# Magnetic Fasteners 101: Exploring Types, Applications, and Best Practices
This comprehensive guide delves into the fascinating world of magnetic fasteners. Learn about the various types available, from powerful neodymium magnets to flexible magnetic strips, and discover their diverse applications in industries ranging from manufacturing to crafting. We’ll also explore best practices for selection, installation, and maintenance to ensure optimal performance and longevity, equipping you with the knowledge to choose the right magnetic fastener for your specific needs.
## Understanding the Power of Magnetic Fasteners
Magnetic fasteners offer a compelling alternative to traditional mechanical fasteners like screws, bolts, and rivets. They leverage the inherent power of magnetism to create secure and often easily reversible connections. This makes them ideal for applications where frequent adjustments or disassembly are required, or where a clean, aesthetically pleasing appearance is desired. Unlike mechanical fasteners, magnetic fasteners don’t require drilling or tapping, preserving the integrity of the materials being joined.
The versatility of magnetic fasteners stems from their ability to bond to ferrous metals (metals containing iron), such as steel and iron. The strength of the bond depends on several factors, including the type and size of magnet, the material being fastened, and the surface area of contact. Choosing the right magnetic fastener involves careful consideration of these factors to ensure a reliable and long-lasting connection. The ever-increasing demand for innovative fastening solutions has propelled advancements in magnetic fastener technology, leading to stronger, more adaptable, and cost-effective options.
## Key Types of Magnetic Fasteners: A Comprehensive Overview
The world of magnetic fasteners is diverse, with each type offering unique characteristics suited for specific applications. Understanding these differences is crucial for selecting the appropriate fastener for your project. Let’s explore some of the most common types:
* **Neodymium Magnets:** These are the strongest type of permanent magnet available commercially. Made from an alloy of neodymium, iron, and boron, they boast exceptional holding power for their size. They’re commonly used in high-strength applications like motors, sensors, and closures. Be cautious as they are brittle and can chip or break if subjected to excessive impact.
* **Ferrite Magnets:** Also known as ceramic magnets, ferrite magnets are cost-effective and resistant to corrosion. While not as powerful as neodymium magnets, they offer a good balance of strength and durability. They are frequently used in speakers, magnetic separators, and holding devices.
* **Alnico Magnets:** Composed of aluminum, nickel, and cobalt, alnico magnets are known for their high temperature stability and resistance to demagnetization. They are suitable for applications operating in harsh environments, such as generators, sensors, and high-temperature holding fixtures.
* **Flexible Magnetic Sheets and Strips:** Made by embedding magnetic particles in a flexible binder, these materials can be easily cut, shaped, and adhered to various surfaces. They’re ideal for applications like refrigerator magnets, signage, and door seals.
* **Magnetic Catches and Latches:** These fasteners combine a magnet with a metal strike plate to create a secure closure. They are commonly used on cabinet doors, drawers, and access panels. They provide a clean, uncluttered look and are often adjustable.
The choice between these different types depends on the required holding strength, operating temperature, corrosion resistance, budget, and application-specific needs. Careful evaluation of these factors will lead to optimal performance and longevity of the magnetic fastener.
## Diverse Applications Across Industries and Everyday Life
The versatility of magnetic fasteners has led to their adoption in a wide range of industries and everyday applications. Their ability to provide secure, reversible, and aesthetically pleasing connections makes them a valuable solution for numerous fastening challenges.
In the manufacturing sector, magnetic fasteners are utilized in assembly lines for quick and easy component attachment. They are also found in jigs and fixtures for holding parts during machining and welding. The aerospace industry employs magnetic fasteners for securing access panels and attaching lightweight components. Similarly, the automotive industry uses them in sensors, speakers, and various interior trim elements.
Beyond industrial applications, magnetic fasteners are ubiquitous in everyday life. Refrigerator magnets, magnetic knife racks, and magnetic cabinet closures are just a few examples. They are also used in crafting, hobby projects, and educational tools. The medical field utilizes magnetic fasteners in medical devices and implants, leveraging their biocompatibility and non-invasive nature. The retail industry employs magnetic fasteners in displays and shelving systems, allowing for easy reconfiguration and product placement adjustments.
The increasing demand for efficient and versatile fastening solutions ensures the continued growth and innovation of magnetic fastener applications. From holding heavy-duty components in industrial machinery to securing delicate items in everyday household products, magnetic fasteners are continuously evolving to meet the ever-changing needs of diverse industries.
## Key Factors in Selecting the Right Magnetic Fastener
Choosing the correct magnetic fastener is essential for ensuring optimal performance and longevity. Several factors must be considered to match the fastener to the specific application requirements:
* **Holding Strength:** This is the most crucial factor. Determine the minimum force required to hold the components together securely. Overestimating the necessary holding strength can lead to unnecessary cost, while underestimating it can result in failure.
* **Material Compatibility:** Ensure the magnet is compatible with the materials being joined. The magnet must be able to effectively attract the ferrous metal components. Consider using steel backing plates to improve the magnetic attraction to non-ferrous materials or thin ferrous materials.
* **Environmental Conditions:** Consider the operating temperature, humidity, and exposure to corrosive substances. Select a magnet with appropriate corrosion resistance and temperature stability for the intended environment. Neodymium magnets, for instance, can be susceptible to corrosion in humid environments, while alnico magnets excel in high-temperature applications.
* **Size and Shape:** Choose a size and shape that fits the available space and surface area. Larger magnets generally provide greater holding strength, but may not be practical for certain applications. Magnetic fasteners come in various shapes, including discs, blocks, rings, and rods.
* **Cost:** Balance the desired performance characteristics with the budget constraints. While neodymium magnets offer superior holding strength, they are also more expensive than ferrite magnets. Consider the long-term cost benefits of choosing a more durable and reliable magnet, even if it has a higher initial cost.
Careful consideration of these factors will help you select a magnetic fastener that meets the specific needs of your application, ensuring a secure, reliable, and long-lasting connection.
## Installation Techniques and Best Practices
Proper installation is crucial for maximizing the performance and lifespan of magnetic fasteners. Adhering to best practices ensures a secure and reliable connection.
* **Surface Preparation:** Clean the surfaces thoroughly before attaching the magnet. Remove any dirt, grease, oil, or rust that may impede the magnetic attraction. Use a suitable solvent or cleaning agent to prepare the surfaces.
* **Adhesive Application (if applicable):** If using an adhesive to bond the magnet to a non-ferrous surface, choose an adhesive that is compatible with both the magnet and the substrate. Apply the adhesive evenly and according to the manufacturer’s instructions. Consider using a primer on the substrate to improve adhesion.
* **Proper Alignment:** Ensure the magnet and the ferromagnetic surface are properly aligned. Misalignment can reduce the holding strength and potentially damage the magnet. Use jigs or fixtures to ensure accurate alignment during installation.
* **Avoiding Impact:** Avoid subjecting neodymium magnets to sudden impacts or excessive force, as they are brittle and can chip or break. Handle them with care during installation and avoid dropping them onto hard surfaces.
* **Using Strike Plates:** For magnetic catches and latches, ensure the strike plate is properly positioned and aligned with the magnet. The strike plate should be made of a suitable ferromagnetic material to maximize the holding force.
* **Testing and Inspection:** After installation, test the connection to ensure it provides adequate holding strength. Inspect the magnet and the surrounding area for any signs of damage or misalignment.
By following these installation techniques and best practices, you can ensure that your magnetic fasteners provide a secure, reliable, and long-lasting connection.
## Maintaining Magnetic Fasteners for Longevity
While magnetic fasteners are generally robust, proper maintenance can extend their lifespan and ensure consistent performance.
* **Regular Cleaning:** Keep the magnet and the surrounding area clean to prevent the accumulation of dirt, dust, and debris. Use a soft cloth or brush to remove any contaminants. Avoid using harsh chemicals or abrasive cleaners, as they may damage the magnet’s surface.
* **Protecting from Corrosion:** If the magnet is exposed to a corrosive environment, apply a protective coating or sealant to prevent rust and degradation. Consider using magnets with a corrosion-resistant coating, such as nickel plating or epoxy coating.
* **Avoiding Demagnetization:** Avoid exposing magnets to extremely high temperatures or strong external magnetic fields, as these can cause demagnetization. Store magnets in a cool, dry place away from electrical equipment and other magnets.
* **Inspection and Replacement:** Regularly inspect the magnets for any signs of damage, such as cracks, chips, or corrosion. Replace any damaged magnets promptly to prevent failure and potential safety hazards.
* **Lubrication (for moving parts):** For magnetic catches and latches with moving parts, apply a light lubricant to the moving parts to ensure smooth operation.
By following these maintenance guidelines, you can ensure that your magnetic fasteners continue to provide reliable and long-lasting performance.
## Understanding Magnetic Forces and Safety Considerations
Working with magnets, especially strong neodymium magnets, requires awareness of the forces involved and adherence to safety precautions.
* **Pinch Points:** Strong magnets can attract to each other or to ferromagnetic materials with considerable force, creating pinch points that can cause injury. Exercise caution when handling magnets, especially when bringing them close to metal objects or other magnets.
* **Impact Hazards:** Neodymium magnets are brittle and can shatter upon impact, launching sharp fragments that can cause eye injuries. Wear eye protection when handling neodymium magnets and avoid dropping them onto hard surfaces.
* **Magnetic Field Interference:** Strong magnetic fields can interfere with electronic devices, such as pacemakers, credit cards, and computer hard drives. Keep magnets away from these devices.
* **Swallowing Hazards:** Small magnets can be easily swallowed, especially by children. Swallowed magnets can cause serious internal injuries. Keep magnets out of reach of children.
* **Shipping Regulations:** Strong magnets are subject to shipping regulations due to their potential to interfere with aircraft navigation systems. Consult with a shipping carrier to ensure compliance with all applicable regulations.
Understanding these safety considerations and implementing appropriate precautions can help prevent accidents and ensure a safe working environment when handling magnetic fasteners.
## The Future of Magnetic Fastening Technology
The field of magnetic fastening is constantly evolving, driven by advancements in materials science, manufacturing techniques, and increasing demand for innovative fastening solutions. Several key trends are shaping the future of magnetic fastening technology:
* **Development of Stronger Magnets:** Research and development efforts are focused on creating magnets with even higher energy products and improved temperature stability. This will enable the use of smaller and more powerful magnets in a wider range of applications. Rare earth alternatives are also being heavily researched to reduce reliance on critical elements.
* **Customization and Integration:** Magnetic fasteners are becoming increasingly customized to meet specific application requirements. Manufacturers are offering tailored solutions with optimized shapes, sizes, and magnetic properties. Integration with other fastening technologies, such as adhesives and mechanical fasteners, is also gaining traction.
* **Smart Magnetic Fasteners:** Incorporating sensors and electronics into magnetic fasteners enables real-time monitoring of holding strength, temperature, and other parameters. This data can be used for predictive maintenance and process optimization.
* **Additive Manufacturing:** The ability to 3D print magnets opens up new possibilities for creating complex shapes and customized designs. Additive manufacturing enables the production of magnets with tailored magnetic properties and integrated features.
* **Sustainable Materials:** Environmentally friendly magnetic materials are gaining increasing attention. Researchers are exploring the use of recycled materials and bio-based binders in the production of magnetic fasteners.
These trends suggest a future where magnetic fastening technology plays an even more significant role in various industries. As advancements continue, we can expect to see stronger, more versatile, and more sustainable magnetic fasteners that meet the evolving needs of modern applications.
## Conclusion
Magnetic fasteners offer a versatile, efficient, and often aesthetically pleasing alternative to traditional mechanical fasteners. This guide has explored the different types of magnetic fasteners, their diverse applications, crucial selection factors, installation techniques, maintenance practices, safety considerations, and the exciting trends shaping their future. By understanding these aspects, you can effectively leverage the power of magnetic fasteners to enhance your projects and applications, ensuring secure, reliable, and long-lasting connections. Whether you are a seasoned engineer or a DIY enthusiast, the knowledge gained from this comprehensive overview provides a solid foundation for choosing and utilizing magnetic fasteners with confidence.
## FAQ
### H3 What are the key advantages of using magnetic fasteners?
Magnetic fasteners offer several advantages, including: ease of installation and removal, non-destructive fastening, clean aesthetics, adjustability, and suitability for frequent access. They also eliminate the need for drilling or tapping, preserving the integrity of the materials being joined.
### H3 Which type of magnetic fastener is the strongest?
Neodymium magnets are the strongest type of permanent magnet commercially available, offering exceptional holding power for their size. They are ideal for applications requiring high strength and compact designs.
### H3 How do I choose the right holding strength for my magnetic fastener?
To determine the required holding strength, calculate the minimum force needed to hold the components together securely. Consider the weight of the components, the expected loads, and any external forces that may act upon the connection. It’s generally better to slightly overestimate the required holding strength to ensure a reliable connection.
### H3 Can magnetic fasteners be used in outdoor applications?
Yes, but it’s crucial to select a magnetic fastener with appropriate corrosion resistance for the outdoor environment. Magnets with protective coatings, such as nickel plating or epoxy coating, are recommended. Ferrite magnets are also a good option due to their inherent corrosion resistance.
### H3 How can I prevent neodymium magnets from corroding?
Protect neodymium magnets from moisture and corrosive substances by applying a protective coating or sealant. Ensure the coating is fully intact to prevent corrosion from penetrating the magnet. Storing the magnets in a dry environment can also help prevent corrosion.
### H3 Are there any safety concerns when working with strong magnets?
Yes, strong magnets can create pinch points, interfere with electronic devices, and pose a swallowing hazard, especially for children. Exercise caution when handling strong magnets and keep them out of reach of children. Wear eye protection to prevent injuries from shattering fragments.
### H3 How do I demagnetize a magnet?
Demagnetizing a magnet typically requires exposing it to a strong alternating magnetic field or heating it above its Curie temperature (the temperature at which it loses its magnetic properties). Demagnetizing is often difficult and requires specialized equipment.
### H3 Can I use magnetic fasteners to join non-ferrous materials?
Magnetic fasteners primarily attract to ferromagnetic materials, such as steel and iron. To join non-ferrous materials, you can use an adhesive to bond the magnet to one component and attach a steel backing plate to the other component, allowing the magnet to adhere to the steel plate.
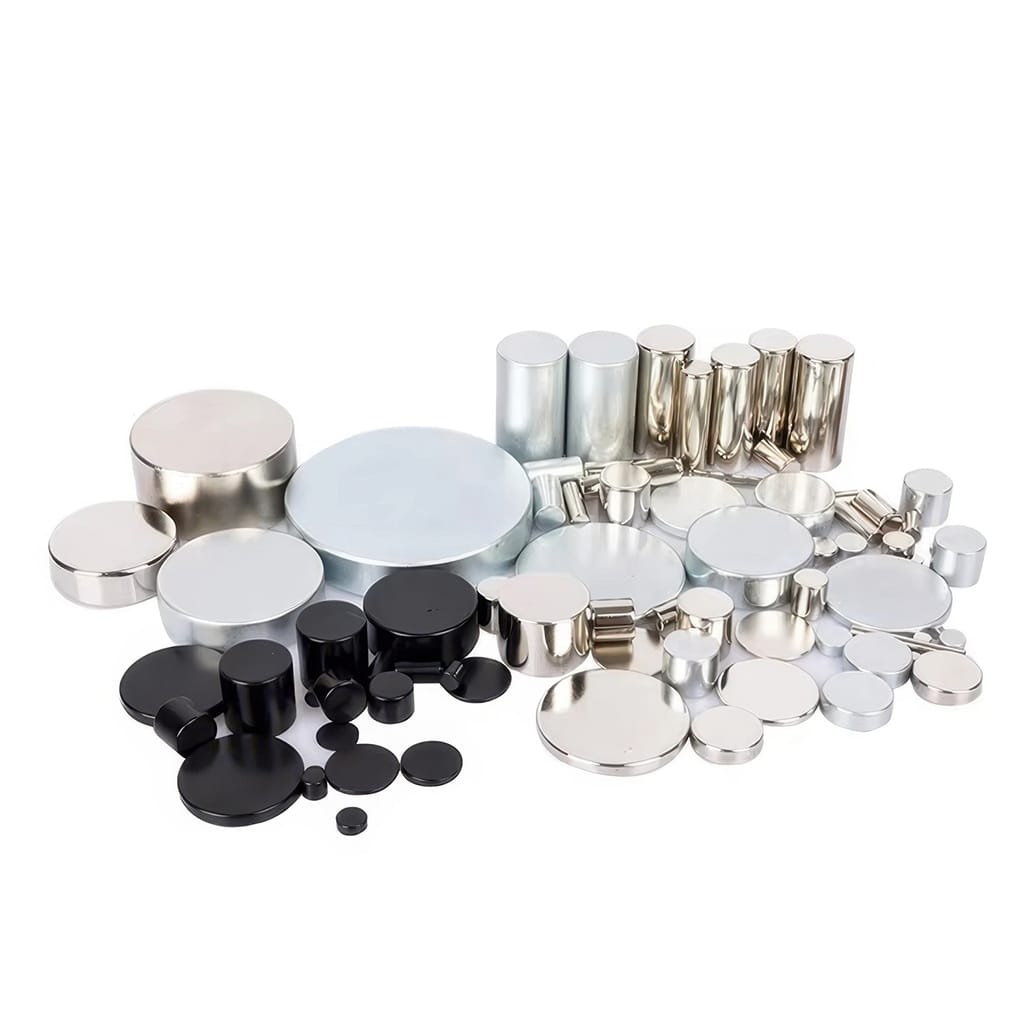