# The Surprising Strength and Versatility: Why Magnetic Fasteners Are Exploding in Popularity
**Summary:** Tired of screws that strip, snaps that break, and adhesives that fail? This article dives deep into the world of magnetic fasteners, revealing their numerous advantages over traditional fastening methods. Discover why magnetic fasteners are rapidly gaining popularity across a wide range of industries and applications, from crafting and woodworking to automotive and aerospace, and learn how they can improve your projects with increased efficiency, durability, and aesthetics. We’ll explore the different types, strengths, and applications, providing you with the knowledge to choose the right magnetic fastener for your specific needs.
## Understanding the Power of Attraction: What Are Magnetic Fasteners?
Magnetic fasteners, at their core, leverage the fundamental force of magnetism to join two or more objects together. Unlike traditional fasteners that rely on physical interlocking mechanisms (like threads on screws or the physical grip of rivets), magnetic fasteners utilize the attractive forces between magnets or between a magnet and a ferromagnetic material (like iron, steel, or nickel). They come in a vast array of shapes, sizes, and configurations, each designed for specific applications. The selection of the right magnet is crucial, with options ranging from inexpensive ferrite magnets to powerful neodymium magnets, each offering varying strengths and temperature resistances.
The primary advantage that defines all magnetic fasteners is their non-destructive nature and reusability. Traditional fasteners often require drilling holes or applying adhesives, permanently altering the materials they join. Magnetic fasteners, however, offer a clean, reversible, and often stronger solution. This makes them ideal for applications where frequent assembly and disassembly are required, or where preserving the aesthetic integrity of the materials is paramount. This reusability also contributes to long-term cost savings and reduced waste.
## Speed and Efficiency: The Time-Saving Benefits of Magnetic Connections
One of the most compelling reasons for the increasing popularity of magnetic fasteners is the significant time savings they offer during assembly and disassembly. Unlike screwing, snapping, or gluing, which require precise alignment and often multiple steps, magnetic fasteners can be connected almost instantly. This speed is particularly beneficial in high-volume manufacturing environments or in applications where accessibility is limited.
Consider the assembly of electronic devices, furniture, or modular displays. With traditional fasteners, each screw or bolt adds precious seconds (or even minutes) to the overall process. Magnetic fasteners, on the other hand, can dramatically reduce this assembly time, leading to increased production rates and reduced labor costs. The ease of use also extends to consumers, making products easier to assemble and customize at home. Moreover, the simplified assembly process often requires less specialized tooling, further reducing overhead expenses.
## Durability and Longevity: Magnetic Fasteners Built to Last
Magnetic fasteners offer exceptional durability and longevity in many applications. The absence of physical stress points, like those found in threaded connections, means they are less susceptible to wear and tear, vibration-induced loosening, and fatigue failure. This is particularly crucial in applications where the assembled structure is subjected to repetitive motion or harsh environmental conditions.
Additionally, because magnetic fasteners don’t require drilling or punching holes, they preserve the structural integrity of the joined materials. This is especially important in lightweight materials like composite panels or thin-walled metal structures, where traditional fasteners can create weak points or stress concentrations. Furthermore, the resistance to corrosion is generally excellent, especially when the magnets are coated with protective materials. This ensures long-term reliability even in humid or corrosive environments, significantly extending the lifespan of the assembled product.
## Aesthetics and Design: Unobtrusive and Visually Appealing
Magnetic fasteners offer a clean, seamless aesthetic that is often impossible to achieve with traditional fasteners. By eliminating the need for visible screws, bolts, or snaps, they create a more refined and modern appearance. This is particularly important in applications where visual appeal is a key consideration, such as furniture design, retail displays, and architectural elements.
The unobtrusive nature of magnetic fasteners allows designers to focus on the overall form and function of the product, without being constrained by the need to conceal or integrate visible fasteners. This freedom can lead to more innovative and aesthetically pleasing designs. Furthermore, magnetic fasteners can be easily concealed beneath surfaces, creating a “floating” or “invisible” connection, which is highly desirable in many applications. The clean lines and minimalist aesthetic contribute significantly to the perceived quality and value of the product.
## Versatility Across Industries: From Craft Projects to Aerospace Engineering
The versatility of magnetic fasteners is truly remarkable. They find applications in virtually every industry, from small-scale craft projects to complex aerospace engineering. This adaptability stems from the wide range of sizes, strengths, and configurations available, allowing engineers and designers to tailor the fastening solution to meet the specific requirements of each application.
In the crafting world, magnetic clasps and closures are used extensively in jewelry making, bag making, and other creative projects. In the woodworking industry, magnetic catches are used to secure cabinet doors and drawers, providing a clean and reliable alternative to traditional latches. In the automotive industry, magnetic fasteners are used in a variety of applications, including attaching trim panels, securing sensors, and even holding body panels in place during assembly. And in aerospace and defense, high-strength magnetic fasteners are used in critical applications where reliability and performance are paramount. This widespread adoption underscores the inherent adaptability and problem-solving capabilities of magnetic fastening technology.
## Specialized Applications: Beyond the Basics of Magnetic Fastening
Beyond general fastening purposes, magnetic fasteners have found niche applications where their unique properties provide significant advantages. For example, magnetic couplings are used in pumps and mixers to create a hermetically sealed connection between the motor and the impeller, preventing leaks and contamination. This is crucial in industries like pharmaceuticals, food processing, and chemical manufacturing.
Another specialized application is magnetic shielding, where magnetic materials are used to protect sensitive electronic components from electromagnetic interference. This is essential in medical devices, aerospace equipment, and other applications where reliable performance is critical. Magnetic holding systems are also used in robotic arms and automated machinery to grip and manipulate parts with speed and precision. These specialized applications highlight the versatility and potential of magnetic fasteners to solve complex engineering challenges. Magnetic sweepers used to remove metal debris are another good example.
## Choosing the Right Magnetic Fastener: Factors to Consider
Selecting the right magnetic fastener for a specific application requires careful consideration of several key factors. First and foremost is the required holding force. This depends on the weight of the objects being joined, the expected loads, and the safety factor required. Neodymium magnets offer the strongest holding force, while ferrite magnets are typically used in less demanding applications.
Another important factor is the operating temperature. Some magnets, particularly neodymium magnets, can lose their magnetism at elevated temperatures. Therefore, it is crucial to select a magnet material that is compatible with the expected temperature range. The environment in which the fastener will be used is also important. Corrosion resistance is crucial in humid or corrosive environments. Finally, consider the size and shape of the magnets and the materials they will be attached to. It’s always better to test the configuration before committing to a bulk order.
## Future Trends: Innovations and Advancements in Magnetic Fastening Technology
The field of magnetic fastening is constantly evolving, with ongoing research and development focused on improving performance, expanding applications, and reducing costs. One promising trend is the development of new magnetic materials with higher energy products and improved temperature stability. These advancements will enable the creation of even stronger and more reliable magnetic fasteners.
Another trend is the integration of magnetic fasteners with smart technologies. For example, sensors can be incorporated into magnetic fasteners to monitor the connection strength and detect any signs of loosening or failure. This information can be used to trigger alerts or initiate maintenance procedures, improving safety and preventing costly downtime. 3D printing technology is also playing a role, enabling the creation of custom-designed magnetic fasteners with complex geometries and tailored magnetic properties. These innovations promise to further expand the capabilities and applications of magnetic fastening technology in the years to come.
## Conclusion
Magnetic fasteners present a compelling alternative to traditional fastening methods, offering advantages in speed, durability, aesthetics, and versatility. Their increasing popularity across various industries is a testament to their effectiveness and adaptability. From simplifying everyday tasks to solving complex engineering challenges, magnetic fasteners are proving to be a valuable tool for designers, engineers, and hobbyists alike. With ongoing advancements in magnetic materials and manufacturing techniques, the future of magnetic fastening looks bright, promising even greater innovation and application potential. Their ease of use, combined with their robustness, makes them an increasingly attractive option for a wide array of projects and applications.
## FAQ
### What are the main types of magnetic fasteners?
Magnetic fasteners can be broadly categorized by the type of magnet used (ferrite, neodymium, alnico, samarium cobalt) and their configuration (buttons, catches, latches, strips, etc.). The strongest are typically neodymium magnets, while ferrite magnets are more economical.
### How strong are magnetic fasteners?
The strength of a magnetic fastener depends on several factors, including the type of magnet, its size, its shape, the material it is attracting to, and the air gap between the magnet and the ferromagnetic material. Neodymium magnets can provide extremely high holding forces, while ferrite magnets are suitable for lighter-duty applications.
### Can magnetic fasteners damage electronic devices?
Strong magnetic fields can potentially interfere with or damage sensitive electronic devices, such as hard drives and magnetic storage media. It is important to keep strong magnetic fasteners away from these devices and to follow the manufacturer’s recommendations.
### Are magnetic fasteners resistant to corrosion?
The corrosion resistance of magnetic fasteners depends on the magnet material and any protective coatings that have been applied. Neodymium magnets are particularly susceptible to corrosion and typically require a protective coating, such as nickel, zinc, or epoxy. Ferrite magnets offer inherent corrosion resistance.
### How do I choose the right size and strength of magnetic fastener for my application?
To choose the right size and strength, consider the weight of the objects being joined, the expected loads, the environment in which the fastener will be used, and the desired safety factor. It is always a good idea to test the fastener in your specific application before committing to a bulk purchase. Consider using a pull testing device to measure detachment strength.
### Are magnetic fasteners more expensive than traditional fasteners?
The cost of magnetic fasteners varies depending on the type of magnet, its size, and the quantity purchased. In some cases, they can be more expensive than traditional fasteners, but the long-term benefits, such as increased durability, reduced assembly time, and improved aesthetics, can often justify the higher initial cost.
### Can magnetic fasteners be used in high-temperature environments?
Some magnets, particularly neodymium magnets, can lose their magnetism at elevated temperatures. It is important to select a magnet material that is compatible with the expected temperature range. Alnico and samarium cobalt magnets offer better temperature stability than neodymium magnets.
### Where can I buy magnetic fasteners?
Magnetic fasteners are available from a variety of sources, including online retailers, hardware stores, industrial supply companies, and specialized magnet suppliers. Be sure to research different vendors to find the best prices and selection.
### Can magnetic fasteners be used with non-ferrous materials like aluminum and plastic?
Magnetic fasteners require a ferromagnetic material (like iron, steel, or nickel) to attract to. To use them with non-ferrous materials like aluminum and plastic, you’ll need to incorporate a steel plate or other ferromagnetic component into the assembly. Alternatively, you can use magnetic adhesives designed to bond magnets to non-ferrous surfaces.
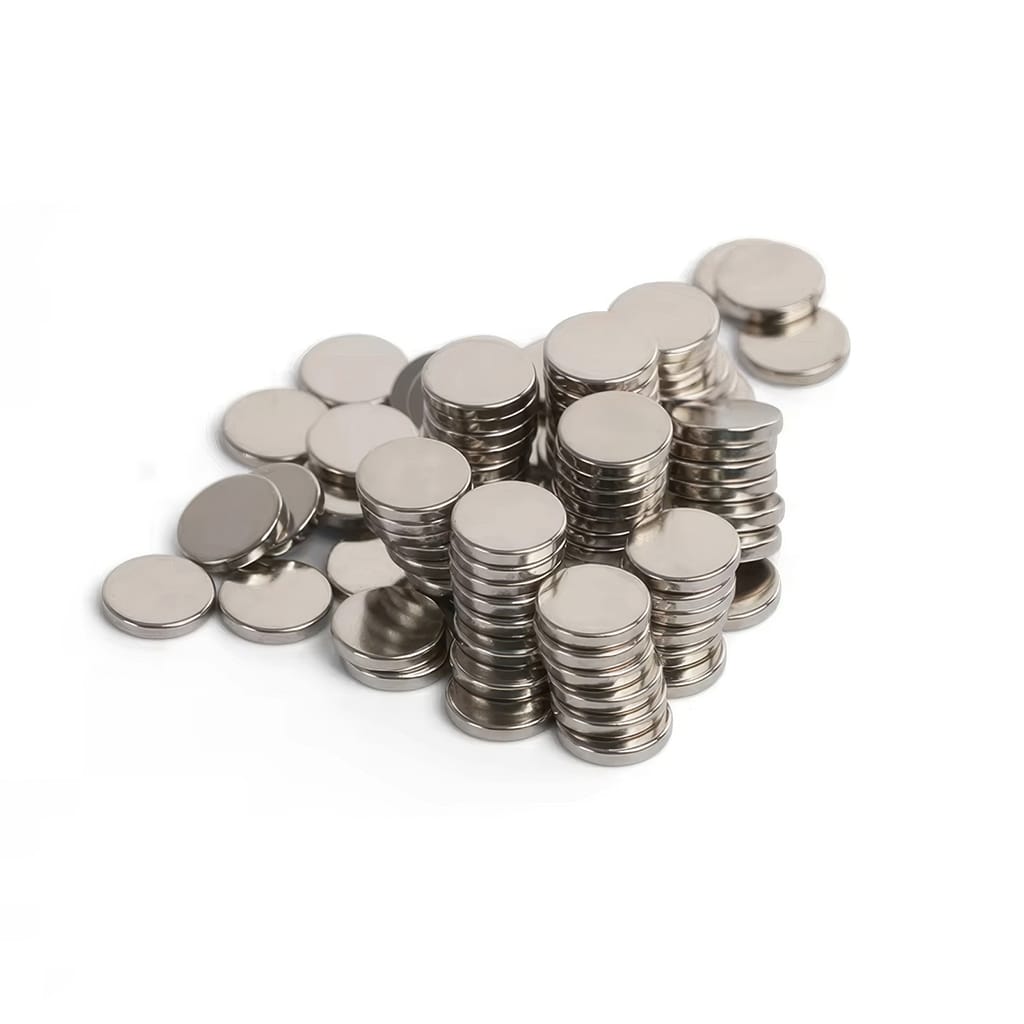