creating a dense and robust magnetic material. Post-sintering processes may include machining to achieve desired shapes and dimensions and surface treatment for corrosion protection (though SmCo is inherently more corrosion-resistant than neodymium). The precise control over composition and processing allows engineers to tailor the magnetic properties to suit specific application requirements.
Different grades of SmCo magnets exist, categorized primarily by their energy product (a measure of magnetic strength). The two main families are SmCo5 (Samarium Cobalt 1:5) and Sm2Co17 (Samarium Cobalt 2:17). SmCo5 alloys generally offer higher coercivity and are suitable for applications with extreme demagnetizing fields. Sm2Co17 alloys provide higher energy product and are often preferred when a stronger magnetic field is required. Choosing the appropriate grade is crucial for optimal performance and longevity.
## The Advantages of Hole Magnets Design
Hole magnets, as the name suggests, are magnets with a central hole. This seemingly simple design modification unlocks several key advantages, making them supremely useful in specific applications. The presence of the hole allows for mechanical fastening with screws, bolts, or rivets, providing a secure and integrated mounting solution. This eliminates the need for adhesives, which can degrade over time, especially at elevated temperatures, leading to potential failures.
The hole also offers a conduit for running wires, tubes, or other components directly through the magnet. This is particularly beneficial in sensor applications, motor assemblies, and other designs where space is limited and efficient routing is essential. Integrating these elements directly within the magnetic assembly simplifies the overall design, reduces the number of components required, and improves reliability.
Furthermore, the hole can alter the magnetic field distribution around the magnet. By carefully designing the hole’s size and shape, engineers can fine-tune the magnetic field strength and direction to optimize performance for a given application. This aspect is crucial in areas with strong demagnetizing influences and requiring precise magnetic field control.
## High-Temperature Performance: SmCo’s Standout Feature
One of the most compelling arguments for using Samarium Cobalt magnets, particularly in hole magnet configurations, is their exceptional high-temperature performance. Unlike Neodymium Iron Boron (NdFeB) magnets, which suffer significant performance degradation at relatively moderate temperatures, SmCo magnets retain their magnetic properties at considerably higher temperatures, often exceeding 300°C (572°F) depending on grade and operating conditions.
This superior thermal stability stems from the strong interatomic bonding within the SmCo alloy structure and their high Curie temperatures. This makes SmCo hole magnets ideal for applications where exposure to elevated temperatures is unavoidable or even a core operating characteristic. Examples include high-performance motors and generators used in aerospace and automotive applications, sensors deployed in industrial processes, and holding applications in demanding environments.
The superior resistance to temperature-related demagnetization leads to more consistent and reliable performance over the lifetime of the application. While NdFeB magnets might offer a slightly higher initial energy product at room temperature, their rapid performance decline at higher temperatures can quickly negate that advantage, making SmCo the clear choice when operating temperature is a critical factor. Careful consideration of the operating temperature range is paramount when selecting the appropriate magnet material.
## Applications Where Samarium Cobalt Hole Magnets Excel
The unique properties of Samarium Cobalt hole magnets make them indispensable in a wide range of applications where high performance at high temperatures is critical. In aerospace, they are used in actuators, sensors, and high-performance motors designed to operate under extreme conditions. The inherent reliability and temperature stability ensure that these critical components function flawlessly even during demanding flight profiles.
In the automotive industry, SmCo hole magnets find applications in various sensors, including ABS sensors, crankshaft position sensors, and throttle position sensors. The magnets’ ability to withstand the high temperatures generated by the engine compartment while maintaining accurate sensor readings is crucial for optimal vehicle performance and safety. Furthermore, they are found in high-performance electric motors used in hybrid and electric vehicles, contributing to improved efficiency and power output.
Industrial automation benefits from SmCo hole magnets in applications such as magnetic couplings, sensors, and robotic systems. Their robust performance and resistance to harsh industrial environments, including elevated temperatures and corrosive substances, ensure long-term reliability and minimal downtime. Also, down-hole drilling tools rely on the magnet’s exceptional quality for operation in the Earth under extreme pressures and temperatures.
## Designing with SmCo Hole Magnets: Key Considerations
When designing with SmCo hole magnets, several key factors must be carefully considered to ensure optimal performance and longevity. The size and geometry of the magnet, including the hole diameter and position, should be optimized to achieve the desired magnetic field distribution and mechanical strength. Finite element analysis (FEA) software can be a valuable tool for simulating magnetic fields and predicting performance under various operating conditions.
The operating temperature range is another critical factor. While SmCo magnets excel at high temperatures, their performance characteristics still vary somewhat with temperature. Consulting the manufacturer’s data sheets for the specific magnet grade is essential to understand how magnetic properties change with temperature and to account for these variations in the design. Calculating the working point of the magnet is vital to ensure that it operates within its stable region.
The mechanical aspects of integrating the hole magnet into the assembly must also be addressed. The mounting method, whether using screws, bolts, or other fasteners, should be designed to distribute stress evenly and prevent damage to the magnet. Care should be taken to avoid applying excessive torque during tightening, which could potentially crack or fracture the magnet. Appropriate tolerances should be specified to ensure proper fit and alignment.
## Comparing Samarium Cobalt to Other Magnet Types
While Samarium Cobalt magnets offer exceptional high-temperature performance, it’s important to compare them to other magnet types to understand their relative strengths and weaknesses. Neodymium Iron Boron (NdFeB) magnets boast the highest energy product and are generally more cost-effective than SmCo magnets at room temperature. However, their significant performance degradation at elevated temperatures limits their use in many demanding applications.
Ferrite magnets are another cost-effective option, offering good corrosion resistance and moderate temperature stability. However, their energy product is significantly lower than that of both SmCo and NdFeB magnets, making them less suitable for applications requiring high magnetic force. Alnico magnets offer good temperature stability and corrosion resistance but have a lower energy product than SmCo magnets and are more susceptible to demagnetization by external fields.
Ultimately, the choice of magnet material depends on the specific application requirements. If high-temperature performance and resistance to demagnetization are paramount, Samarium Cobalt magnets are the clear winner. However, if cost and maximum magnetic strength at room temperature are the primary considerations, NdFeB magnets may be a more suitable option. It’s important to carefully evaluate all factors and select the magnet material that best meets the needs of the application.
## Machining and Handling Samarium Cobalt Magnets
Samarium Cobalt magnets are brittle materials and require careful handling and machining to avoid damage. While they can be machined using specialized techniques, it’s generally recommended to purchase them in the desired shape and size to minimize the need for machining. If machining is necessary, it should be performed by experienced professionals using appropriate equipment and techniques.
Abrasive machining methods, such as grinding and lapping, are commonly used for shaping and finishing SmCo magnets. Coolants should be used to prevent overheating and thermal shock, which could cause cracking. Electrical discharge machining (EDM) can also be used for creating complex shapes. Care should be taken to avoid contamination during machining, as foreign materials can affect the magnetic properties of the magnet.
When handling SmCo magnets, it’s important to wear appropriate personal protective equipment, including gloves and eye protection. The magnets can exert strong attractive forces, and care should be taken to avoid pinching fingers or allowing them to snap together forcefully. SmCo magnets are also susceptible to chipping or breaking if dropped or subjected to impact. Storing them properly in a protective container can prevent accidental damage.
## The Future of Samarium Cobalt Magnet Technology
Ongoing research and development efforts continue to improve the performance and reduce the cost of Samarium Cobalt magnets. Improvements in materials processing techniques, such as grain refinement and compositional optimization, are leading to higher energy products and improved temperature stability. Efforts are also underway to reduce the Cobalt content of SmCo magnets, as Cobalt is a relatively expensive and strategically important material.
Nanotechnology is also playing an increasingly important role in the development of new magnetic materials. Nanocrystalline SmCo magnets, with grain sizes on the nanometer scale, exhibit enhanced magnetic properties compared to conventional microcrystalline magnets. These materials offer the potential for even higher energy products and improved high-temperature performance. 3D printing technologies also hold promise for creating complex and customized magnet shapes with unprecedented precision.
The growing demand for high-performance magnets in applications such as electric vehicles, renewable energy systems, and industrial automation is driving innovation in SmCo magnet technology. As technology advances, we can expect to see even more powerful and cost-effective SmCo magnets that will enable new and exciting applications.
## Conclusion
Samarium Cobalt hole magnets represent a pinnacle in magnetic technology, offering unmatched performance in harsh, high-temperature environments. Their inherent resistance to demagnetization, combined with the design flexibility afforded by the hole configuration, makes them ideal for a broad spectrum of applications. From aerospace and automotive to industrial automation and beyond, SmCo hole magnets provide the reliability and performance demanded by critical systems. While considerations like cost and machining complexities exist, the benefits of SmCo magnets are undeniable when high-temperature operation and long-term stability are paramount. As research and development continue to push the boundaries of magnetic materials, expect to see even more advanced SmCo magnets powering the technologies of tomorrow.
## FAQ
### What is the Curie temperature of a Samarium Cobalt magnet?
Generally, SmCo magnets have Curie temperatures ranging from 700°C to 800°C (1292°F to 1472°F), significantly higher than NdFeB magnets. The specific Curie temperature depends on the alloy composition and manufacturing process.
### Are Samarium Cobalt magnets brittle?
Yes, SmCo magnets are inherently brittle materials and can be susceptible to chipping or cracking if mishandled or subjected to impact.
### How does the hole affect the magnetic field of a SmCo hole magnet?
The presence of the hole alters the magnetic field distribution around the magnet. By carefully designing the hole’s size and shape, engineers can fine-tune the magnetic field strength and direction to optimize performance for a given application.
### Are SmCo magnets corrosion resistant?
Samarium Cobalt magnets exhibit good corrosion resistance, particularly compared to Neodymium magnets. They generally do not require protective coatings in most environments, though specific applications with harsh chemicals might necessitate a coating.
### Can SmCo hole magnets be remagnetized?
Yes, SmCo hole magnets can be remagnetized using a strong magnetic field. It’s important to use the appropriate magnetization equipment and procedure to avoid demagnetizing or damaging the magnet.
### What are the main differences between SmCo5 and Sm2Co17 grades?
SmCo5 alloys generally offer higher coercivity and are suitable for applications with extreme demagnetizing fields. Sm2Co17 alloys provide higher energy product and are often preferred when a stronger magnetic field is required.
### Are there any safety precautions when working with strong magnets, like SmCo magnets?
Yes, you should wear safety glasses to protect your eyes when handling. Keep magnets away from items sensitive to magnetism; jewelry, keys, ID cards, computer hard drives. The high attraction force of magnets can be a safety threat if you allow fingers or skin to be pinched between two magnets or a magnet and a steel object. Use caution when working with high field magnets.
### What is the typical lifespan of a Samarium Cobalt magnet?
If used within specifications, magnets do not have moving parts that will break down over time. The degradation that they experience slows greatly as time increases. Magnets can lose a percent or two of their power after initial use. A magnet will be considered near the end of its useful life when it has lost 20% of its original magnetic field strength. With proper handling, a SmCo magnet can last several decades.
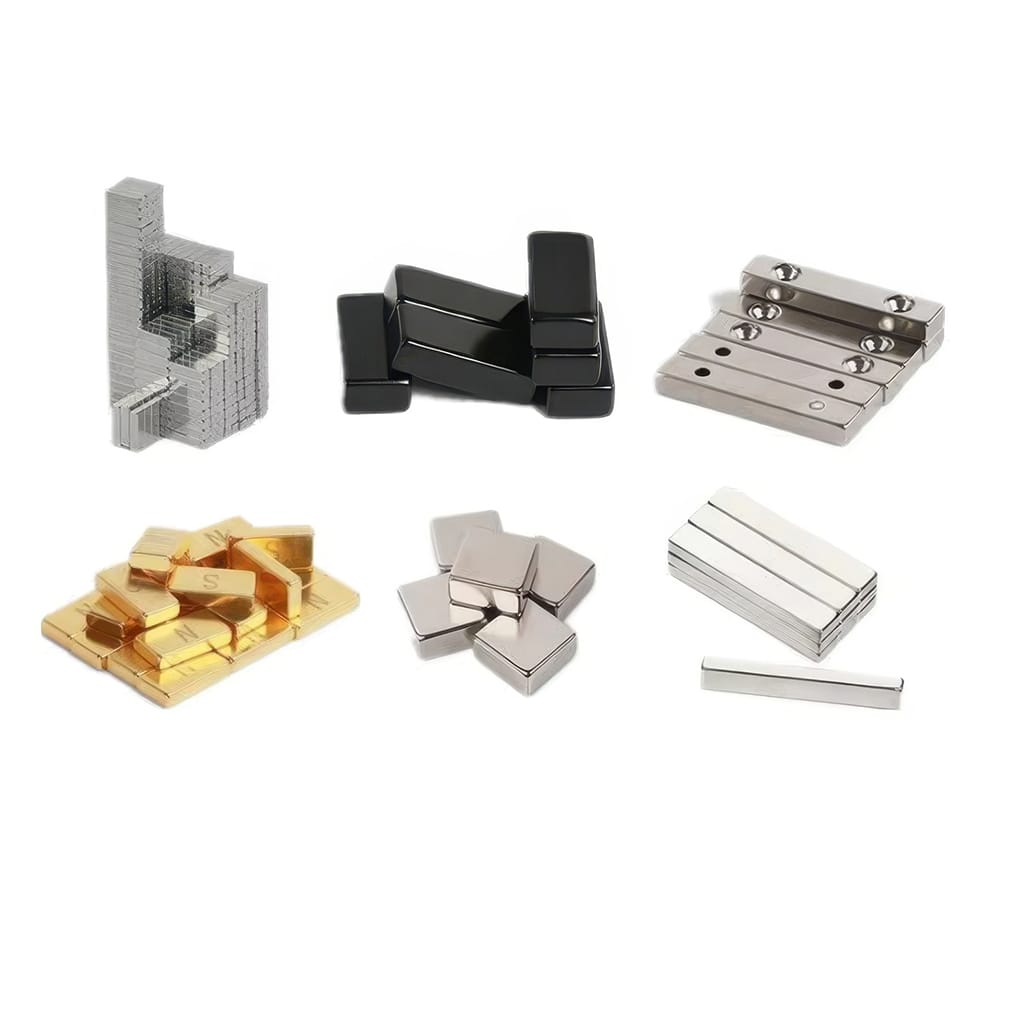