# Strong Hold, No Tools: Unleashing the Power of Magnetic Fasteners
This article explores the fascinating world of magnetic fasteners, highlighting their strength, ease of use, and versatility across various applications. Discover how these ingenious devices offer a secure and tool-free alternative to traditional fastening methods, saving you time, effort, and potentially, damage to your materials.
## The Allure of Magnetic Fastening: Simplicity and Strength Combined
Magnetic fasteners offer a compelling alternative to screws, nails, bolts, and adhesives. Their primary advantage lies in their simplicity – requiring no tools for installation or removal. They rely on the inherent attractive force of magnets to create a strong and reliable bond between two surfaces. This inherent simplicity translates to faster assembly, easier adjustments, and a cleaner, more reversible solution compared to traditional mechanical fasteners. The combination of ease of use and surprising holding power makes magnetic fastening an increasingly attractive option for both DIY projects and industrial applications. Imagine assembling furniture without needing a screwdriver, or creating modular displays that can be reconfigured in seconds. Magnetic fasteners make such scenarios a reality.
Beyond user-friendliness, magnetic fasteners often offer a cleaner aesthetic. They eliminate the visible heads of screws or the need for potentially messy adhesives. This creates a more seamless and professional look, which is particularly appealing in display cases, cabinets, and other applications where appearance is paramount. The ability to conceal the fastening mechanism adds a touch of elegance and sophistication that traditional methods often lack.
Finally, magnetic fastening can be less damaging to materials than methods like drilling or nailing. In applications involving fragile materials or surfaces that require a pristine finish, magnets provide a non-invasive solution that minimizes the risk of scratches, dents, or other blemishes.
## Understanding the Different Types of Magnetic Fasteners
The world of magnetic fasteners is diverse, offering a range of options designed for specific needs. The choice of which type to use depends heavily on factors like the materials being joined, the required holding force, and the environmental conditions. Broadly, magnetic fasteners can be categorized based on the type of magnet used and the fastening mechanism employed.
Permanent magnets, such as neodymium (NdFeB), ferrite, samarium cobalt (SmCo), and alnico, are the most common choice for fasteners. Neodymium magnets are known for their exceptional strength-to-size ratio, making them ideal for applications where a strong hold is needed in a small space. Ferrite magnets are more cost-effective and resistant to corrosion, but generally offer lower magnetic strength. Samarium cobalt magnets are known for their high-temperature resistance, making them suitable for applications where the fastener will be exposed to heat. Alnico magnets offer good temperature stability and corrosion resistance, but are generally less powerful than neodymium magnets.
Beyond the type of magnet, fasteners can also vary in their design and construction. Some common forms include magnetic catches, magnetic latches, magnetic hooks, and magnetic strips. Magnetic catches are often used in cabinet doors and drawers, providing a simple and reliable way to keep them closed. Magnetic latches offer a stronger holding force and are typically used in heavier doors or panels. Magnetic hooks are versatile for hanging lightweight items, while magnetic strips are ideal for organizing tools or creating temporary displays. Each design is optimized for particular applications, ensuring the best possible performance and security.
## Calculating Holding Strength: Ensuring a Reliable Bond
Determining the correct holding strength of a magnetic fastener is crucial for ensuring the safety and reliability of any application. Overestimating the required strength can lead to unnecessary costs, while underestimating it can result in failures and potential hazards. Fortunately, calculating holding strength, while requiring some understanding of magnet physics, can be approached systematically.
Several factors influence the holding strength of a magnetic fastener. These include the type and grade of the magnet, its size and shape, the material it is attaching to (specifically its ferromagnetic properties), the thickness and surface finish of the materials, and the presence of any air gaps between the magnet and the ferromagnetic material. Generally, neodymium magnets offer the highest holding force for their size, making them a popular choice when space is limited.
Manufacturers typically provide the pull force rating for their magnets, which represents the force required to separate the magnet from a flat, steel plate under ideal conditions. However, this rating is often a best-case scenario and may not accurately reflect the holding strength in a real-world application. It is crucial to consider the factors mentioned above and apply appropriate safety factors to ensure the chosen fastener provides adequate holding strength. Using multiple smaller magnets instead of a single large magnet can sometimes distribute the load more effectively. Consulting with a magnet specialist can provide valuable guidance in selecting the right magnetic fastener and calculating its holding strength for specific applications.
## Material Considerations: Choosing the Right Surface for Magnetic Adhesion
The success of magnetic fastening hinges on the properties of the materials involved, particularly the material to which the magnet is attracting. Not all materials are created equal in terms of their response to a magnetic field. Understanding these material differences is essential for selecting the appropriate magnetic fastening solution.
Ferromagnetic materials, such as iron, steel, nickel, and cobalt, are strongly attracted to magnets. These materials possess a unique atomic structure that allows them to readily align with a magnetic field, resulting in a strong attractive force. The strength of this attraction depends on the specific type of ferromagnetic material and its purity. For example, high-carbon steel will typically exhibit a stronger attraction than stainless steel. The surface finish of the ferromagnetic material also plays a role, with smoother surfaces generally providing better contact and a stronger hold than rough or corroded surfaces.
Non-ferromagnetic materials, such as aluminum, copper, brass, wood, plastic, and glass, are not attracted to magnets. While these materials cannot be directly fastened using magnets, there are still ways to incorporate magnetic fastening into applications involving them. This often involves embedding a ferromagnetic material, such as a steel plate or washer, into or behind the non-ferromagnetic material. The magnet then attracts to the embedded steel, providing a secure and concealed fastening point. Proper planning and execution are crucial for ensuring the steel plate is adequately secured and can withstand the applied forces.
## Applications Across Industries: Versatility in Action
Magnetic fastening’s versatility has led to its adoption across a diverse range of industries and applications. From everyday household uses to specialized industrial equipment, magnetic fasteners provide innovative solutions for a variety of challenges. Their ability to provide a strong, tool-free, and often reversible connection makes them an attractive alternative to traditional fastening methods.
In the woodworking industry, magnetic fasteners are used to create jigs, hold workpieces in place during assembly, and secure cabinet doors and drawers. The user-friendly nature of magnetic fasteners allows for quick adjustments and modifications, making them ideal for dynamic woodworking projects. In retail and display, magnetic fasteners are used to create modular displays, attach signage, and secure merchandise. Their ability to be easily reconfigured allows for flexible and eye-catching displays.
The automotive industry utilizes magnetic fasteners for holding panels in place during assembly, attaching sensors and wiring, and securing removable components. In the medical industry, magnetic fasteners are found in devices like MRI machines, surgical tools, and prosthetic limbs. The aerospace industry makes use of magnetic fasteners in aircraft interiors, access panels, and specialized fastening systems. The inherent reliability and non-invasive nature of magnetic fasteners make them suitable for these demanding and specialized applications. These are merely a few examples of the nearly limitless versatility of magnetic fasteners.
## Advantages Over Traditional Fastening Methods: Weighing the Benefits
Choosing the right fastening method is critical for any project, and magnetic fasteners offer several advantages over traditional methods like screws, nails, bolts, and adhesives. Understanding these advantages can help you make informed decisions and select the best solution for your needs.
One of the most significant advantages is the ease of use. Magnetic fasteners require no tools for installation or removal, saving time and effort. This is particularly beneficial in applications where frequent adjustments or reconfigurations are required. Another major advantage is the non-damaging nature of magnetic fastening. Unlike drilling or nailing, magnets do not penetrate the material, minimizing the risk of damage or blemishes. This is particularly important in applications involving fragile or sensitive materials.
Furthermore, magnetic fasteners often provide a cleaner aesthetic than traditional fasteners. They eliminate the visible heads of screws or the residue from adhesives, creating a more seamless and professional look. Magnetic fasteners can also be easily concealed, further enhancing the aesthetic appeal. Finally, magnetic fasteners are often reusable and adjustable, offering a more sustainable and flexible solution than permanent fastening methods. This allows for easy modifications and upgrades without damaging the materials.
## Limitations and Considerations: Recognizing Potential Drawbacks
While magnetic fasteners offer numerous advantages, it’s important to acknowledge their limitations and consider potential drawbacks before choosing them for a particular application. Understanding these limitations will help ensure that magnetic fasteners are used effectively and safely.
One primary limitation is the requirement for a ferromagnetic material to which the magnet can attract. As discussed previously, non-ferromagnetic materials cannot be directly fastened using magnets. Another important consideration is the potential for demagnetization. Exposure to high temperatures, strong magnetic fields, or physical shocks can weaken a magnet’s holding force over time. Selecting the appropriate magnet material and protecting it from these conditions can help prevent demagnetization.
The holding strength of a magnetic fastener can also be affected by factors like air gaps, surface irregularities, and the presence of contaminants. Ensuring a clean and smooth contact surface is crucial for maximizing the holding force. Additionally, the load-bearing capacity of magnetic fasteners can be limited compared to traditional fasteners like screws or bolts. It’s important to carefully calculate the required holding strength and select a fastener that can safely support the load. Finally, in certain applications, the strong magnetic field generated by the fastener can interfere with sensitive electronic equipment. Careful placement and shielding may be necessary to mitigate this risk.
## The Future of Magnetic Fastening: Innovations and Emerging Trends
The field of magnetic fastening is constantly evolving, with ongoing research and development leading to new innovations and applications. Emerging trends point towards lighter, stronger, and more versatile magnetic fasteners that will further expand their appeal across various industries.
One key area of development is the creation of stronger and more temperature-resistant magnets. Researchers are exploring new magnet materials and manufacturing techniques that can enhance both strength and stability. Another trend is the integration of sensors and smart technology into magnetic fasteners. These “smart magnets” can provide real-time data on load, temperature, and other parameters, allowing for more precise monitoring and control.
The rapid growth of 3D printing is also revolutionizing the design and production of magnetic fasteners. 3D printing allows for the creation of complex and customized magnetic fastening solutions tailored to specific applications. This technology can also be used to embed magnets directly into 3D-printed parts, creating seamless and integrated fastening systems. As technology continues to advance, magnetic fastening will likely play an increasingly important role in various industries, offering innovative solutions for a wide range of fastening challenges.
## Conclusion
Magnetic fastening provides a viable, efficient, and often superior alternative to traditional fastening methods. Its ease of use, strength, non-destructive nature, and aesthetic appeal make it a versatile solution for diverse applications, ranging from simple home projects to complex industrial assemblies. Understanding the different types of magnetic fasteners, calculating holding strength, considering the material properties, and recognizing the limitations are important for making informed choices. As technology advances, continued innovation in magnet materials, smart technologies, and 3D printing will further enhance the capabilities and expand the applications of magnetic fastening, solidifying its role as a powerful and versatile fastening solution of the future.
## FAQ
### What are the main advantages of using magnetic fasteners?
Magnetic fasteners are tool-free, easy to use, non-damaging to surfaces, offer a clean aesthetic, and can be reusable and adjustable. They save time and effort and are ideal for applications requiring frequent adjustments.
### Can magnetic fasteners be used on any material?
No. Magnetic fasteners only work directly with ferromagnetic materials like iron, steel, nickel, and cobalt. For non-ferromagnetic materials, a ferromagnetic component (like a steel plate) needs to be integrated.
### How do I determine the right holding strength for a magnetic fastener?
Consider factors like magnet type and grade, size and shape, the material being attached to, the thickness and surface finish of the materials, and any air gaps. Consult manufacturer ratings and apply safety factors. Consider using multiple smaller magnets for better load distribution.
### Are magnetic fasteners reusable?
Yes, most magnetic fasteners can be repeatedly attached and removed without damaging the magnet or the surfaces involved, making them a more sustainable option than some adhesives or permanent fasteners.
### What are some common applications of magnetic fasteners?
Common applications include woodworking jigs, cabinet doors and drawers, retail displays, automotive assembly, medical devices, and aerospace components. They are commonly used anywhere a strong, removaable attachment is required.
### Can magnetic fasteners weaken over time?
Yes, magnets can weaken (demagnetize) due to exposure to high temperatures, strong magnetic fields, or physical shocks. Choosing suitable magnet material and protecting it from these conditions can help prevent demagnetization.
### Are there different types of magnetic fasteners?
Yes, there are various types, including magnetic catches, latches, hooks, and strips, each designed for specific applications and holding strength requirements.
### What are the limitations of magnetic fastening?
Limitations include the need for ferromagnetic materials, potential demagnetization, sensitivity to air gaps and surface irregularities, limited load-bearing capacity compared to traditional fasteners, and possible interference with sensitive electronic equipment in certain applications.
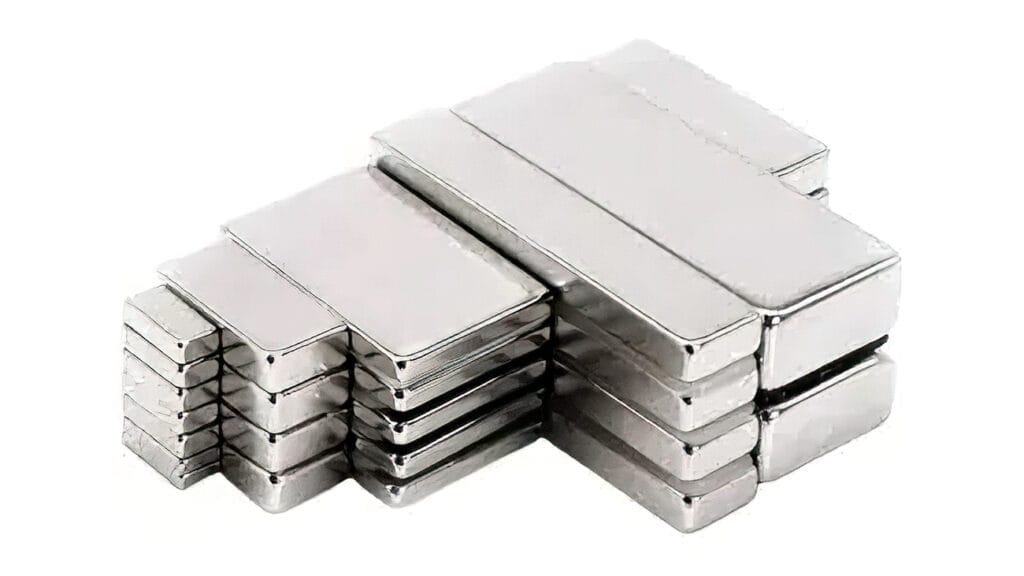