# The Frustrations of Screws, Bolts, and Rivets: Magnetic Fasteners as the Superior Solution
This article delves into the common issues plaguing traditional fasteners like screws, bolts, and rivets – from installation challenges and wear and tear to aesthetic concerns and limitations in certain applications. It then explores how magnetic fasteners offer a compelling alternative, providing greater convenience, improved durability, and enhanced design flexibility, ultimately highlighting why magnetic fastening solutions are gaining prominence across various industries.
## The Inherent Limitations of Traditional Fasteners
Traditional fasteners, while ubiquitous, are far from perfect. Their functionality often comes at the cost of convenience, durability, and even aesthetic appeal. Understanding these inherent limitations is crucial to appreciating the advantages offered by magnetic fastening solutions.
Firstly, the act of applying traditional fasteners necessitates tools, skill, and time. Whether it’s meticulously aligning screws in pre-drilled holes or clamping rivets with specialized machinery, the process can be cumbersome and prone to error. Misaligned screws can strip threads, while poorly applied rivets can create weak points in a structure. This not only increases the overall project timeline but also adds to the cost due to potential rework and material wastage.
Secondly, these fasteners inherently create permanent or semi-permanent bonds. While this is desirable in some situations, it hinders disassembly and reassembly. Accessing internal components for repair or modification becomes a destructive process often involving damaging the fastener or the surrounding material. This lack of flexibility can be a major drawback in applications where adaptability and ease of access are paramount.
## Installation Headaches: Time, Tools, and Expertise Required
The installation of traditional fasteners is rarely as simple as twisting a screw or hammering a nail. It frequently involves pre-drilling holes, ensuring proper alignment, and using specialized tools like screwdrivers, wrenches, or riveting guns. This complexity not only increases the time required for installation but also necessitates a certain level of expertise.
Consider a scenario where you’re assembling flat-pack furniture. The instructions often involve multiple types of screws, each requiring a specific screwdriver. Missing a step or using the wrong screw can lead to instability, damage to the furniture, or even injury. This highlights the inherent user-unfriendliness of traditional fastening methods, especially for individuals with limited DIY experience. Further, scaling this up to industrial applications introduces issues of precise torque settings and trained labor, further compounding installation difficulties.
## Wear and Tear: Corrosion, Loosening, and Fatigue
Traditional fasteners are constantly exposed to environmental factors that contribute to wear and tear. Corrosion, caused by exposure to moisture and other corrosive agents, can weaken the fastener and eventually lead to failure. Loosening, due to vibration or changes in temperature, can also compromise the integrity of the connection. Fatigue, caused by repeated stress cycles, can eventually lead to cracks and fractures in the fastener.
Think of outdoor structures like bridges or fences. These structures are constantly subjected to the elements, leading to rust and corrosion. Regular maintenance is required to inspect and replace corroded fasteners, which can be costly and time-consuming. Similarly, vibrating machinery often experiences loosening of bolts and screws, requiring periodic tightening to prevent malfunctions or accidents. The sheer number of potential failure points in a system relying on traditional fasteners makes it a significant long-term maintenance concern.
## Aesthetic Compromises: Visible Fasteners and Unsightly Holes
One often-overlooked aspect of fastening is the aesthetic impact. Traditional fasteners, by their very nature, are visible and can detract from the overall appearance of a product or structure. Exposed screw heads or rivet protrusions can be unsightly, especially in applications where visual appeal is paramount.
Consider the design of modern electronics. Manufacturers strive for sleek, minimalist designs, and visible fasteners can disrupt this aesthetic. Hiding screws requires complex assembly techniques or the use of adhesive bonding, which has its own set of limitations. Similarly, in furniture design, exposed fasteners can detract from the overall elegance and craftsmanship. The need to balance functionality with aesthetics often leads to compromises when using traditional fastening methods.
## Limited Versatility: Material Compatibility and Application Constraints
Traditional fasteners are not universally compatible with all materials. Certain materials, like thin plastics or composite materials, can be easily damaged by screws or bolts. Additionally, some applications require fasteners that can withstand extreme temperatures, pressures, or corrosive environments, further limiting the options available.
For example, attaching components to lightweight or brittle materials requires careful consideration to avoid cracking or deformation. Using excessive force can easily damage the material, rendering the fastener ineffective. Similarly, in aerospace applications, fasteners must be able to withstand extreme temperature fluctuations and high levels of stress. The inherent limitations of traditional fasteners in these scenarios necessitate the exploration of alternative fastening solutions.
## Disassembly Challenges: Damage, Difficulty, and Time Consumption
Disassembling components that are held together by traditional fasteners can be a challenging and time-consuming process. Screws can be stripped, bolts can be rusted, and rivets can be difficult to remove without damaging the surrounding material. This lack of ease during disassembly can significantly increase the cost and complexity of repairs and modifications.
Imagine trying to repair a broken appliance. Often, the first step is to disassemble the unit, which can involve struggling with corroded screws or difficult-to-reach fasteners. This can be frustrating and time-consuming, especially if you lack the proper tools or experience. Furthermore, accidentally stripping a screw head can further complicate the process. This highlights the significant disadvantage of traditional fasteners in applications where easy disassembly is critical.
## Magnetic Fasteners: A Superior Alternative Emerges
Magnetic fasteners present a compelling alternative to traditional fastening methods, offering numerous advantages in terms of convenience, durability, and aesthetics. Their non-mechanical nature eliminates many of the common problems associated with screws, bolts, and rivets, making them a suitable solution for a wide range of applications.
At their core, magnetic fasteners utilize powerful magnets to create a strong and reliable connection. This eliminates the need for drilling holes, tightening screws, or applying rivets. Installation is typically as simple as placing the two components together, allowing the magnets to attract and secure them. This significantly reduces installation time and eliminates the risk of damage to the materials being joined.
## The Benefits of Magnetic Fasteners: Simplicity, Speed, and Strength
Magnetic fasteners offer a multitude of benefits over traditional fasteners, including ease of installation, improved aesthetics, enhanced durability, and greater design flexibility. These advantages make them an increasingly attractive option for a wide range of applications, from consumer electronics to aerospace engineering.
One of the most significant benefits is the simplicity and speed of installation. With magnetic fasteners, there is no need for pre-drilling holes or tightening screws. Simply bring the two components together, and the magnets will automatically align and secure them. This not only saves time but also reduces the risk of errors and damage. Another notable advantage is the improved aesthetics. Since magnetic fasteners do not require visible screws or bolts, they allow for a cleaner and more seamless design. This is particularly important in applications where visual appeal is a priority, such as furniture and consumer electronics.
## Rethinking Design with Magnetism: Flexibility and Functionality
Magnetic fasteners offer designers a new level of flexibility and functionality. They allow for the creation of products that are easier to assemble, disassemble, and modify. This can lead to significant cost savings and improved product performance.
Consider the design of modular furniture. Magnetic fasteners allow for the easy reconfiguration of components, enabling users to customize their furniture to suit their individual needs. Similarly, in the automotive industry, magnetic fasteners can be used to attach trim panels and other components, making them easier to remove for maintenance or repair. The increased flexibility offered by magnetic fasteners opens up new possibilities for innovative product design. Moreover, magnetic fasteners can facilitate concealed and reversible attachment, which is difficult to achieve with traditional methods.
## Durability and Longevity: Resistant to Vibration and Corrosion
Magnetic fasteners are inherently more durable and resistant to wear and tear than traditional fasteners. They are not susceptible to corrosion, loosening, or fatigue, making them a reliable option for demanding applications.
Unlike screws and bolts, magnetic fasteners do not require threading, which eliminates a potential point of failure. They are also not affected by vibration, which can cause traditional fasteners to loosen over time. Furthermore, the magnetic force provides a consistent and reliable holding power, even in extreme temperatures or corrosive environments. This makes magnetic fasteners a long-lasting and maintenance-free solution for a variety of applications.
## Applications Across Industries: From Electronics to Aerospace
Magnetic fasteners are finding increasing applications across a wide range of industries, including electronics, automotive, aerospace, and construction. Their versatility and ease of use make them a suitable solution for various fastening challenges.
In the electronics industry, magnetic fasteners are used to attach components to circuit boards, secure enclosures, and create snap-fit connections. In the automotive industry, they are used to attach trim panels, secure sensors, and provide temporary fastening during assembly. In the aerospace industry, they are used to attach lightweight panels, secure access panels, and provide temporary fastening during maintenance. The growing adoption of magnetic fasteners across diverse industries highlights their versatility and potential.
## Choosing the Right Magnetic Fastener: Factors to Consider
Selecting the appropriate magnetic fastener requires careful consideration of several factors, including the required holding force, the materials being joined, the environmental conditions, and the desired aesthetic. Proper planning ensures optimal performance and longevity.
The holding force of the magnet must be sufficient to withstand the expected loads and stresses. The materials being joined must be compatible with magnetism. The environmental conditions, such as temperature and humidity, can affect the performance of the magnet. The desired aesthetic should also be considered when selecting the type and size of the magnetic fastener. Consulting with a magnetic fastener supplier can help ensure you select the right solution for your specific needs. Additionally, consider the long-term performance; some magnets degrade over time.
## Conclusion: Embracing the Future of Fastening
Traditional fasteners have served their purpose for centuries, but their limitations are becoming increasingly apparent in the modern world. Magnetic fasteners offer a superior alternative, providing greater convenience, improved durability, and enhanced design flexibility. As technology advances and manufacturing processes evolve, the adoption of magnetic fastening solutions is poised to accelerate, revolutionizing the way we connect and assemble products across various industries. The future of fastening is magnetic.
## FAQ
### How strong are magnetic fasteners?
Magnetic fasteners can be incredibly strong, depending on the type of magnet used (e.g., neodymium, ferrite, samarium cobalt), its size, and the design of the fastener. Neodymium magnets, in particular, offer very high holding power for their size. The strength of magnetic fasteners is measured in pull force, which indicates how much force is required to separate the components held together by the magnets.
### Can magnetic fasteners be used in high-temperature environments?
Yes, but the type of magnet is crucial. Ferrite magnets generally have good temperature resistance, while neodymium magnets can lose strength at higher temperatures. Samarium cobalt magnets offer even better temperature performance than ferrite. It’s essential to check the temperature rating of the specific magnet before using it in a high-temperature environment, as exceeding this rating can permanently demagnetize the magnet.
### Will magnetic fasteners affect electronic devices?
Potentially. Strong magnetic fields can interfere with the operation of certain electronic devices, such as hard drives, magnetic stripe cards, and some types of sensors. The proximity of the magnet and the type of device will determine the extent of the interference. It is generally recommended to keep strong magnets away from sensitive electronic equipment. Shielded magnetic fasteners can minimize the magnetic field leakage and reduce the risk of interference.
### Are magnetic fasteners more expensive than traditional fasteners?
The cost of magnetic fasteners can vary depending on the type of magnet, the size of the fastener, and the quantity purchased. In some cases, they may be more expensive than traditional fasteners. However, the reduced installation time, improved durability, and enhanced aesthetics can often offset the higher initial cost. Furthermore, the elimination of tools and skilled labor can lead to significant cost savings in the long run.
### Can magnetic fasteners be used with non-magnetic materials?
Yes, magnetic fasteners can be used with non-magnetic materials by incorporating a ferrous material (e.g., steel) on one or both sides of the connection. The magnet will attract the ferrous material, providing a secure hold. This is a common technique used to attach magnetic fasteners to materials like aluminum, plastic, or wood.
### How do you remove magnetic fasteners?
Removing magnetic fasteners is typically very simple. Depending on the design, you may be able to simply pull the components apart or slide them apart. In some cases, a specialized tool may be needed to overcome the magnetic force. The ease of removal is one of the key advantages of magnetic fasteners over traditional fasteners.
### Are magnetic fasteners environmentally friendly?
The environmental impact of magnetic fasteners depends on the materials used and the manufacturing processes. Magnets are typically made from rare earth elements, which require mining and processing. However, the long life and reusability of magnetic fasteners can reduce the overall environmental impact compared to traditional fasteners that are frequently discarded. Recycling magnets is also becoming more common, which can further reduce their environmental footprint.
### Where can I buy magnetic fasteners?
Magnetic fasteners are available from a variety of sources, including industrial suppliers, hardware stores, and online retailers. Researching different vendors and comparing prices and product specifications is essential to purchase high-quality magnetic fasteners to meet your needs. Consulting with a magnetic fastener specialist can also offer valuable guidance during the selection and procurement process.
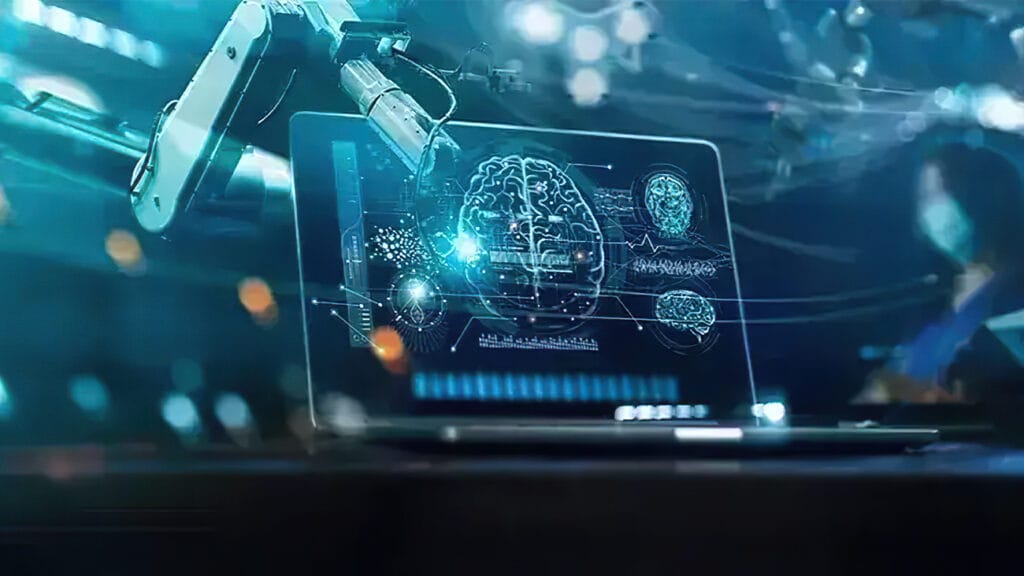