# Choosing the Right Cylindrical Magnet: Your Ultimate Buyer’s Guide for Performance and Precision
Cylindrical magnets, those unassuming yet powerful little cylinders, are the unsung heroes in countless applications, from holding fridge magnets to enabling complex industrial machinery. But with a vast array of sizes, materials, and strengths available, selecting the *right* cylindrical magnet for your specific needs can feel like navigating a magnetic maze. Fear not! This comprehensive buyer’s guide is designed to demystify the world of cylindrical magnets, acting as your expert compass to ensure you choose the perfect magnet, every time. Whether you’re an engineer designing a cutting-edge device, a hobbyist tinkering in your workshop, or simply curious about these fascinating components, this article will equip you with the knowledge to confidently navigate the selection process and unlock the full potential of cylindrical magnets. Let’s dive in and discover the magnetic force that’s right for you.
## What Exactly Are Cylindrical Magnets and Why Are They So Versatile?
Have you ever stopped to consider just how many things around you rely on magnets? From the speakers in your phone to the motors in your car, magnets are indispensable. Cylindrical magnets, in particular, offer a unique combination of shape and magnetic properties that make them incredibly versatile. Think of them as magnetic rods, longer than they are wide, presenting a concentrated magnetic field at their ends. This shape is perfect for applications where you need a strong, localized magnetic force, like sensors, actuators, and holding assemblies.
Their versatility stems from a few key factors. Firstly, the cylindrical shape itself allows for easy integration into various designs. They can be inserted into holes, aligned along surfaces, or used in rotating assemblies. Secondly, they are available in a wide range of magnetic materials, each with its own set of characteristics, allowing for customization based on strength, temperature resistance, and cost. We can use incredibly powerful neodymium magnets for situations demanding maximum force in a small space, or opt for cost-effective ferrite magnets for simpler applications. This adaptability makes cylindrical magnets a go-to choice across diverse industries and applications.
## Neodymium, Ferrite, or Samarium Cobalt? Deciphering Cylindrical Magnet Materials
When venturing into the world of cylindrical magnets, you’ll quickly encounter a bewildering array of materials – neodymium, ferrite, alnico, samarium cobalt – each with distinct properties and price points. Choosing the right material is paramount to ensuring your magnet performs as intended and fits within your budget. Let’s break down the most common contenders:
**Neodymium Magnets (NdFeB):** These are the superstars of the magnet world. Known for their exceptional strength – the strongest type of permanent magnet commercially available – neodymium magnets are the go-to choice when you need maximum magnetic force in a compact size. Imagine holding a tiny neodymium magnet effortlessly suspending several pounds of steel! This power comes with a caveat: they are more brittle and have lower temperature resistance compared to some other materials. They are also more prone to corrosion, often requiring coatings like nickel or epoxy. Ideal for: high-performance applications, sensors, motors, compact designs requiring strong holding force.
**Ferrite Magnets (Ceramic):** If budget is a primary concern, ferrite magnets are your champions. They are significantly less expensive than neodymium and offer good corrosion resistance and high temperature resistance, making them reliable in harsh environments. However, they are considerably weaker than neodymium magnets for the same size. Think of refrigerator magnets – often made of ferrite. Useful for: cost-sensitive applications, motors, speakers, holding applications in humid or high-temperature environments.
**Samarium Cobalt Magnets (SmCo):** These magnets are the high-temperature heroes. While not as strong as neodymium, samarium cobalt magnets boast excellent temperature stability and corrosion resistance, even exceeding ferrite in temperature tolerance. This makes them perfect for applications where magnets are exposed to extreme heat or harsh chemicals. They are also more brittle and expensive than ferrite, placing them in a niche category for demanding environments. Best for: high-temperature applications, aerospace, sensors in challenging environments, situations requiring excellent corrosion resistance.
**Alnico Magnets:** These are the classic workhorses of magnetism. Composed primarily of aluminum, nickel, and cobalt, alnico magnets offer good temperature stability and corrosion resistance. They are less brittle than ceramic or rare earth magnets, and can be magnetized in complex shapes. However, they are also weaker than neodymium and ferrite magnets, and can be more easily demagnetized compared to rare earth magnets. Often used historically and still in some specialty applications. Good for: guitar pickups, motors and generators operating at high temperatures, applications requiring complex shapes.
To help you visualize the differences, here’s a table summarizing key characteristics:
| Material | Strength | Temperature Resistance | Corrosion Resistance | Cost | Brittleness | Common Applications |
|——————–|—————–|————————|———————-|————–|—————–|———————————————————–|
| **Neodymium (NdFeB)** | Very High | Low-Moderate | Low (Requires Coating) | High | High | Motors, Sensors, High-Performance Devices, Compact Designs |
| **Ferrite (Ceramic)** | Moderate-Low | High | High | Low | Moderate | Refrigerator Magnets, Speakers, Cost-Effective Motors |
| **Samarium Cobalt (SmCo)**| High | Very High | High | Very High | High | High-Temperature Sensors, Aerospace, Harsh Environments |
| **Alnico** | Moderate | High | Good | Moderate-High | Low-Moderate | Guitar Pickups, High-Temperature Motors/Generators |
Choosing the right material hinges on your specific application requirements, considering factors like strength, operating temperature, environmental conditions, and budget.
## How Much Pull Force Do You Really Need? Understanding Magnet Strength and Grades
“How strong is it?” That’s likely one of the first questions you’ll ask when considering a cylindrical magnet. Magnet strength is a multifaceted concept, and understanding the key metrics will guide you in making the right choice. Two primary measures of magnet strength are **magnetic flux density (Gauss or Tesla)** – indicating the intensity of the magnetic field – and **pull force (pounds or kilograms)** – the force required to detach the magnet from a steel plate.
**Gauss & Tesla:** These units measure the magnetic field strength at a point. While technically important, Gauss or Tesla values alone are not always the most practical metric for choosing a magnet for holding or attracting applications. A higher Gauss rating indicates a stronger local magnetic field, but it doesn’t directly translate to how well a magnet will hold onto something.
**Pull Force:** This is often the more relevant metric in practical applications, especially when you need magnets for holding, lifting, or attaching. Pull force is typically measured as the force required to pull the magnet directly away from a flat steel plate under specific conditions. Manufacturers usually provide pull force values for their magnets. Keep in mind that pull force is influenced by factors beyond just the magnet itself, including the thickness and material of the steel plate, the surface contact area, and the direction of the applied force.
**Magnet Grades:** Particularly for neodymium magnets, you’ll encounter grades like N35, N42, N52, and so on. These grades indicate the maximum energy product of the magnet material, essentially a measure of its magnetic performance. A higher grade number signifies a stronger magnet *for the same size*. For instance, an N52 neodymium magnet of the same dimensions as an N35 magnet will be significantly stronger. Opt for higher grades when maximum strength is paramount and size constraints are tight. However, higher grades also come with a price premium.
**Practical Considerations for Pull Force:**
* **Air Gap:** The pull force drops dramatically with even a small air gap between the magnet and the steel. Consider any coatings, non-magnetic layers, or gaps in your application that might reduce pull force.
* **Surface Contact:** A flat, clean surface provides optimal contact for maximum pull force. Irregular surfaces or debris will reduce the effective holding power.
* **Shear Force vs. Pull Force:** Pull force (perpendicular to the surface) is generally higher than shear force (parallel to the surface). If your application involves shear forces, factor in a safety margin.
Therefore, when determining the necessary pull force, consider the actual load you need to hold, any air gaps present in your application, and the desired safety factor. Don’t solely rely on Gauss ratings – focus on pull force specifications provided by manufacturers for practical guidance.
## Diameter, Length, and Aspect Ratio: How Cylindrical Magnet Dimensions Impact Performance
Beyond material and strength, the physical dimensions of your cylindrical magnet – its diameter and length – play a crucial role in its performance and suitability for your application. These dimensions directly influence the magnetic field strength and the available surface area for magnetic contact.
**Diameter:** A larger diameter generally leads to a stronger magnet. Increasing the diameter expands the cross-sectional area of the magnet, effectively increasing the total magnetic flux it can generate and project. This translates to a higher pull force, especially when attracting to a flat surface. However, larger diameter magnets are also heavier and bulkier, which might be a constraint in space-sensitive designs.
**Length:** Increasing the length of a cylindrical magnet also enhances its strength, but not as dramatically as increasing the diameter. The length primarily affects the depth and reach of the magnetic field. A longer magnet will project its magnetic field further out from its ends compared to a shorter, stubbier magnet of the same diameter and material. This can be beneficial in applications where you need to attract objects at a distance or create a field that extends over a larger area.
**Aspect Ratio (Length/Diameter):** This ratio is crucial for optimizing magnet performance.
* **Long and Thin Cylinders (High Aspect Ratio):** These tend to have a more focused magnetic field at their ends and are suitable for applications where you need deep penetration or are working with thicker materials. However, they can be more prone to breakage, especially with brittle materials like neodymium.
* **Short and Stubby Cylinders (Low Aspect Ratio):** These offer a wider, less focused magnetic field and are often preferred for holding applications where maximum surface contact is desired. They are generally more robust and less prone to mechanical damage.
**Choosing the Right Dimensions:**
* **Space Constraints:** Your application might dictate specific size limitations. Measure available space carefully to ensure the magnet fits appropriately.
* **Required Pull Force:** Determine the necessary pull force based on your load requirements. Adjust diameter and length accordingly, prioritizing diameter for greater strength.
* **Magnetic Field Shape:** Consider the desired shape and reach of the magnetic field. Longer magnets extend the field further, while shorter, wider magnets offer broader surface attraction.
* **Mechanical Stability:** Be mindful of the aspect ratio, especially with brittle neodymium magnets. Opt for shorter, stubbier designs if mechanical robustness is critical or if your application involves significant stress on the magnet.
Manufacturers typically provide dimensions in their magnet specifications. Carefully consider your application’s needs and select dimensions that optimize performance while adhering to any size or shape limitations.
## What Applications Are Cylindrical Magnets Best Suited For? Exploring Versatility
The cylindrical shape unlocks a diverse range of applications for these magnets across various industries and everyday life. Let’s explore some key areas where cylindrical magnets excel:
**Sensors:** Cylindrical magnets are instrumental components in numerous sensor types.
* **Proximity Sensors:** Used to detect the presence or absence of an object. A cylindrical magnet can be mounted on a moving part, and its presence (or absence) is detected by a nearby Hall effect sensor, triggering a signal. Think of door sensors, position sensors in machinery, and safety interlocks.
* **Magnetic Reed Switches:** These switches are activated by the presence of a magnetic field. A cylindrical magnet brought near a reed switch causes its internal contacts to close. Applications include liquid level sensors, flow meters, and security systems.
* **Rotary Encoders:** For precise position and speed measurement, cylindrical magnets are often integrated into rotary encoders. As a shaft rotates, magnets fixed to it trigger sensors, providing pulses that are counted to determine angular position and speed.
**Motors and Generators:** Cylindrical magnets are essential in electric motors and generators, contributing to efficient energy conversion.
* **Small DC Motors:** In many small DC motors, cylindrical magnets are used in the stator (stationary part) to create a magnetic field that interacts with the rotor (rotating part) windings, causing the rotation. Think of motors in toys, small appliances, and automotive components.
* **Generators:** Conversely, in generators, rotating a cylindrical magnet near coils of wire induces an electric current. This principle is used in various power generation systems, including smaller-scale and specialized generators.
**Holding and Fastening:** The inherent holding power of cylindrical magnets makes them invaluable for various fastening and assembly applications.
* **Magnetic Clamps and Fixtures:** Cylindrical magnets can be incorporated into clamps, jigs, and fixtures to securely hold workpieces during machining, welding, or assembly processes. They offer quick and repositionable holding solutions.
* **Magnetic Separators:** In industries like recycling, food processing, and mining, cylindrical magnets are used in magnetic separators to remove ferrous contaminants from materials.
* **Magnetic Closures:** From cabinet doors to jewelry clasps, small cylindrical magnets provide clean and reliable magnetic closures.
**Other Applications:**
* **Medical Devices:** In MRI machines, specialized cylindrical magnets play a crucial role in generating the strong magnetic fields required for imaging. In smaller medical devices, they can be used for drug delivery systems or surgical instruments.
* **Audio Equipment:** In loudspeakers and headphones, cylindrical magnets are fundamental to converting electrical signals into sound waves.
* **Toys and Novelties:** From magnetic building blocks to fridge magnets, cylindrical magnets bring fascination and functionality to countless toys and novelty items.
The versatility stems from the combination of shape, magnetic strength, and material options, allowing cylindrical magnets to be tailored to a vast array of functions across diverse sectors.
## Which Coating is Right for Your Cylindrical Magnet? Corrosion and Protection Considerations
While magnets themselves are robust, many magnetic materials, especially neodymium, are susceptible to corrosion, chipping, or abrasion in certain environments. Applying a protective coating is often essential to extend the lifespan and maintain the performance of your cylindrical magnets. Choosing the right coating depends on the intended application and the environmental conditions the magnet will face.
**Common Coating Types:**
* **Nickel Plating (Ni-Cu-Ni):** This is the most common and cost-effective coating for neodymium magnets. It typically involves multiple layers – nickel, copper, and then another layer of nickel – providing good protection against humidity and mild corrosion. Nickel plating offers a bright, metallic finish and is suitable for general indoor applications and moderately humid environments. However, it might not be sufficient for harsh chemical exposure or saltwater environments.
* **Epoxy Coating:** Epoxy coatings provide excellent protection against corrosion, humidity, and even some chemicals. They offer a tougher and more durable barrier compared to nickel plating. Epoxy coatings are typically black or gray and provide a non-metallic, smooth finish. Ideal for outdoor applications, humid environments, and situations where chemical resistance is required.
* **Gold Plating:** Gold plating offers excellent corrosion resistance and is often used in medical devices and applications requiring biocompatibility or high reliability. Gold is chemically inert and provides a luxurious, conductive finish. However, it’s a more expensive coating option.
* **Zinc Plating:** Zinc plating is another cost-effective option, offering good corrosion resistance, particularly in dry environments. It’s less durable than nickel or epoxy in humid conditions. Zinc coatings often have a slightly duller, grayish finish.
* **Chrome Plating:** Chrome plating provides a hard, durable, and corrosion-resistant finish. It offers a bright, shiny appearance and is more robust against abrasion than nickel plating. Chrome plating is often used in decorative applications and environments requiring wear resistance.
* **Parylene Coating:** Parylene is a thin, conformal polymer coating applied in a vacuum process. It offers excellent moisture and chemical barrier properties, as well as biocompatibility. Parylene coatings are extremely thin and transparent, preserving the magnet’s original dimensions with minimal added thickness. Suitable for demanding applications, including medical and aerospace.
**Factors to Consider When Choosing a Coating:**
* **Environment:** Will the magnet be exposed to humidity, saltwater, chemicals, or extreme temperatures? Select coatings accordingly (epoxy, gold, parylene for harsh environments).
* **Corrosion Resistance:** If corrosion is a major concern, opt for coatings known for their high corrosion resistance (epoxy, gold, parylene, chrome).
* **Abrasion Resistance:** If the magnet will experience friction or wear, consider coatings with good abrasion resistance (chrome, epoxy).
* **Temperature Range:** Ensure the coating is suitable for the operating temperature range of your application. Some coatings have temperature limitations.
* **Appearance:** If aesthetics are important, choose a coating with the desired finish (nickel for bright metallic, epoxy for black/gray, chrome for shiny chrome finish).
* **Cost:** Coating options vary in cost. Nickel and zinc are generally more affordable, while gold and parylene are more expensive.
* **Thickness:** Consider the added thickness of the coating, especially in tight tolerance applications. Parylene is the thinnest option; other coatings can add a few microns to tens of microns.
Matching the coating to your application’s specific environmental demands is crucial for ensuring long-term magnet performance and preventing premature failure due to corrosion or wear.
## Direction Matters: Understanding Magnetization in Cylindrical Magnets
Magnetization direction refers to the orientation of the magnetic poles within a magnet. For cylindrical magnets, the magnetization direction dictates how the magnetic field is projected and how the magnet interacts with its surroundings. Understanding magnetization direction is essential for selecting the right magnet for your application.
**Common Magnetization Directions for Cylindrical Magnets:**
* **Axial Magnetization:** This is the most common magnetization type for cylindrical magnets. In axial magnetization, the magnetic poles are located at the flat, circular ends of the cylinder, with the magnetic field flowing along the axis of the cylinder. Imagine a north pole at one flat end and a south pole at the opposite end. Axially magnetized cylindrical magnets are ideal for applications where you need a strong magnetic field projected from the ends, such as attracting objects along the axis of the cylinder or creating a holding force perpendicular to the cylinder’s length.
* **Diametrical Magnetization:** In diametrical magnetization, the magnetic poles are located on the curved cylindrical surface, typically across the diameter. Imagine a north pole on one side of the cylinder and a south pole on the opposite side. Diametrically magnetized cylindrical magnets are used in applications where you need the magnetic field to be projected radially outward, such as in rotors of motors, magnetic couplings, or applications involving rotation around the cylinder’s axis.
**Impact of Magnetization Direction on Applications:**
* **Holding Applications:** For most holding or attracting applications where you want to attach the magnet to a flat surface, axially magnetized cylindrical magnets are typically the best choice, as they concentrate the magnetic force at the flat ends for maximum pull force.
* **Rotary Applications (Motors, Generators):** Diametrically magnetized cylindrical magnets are often used in rotors for motors and generators. The radial magnetic field is crucial for interaction with stator windings and generating rotational motion.
* **Sensors (Reed Switches, Hall Effect Sensors):** The choice of magnetization direction depends on the sensor type and the desired detection mechanism. Axially or diametrically magnetized magnets can be used, depending on how the magnetic field needs to interact with the sensor.
* **Magnetic Couplings:** Diametrically magnetized cylindrical magnets can be used in magnetic couplings to transmit rotational motion without physical contact.
**Specifying Magnetization Direction:**
When ordering cylindrical magnets, it’s crucial to specify the desired magnetization direction – axial or diametrical – to ensure you receive magnets that are appropriately magnetized for your application. Manufacturers will typically indicate magnetization direction in product specifications, often using diagrams to visually represent the pole orientation. If unsure, consult with the magnet supplier to determine the optimal magnetization direction for your specific needs.
Incorrect magnetization can lead to ineffective performance or even complete failure of your application to function as intended. Therefore, understanding and carefully considering the magnetization direction is a critical step in choosing the right cylindrical magnet.
## Tolerance & Precision: How Accurate Do Your Cylindrical Magnets Need to Be?
In many applications, particularly in precision engineering and sensitive devices, the dimensional tolerances of cylindrical magnets are critical. Tolerance refers to the permissible variation in size from the specified nominal dimensions. Tighter tolerances mean more precise magnet dimensions, while looser tolerances allow for greater variation. Choosing the appropriate tolerance level is crucial for proper fit, function, and performance, balancing precision requirements with cost considerations.
**Standard Tolerances vs. Precision Tolerances:**
* **Standard Tolerances:** Most commercially available cylindrical magnets are manufactured with standard tolerances, typically expressed as ± a certain value (e.g., ±0.1mm or ±0.004 inches). Standard tolerances are generally sufficient for many general-purpose applications where dimensional variations within a reasonable range are acceptable. They are also more cost-effective to manufacture.
* **Precision Tolerances:** For applications demanding high accuracy and precise fit, precision cylindrical magnets with tighter tolerances are required. These magnets undergo more stringent manufacturing processes and quality control, resulting in dimensions closer to the nominal specified values. Precision tolerances come at a higher cost but are necessary for critical applications.
**Factors Influencing Tolerance Requirements:**
* **Fit and Assembly:** If the cylindrical magnet needs to fit precisely into a cavity, hole, or assembly, tight tolerances are crucial to ensure proper fit and prevent mechanical interference or gaps. Consider mating part tolerances as well.
* **Sensor Accuracy:** In sensor applications where magnet position or alignment is critical for accurate sensing, tight tolerances on magnet dimensions are essential to maintain consistent and reliable sensor performance.
* **Magnetic Circuit Performance:** In certain magnetic circuits designs, precise magnet dimensions can influence the magnetic field distribution and overall circuit performance. Tighter tolerances can ensure predictable and consistent magnetic characteristics.
* **High-Speed Rotation:** In rotating applications like motors or generators, imbalances due to dimensional variations in magnets can lead to vibrations and reduced performance at high speeds. Precision tolerances can minimize these imbalances.
* **Automation and Handling:** In automated assembly processes, magnets with consistent dimensions are easier to handle and reliably position by robotic equipment. Tighter tolerances improve automation efficiency.
**Specifying Tolerances:**
When ordering cylindrical magnets, clearly specify the required tolerances for diameter, length, and any other critical dimensions. If precision tolerances are needed, explicitly request “precision grade” or specify the desired tolerance range (e.g., ±0.05mm or tighter). Be aware that tighter tolerances typically come with an increased cost and potentially longer lead times.
Consider the trade-off between tolerance requirements, cost, and lead time. For many applications, standard tolerances are perfectly adequate. However, for precision applications where dimensional accuracy is paramount, investing in precision cylindrical magnets with tighter tolerances is a necessary investment to ensure optimal performance and reliability. Consult with your magnet supplier to determine achievable tolerance levels and their associated costs for your specific requirements.
## Extreme Conditions? Temperature Resistance of Cylindrical Magnets Explained
Temperature is a critical factor that can significantly impact the performance of permanent magnets. Each magnet material has a specific temperature range within which it retains its magnetic properties effectively. Exceeding the maximum operating temperature can lead to irreversible demagnetization, weakening, or even complete loss of magnetic strength. Understanding the temperature resistance of cylindrical magnets is crucial for selecting the right material for your application’s operating environment.
**Key Temperature Ratings:**
* **Maximum Operating Temperature (Curie Temperature):** This is the temperature at which a ferromagnetic material loses its ferromagnetism – it essentially becomes non-magnetic. While technically the highest possible temperature a magnet can withstand before losing its magnetism, it’s usually far beyond the *practical* operating temperature limit.
* **Maximum Service Temperature:** This is a more practical and relevant temperature rating. It indicates the maximum temperature a magnet can be exposed to *for extended periods* without significant irreversible demagnetization. Operating above the maximum service temperature will typically lead to a gradual but permanent loss of magnetic strength. Manufacturers usually specify maximum service temperatures for different grades and materials.
**Temperature Resistance of Common Magnet Materials:**
* **Ferrite Magnets:** Ferrite magnets boast excellent temperature resistance, with maximum service temperatures ranging from approximately 250°C to 300°C (482°F to 572°F), depending on the grade. This makes them suitable for high-temperature applications where strength is not the primary concern.
* **Alnico Magnets:** Alnico magnets also exhibit excellent temperature stability, capable of operating at temperatures up to 500°C or even higher (932°F+), depending on the specific alnico grade. They are well-suited for very high-temperature environments, though they are less powerful than neodymium or samarium cobalt.
* **Samarium Cobalt Magnets:** Samarium Cobalt magnets offer superior temperature resistance compared to neodymium magnets, with maximum service temperatures typically ranging from 250°C to 350°C (482°F to 662°F) or even higher for specialized grades. They maintain good strength at elevated temperatures, making them suitable for demanding thermal environments.
* **Neodymium Magnets:** Neodymium magnets have the lowest temperature resistance among these common materials. Standard neodymium magnets typically have maximum service temperatures ranging from 80°C to 150°C (176°F to 302°F), depending on the grade. High-temperature neodymium grades (e.g., with suffixes like “H,” “SH,” “UH,” “EH”) are available, pushing the maximum service temperature up to 200°C or even higher, but at a higher cost.
**Demagnetization at Elevated Temperatures:**
Even below the maximum service temperature, neodymium magnets can experience some degree of *reversible* demagnetization with temperature increase. This means their magnetic strength temporarily decreases as temperature rises but recovers when cooled back down (as long as the maximum service temperature wasn’t exceeded). However, exceeding the maximum service temperature leads to *irreversible* demagnetization, a permanent loss of strength that cannot be recovered.
**Factors to Consider for Temperature Resistance:**
* **Operating Temperature Range:** Determine the full temperature range your magnet will be exposed to during operation, including both normal and extreme temperatures.
* **Safety Factor:** Consider adding a safety margin to the maximum service temperature to account for unforeseen temperature spikes or variations.
* **Magnet Material Selection:** Choose a magnet material with a maximum service temperature that comfortably exceeds your application’s maximum operating temperature.
* **Temperature Stabilization:** In critical high-temperature applications, consider temperature stabilization techniques or magnet alloys specifically designed for high temperature stability.
* **Cooling:** If possible, incorporate cooling mechanisms to help maintain the magnet temperature within its safe operating range.
Always consult the manufacturer’s specifications for the maximum service temperature of specific cylindrical magnet grades and materials. Careful consideration of temperature resistance is crucial for ensuring long-term reliable performance, especially in applications operating in elevated or fluctuating temperature environments.
## Budget Matters: What is the Cost of Cylindrical Magnets and How to Save?
The cost of cylindrical magnets can vary significantly depending on several factors, including the magnet material, grade, size, coating, tolerance, magnetization direction, and order volume. Understanding these cost drivers and exploring cost-saving strategies is essential for making budget-conscious choices without compromising performance.
**Key Cost Factors:**
* **Magnet Material:** Neodymium magnets are generally the most expensive, followed by samarium cobalt, alnico, and then ferrite, which is the most cost-effective material. Material cost directly impacts the overall magnet price.
* **Magnet Grade:** Higher grades of neodymium magnets (e.g., N52 vs. N35) fetch a premium due to their enhanced magnetic performance. Choose a grade that meets your strength requirements without overspending on unnecessarily high grades.
* **Size and Volume:** Larger magnets and higher order volumes typically offer better per-unit pricing due to economies of scale in manufacturing. Smaller magnets and low volumes often incur higher per-unit costs.
* **Coating:** Coatings like nickel plating add a relatively small amount to the cost, while more specialized coatings like gold or parylene significantly increase the price due to material and processing costs. Select coatings only when necessary for corrosion protection or specific application requirements.
* **Tolerance and Precision:** Precision magnets with tighter tolerances are more expensive to manufacture due to stricter quality control and processing steps. Opt for standard tolerances when precision is not critical to minimize costs.
* **Magnetization Direction:** While magnetization process itself usually doesn’t drastically alter the price, specifying custom or less common magnetization directions might incur slightly higher costs. Axially magnetization cylindrical magnets are generally the most standard and cost-effective.
* **Supplier and Manufacturer:** Prices can vary between different magnet suppliers and manufacturers. Comparing quotes from multiple vendors is a smart way to identify competitive pricing.
**Cost-Saving Strategies:**
* **Optimize Material Choice:** If high strength is not paramount, consider ferrite magnets as a cost-effective alternative to neodymium. For moderate strength needs, alnico magnets might also be an option. Only use neodymium or samarium cobalt when their superior strength or temperature resistance is absolutely necessary.
* **Choose the Right Grade:** Select a magnet grade that adequately meets your pull force requirements without opting for unnecessarily high grades (e.g., if N35 is sufficient, avoid N5
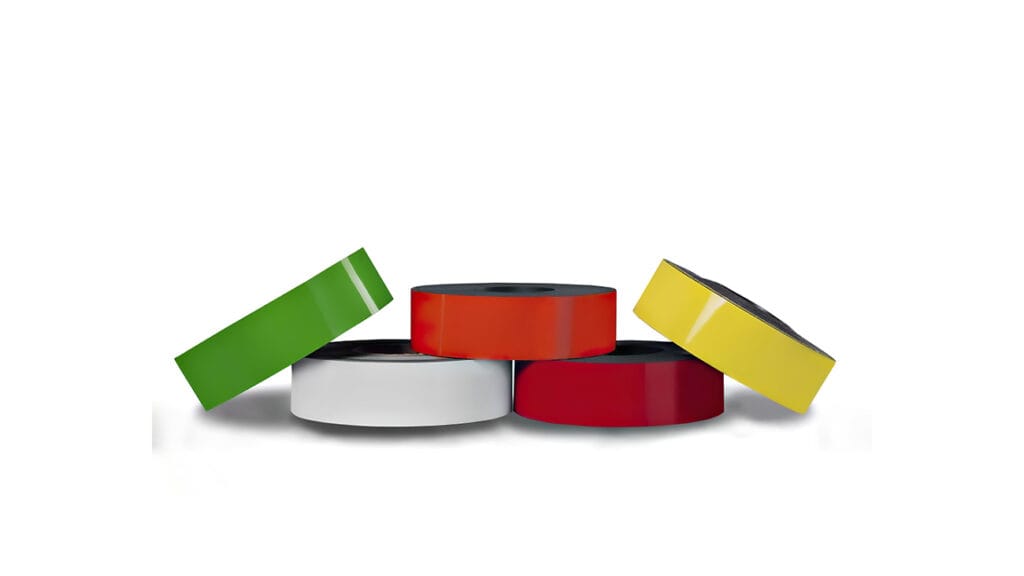