# Beyond the Solid: Exploring the Versatile World of Hole Magnets, Ring Magnets, and Through-Hole Applications
This article delves into the fascinating world of hole magnets, also known as ring magnets, exploring their unique properties, diverse applications, and advantages over traditional solid magnets. Discover how these specialized magnets are revolutionizing various industries, offering enhanced functionality and novel design possibilities. Learn about the different types of hole magnets, their manufacturing processes, and crucial factors to consider when selecting the right magnet for your specific application. This guide provides a comprehensive overview for engineers, designers, hobbyists, and anyone curious about the power and potential of hole magnets.
## The Distinct Advantages of Hole Magnets: Why Choose a Magnet with a Void?
Hole magnets, or ring magnets, offer several distinct advantages over their solid counterparts. The central aperture allows for the passage of a shaft, bolt, or other component directly through the magnet. This opens up a wide range of design possibilities for applications requiring rotational movement, precise alignment, or the integration of mechanical and magnetic functions. Imagine a sensor where the target passes through the magnet, triggering a response based on magnetic field changes. This direct integration wouldn’t be possible with a solid magnet.
Furthermore, the hole can concentrate the magnetic field around its edges, potentially increasing the holding force or magnetic flux density in specific areas surrounding the hole. This concentration can be particularly useful in applications requiring localized magnetic attraction or repulsion. Finally, the reduced weight compared to a solid magnet of the same volume can be a significant benefit in applications where weight is a critical factor, such as in aerospace or portable devices.
## Understanding Neodymium, Ferrite, and Other Hole Magnet Materials
The performance of a hole magnet is significantly influenced by the material from which it is crafted. Neodymium (NdFeB) magnets are renowned for their exceptionally high magnetic strength, making them ideal for applications requiring maximum holding force in a compact size. These magnets are, however, more susceptible to corrosion and typically require a protective coating, such as nickel or epoxy. They also have a lower Curie temperature compared to other magnet types, meaning their magnetic properties can degrade at higher temperatures.
Ferrite magnets, on the other hand, offer a more cost-effective solution and exhibit excellent resistance to corrosion and demagnetization. While their magnetic strength is lower than that of neodymium magnets, they are suitable for a wide range of applications where high magnetic force isn’t paramount. They are also very stable over a wide range of operating temperatures. Other materials, such as samarium cobalt (SmCo), offer a balance of high magnetic strength and temperature resistance, but tend to be more expensive. Choosing the right material depends heavily on the specific application requirements, considering factors like strength, temperature, cost, and corrosion resistance. Plastic bonded magnets are also an option.
## Common Shapes, Sizes, and Magnetization Directions of Ring Magnets
Hole magnets are available in a variety of shapes and sizes, catering to diverse application needs. The most common shape is a simple ring or disc with a central hole, but variations include cylindrical magnets with a bore, rectangular prisms with a through-hole, and even more complex geometries. The size of the hole and the overall dimensions of the magnet are crucial considerations for integration into devices and systems. A larger hole might be needed to accommodate a specific shaft size, while the outer diameter affects the overall footprint and available magnetic field strength.
The direction of magnetization is another critical factor. Axial magnetization, where the magnetic poles are located on the flat faces of the ring, is the most common configuration. However, diametrical magnetization, where the poles are located on opposite sides of the ring’s outer diameter, is also used for specific applications. For example, a diametrically magnetized ring magnet could be used as part of a rotary encoder. Understanding the application’s requirements and the interaction between the magnet and other components is key to selecting the appropriate shape, size, and magnetization direction.
## Manufacturing Processes: From Powder Metallurgy to Injection Molding
The manufacturing process for hole magnets varies depending on the material and desired properties. Powder metallurgy is a common method for producing neodymium and ferrite magnets. This process involves mixing fine powders of the component materials, compacting them under high pressure, and then sintering them at high temperatures to fuse the particles together. The sintering process often takes place in a controlled atmosphere to prevent oxidation and maintain the desired magnetic properties. Precision grinding and machining are often required after sintering to achieve the final dimensions and tolerances.
Injection molding is another method used for producing plastic bonded magnets. This process involves mixing magnetic powder with a polymer binder and then injecting the mixture into a mold. Injection molding allows for the creation of complex shapes and intricate features but typically results in lower magnetic performance compared to powder metallurgy due to the lower density of magnetic material. The choice of manufacturing process is influenced by factors such as production volume, desired magnetic properties, shape complexity, and cost.
## Applications in Electric Motors and Generators: Enhancing Rotational Performance
Hole magnets play a crucial role in enhancing the performance of electric motors and generators. Integrating ring magnets as rotor or stator components allows for efficient energy conversion and precise motor control. The central hole can accommodate the motor shaft, simplifying assembly and reducing overall size. The concentrated magnetic field around the hole can also improve torque output and efficiency.
In generators, ring magnets can be used to generate electrical current as they rotate within a coil of wire. The strength of the magnetic field and the speed of rotation directly influence the voltage and current produced. By carefully selecting the magnet material, size, and magnetization direction, engineers can optimize motor and generator designs for specific performance characteristics, such as high torque, low noise, or high efficiency. Advanced motor designs often employ segmented ring magnets to optimize the flux distribution around the air gap.
## Sensors and Actuators: Precision and Control with Integrated Hole Magnets
The unique geometry of hole magnets makes them well-suited for use in sensors and actuators. In sensor applications, the passage of a ferrous object through the hole can cause a measurable change in the magnetic field, triggering a sensor response. This principle is used in position sensors, speed sensors, and proximity detectors. The small size and high sensitivity of hole magnets allow for the creation of compact and accurate sensing systems.
In actuators, ring magnets can be used to provide controlled linear or rotational motion. For example, a ring magnet positioned around a coil of wire can be used to create a linear actuator. By controlling the current through the coil, the magnetic field generated interacts with the magnet, causing it to move. These actuators are used in a wide range of applications, from valve control to precision positioning systems. The integration of the hole magnet allows for simplified designs and improved performance compared to traditional actuator configurations.
## Magnetic Couplings: Non-Contact Power Transmission with Ring Magnets
Magnetic couplings utilize magnetic fields to transmit torque between two shafts without any physical contact. Hole magnets are often used in these couplings to create a strong and reliable magnetic connection. The magnets are arranged on the driving and driven shafts such that their magnetic fields interact, allowing torque to be transferred even through a physical barrier.
Magnetic couplings offer several advantages over traditional mechanical couplings, including reduced wear and tear, inherent overload protection, and the ability to isolate vibrations and noise. The ability to transmit torque through a sealed barrier makes them ideal for applications in harsh environments or where contamination is a concern. Ring magnets, with their central aperture, facilitate easier assembly and offer design flexibility in constructing efficient magnetic couplings.
## Creative Applications: From Magnetic Jewelry to Scientific Experiments
Beyond industrial applications, hole magnets find use in numerous creative and innovative endeavors. Magnetic jewelry, for instance, utilizes the attractive force of magnets to create clasps, closures, and decorative elements. Hole magnets can be easily incorporated into these designs, providing a secure and aesthetically pleasing attachment mechanism.
In scientific experiments, ring magnets can be used to create magnetic levitation devices, demonstrate magnetic field principles, or construct simple motors and generators. Their availability in various sizes and strengths makes them ideal for educational and research purposes. Artists and hobbyists also utilize hole magnets in their creations, exploring their unique properties to create engaging and interactive artworks. Their strong holding force and unique shape offer a wide range of possibilities for creative expression.
## Selecting the Right Hole Magnet: Key Considerations and Specifications
Choosing the right hole magnet requires careful consideration of several key factors. The first is the required magnetic strength, which depends on the application’s specific needs. If the magnets need to provide strong holding force, a neodymium magnet is likely the best choice. If high magnetic strength is not required a more cost effective ferrite magnet may suffice. The second factor is the operating temperature. Neodymium magnets have a relatively low Curie temperature, meaning their magnetic properties can degrade at higher temperatures. Samarium cobalt magnets offer better temperature stability. Corrosion resistance is another important consideration, especially in harsh environments. Neodymium magnets typically require a protective coating to prevent corrosion.
The magnet’s size and shape must also match the application’s requirements. The size of the hole must be large enough to accommodate any shafts or components that need to pass through it. The outer dimensions of the magnet must also be compatible with the surrounding hardware. Finally, the magnetization direction must be appropriate for the application. Axial magnetization is the most common, but diametrical magnetization may be required for certain applications. When specifying hole magnets, it is crucial to provide detailed information to the supplier, including material type, dimensions, tolerance requirements, coating specifications, and magnetization direction. This ensures that you receive magnets that meet your exact needs.
## Conclusion: Unleashing the Potential of Hole Magnets
Hole magnets, with their unique shape and diverse properties, offer a powerful tool for engineers, designers, and hobbyists alike. From enhancing the performance of electric motors to enabling innovative sensor designs and magnetic couplings, these magnets provide solutions to a wide range of challenges. By understanding the different materials, manufacturing processes, and key selection criteria, you can unlock the full potential of hole magnets and create groundbreaking applications in various industries. Exploring the versatile world of hole magnets opens new possibilities for innovation and design, pushing the boundaries of what’s possible with magnetic technology
## FAQ
### What exactly *is* a hole magnet?
A hole magnet, also known as a ring magnet, is a magnet with a hole through its center. This hole allows for the passage of a shaft, bolt, or other component, enabling unique design possibilities compared to solid magnets.
### What are the primary advantages of using a hole magnet?
The main benefits include the ability to pass objects through the center, potential for concentrated magnetic fields around the hole, reduced weight compared to solid magnets of the same volume, and simplified assembly in certain applications.
### What types of materials are commonly used to make hole magnets?
Neodymium (NdFeB) is popular for its high strength, while ferrite is a cost-effective option with good corrosion resistance. Samarium cobalt (SmCo) offers a balance of strength and temperature resistance. Plastic bonded magnets are also an option.
### How are hole magnets manufactured?
Powder metallurgy is a common method for neodymium and ferrite magnets, involving compaction and sintering. Injection molding is used for plastic bonded magnets allowing for the creations of complex shapes.
### What are some typical applications for hole magnets?
They are used in electric motors, generators, sensors, actuators, magnetic couplings, magnetic jewelry, scientific experiments, holding applications and more.
### What factors should I consider when selecting a hole magnet?
Consider the required magnetic strength, operating temperature, corrosion resistance, size, shape, hole diameter, and magnetization direction.
### Are hole magnets more expensive than solid magnets?
The cost depends on the material and manufacturing process. Neodymium hole magnets are generally more expensive than ferrite versions. The cost can also increase based on special requirements like tight tolerances, custom shapes, and premium material choices.
### Can hole magnets be custom-made to specific dimensions and shapes?
Yes, most magnet manufacturers offer custom design and manufacturing services to meet specific application requirements. Always check with the provider if you have any customization queries or special requirements before placing orders.
### Can hole magnets be remagnetized if they lose their strength?
While it’s possible to remagnetize magnets, it’s not typically done end-user. It usually requires specialized equipment and expertise. It’s more cost-effective to replace a magnet that has lost its strength, unless it’s a very large and costly magnet.
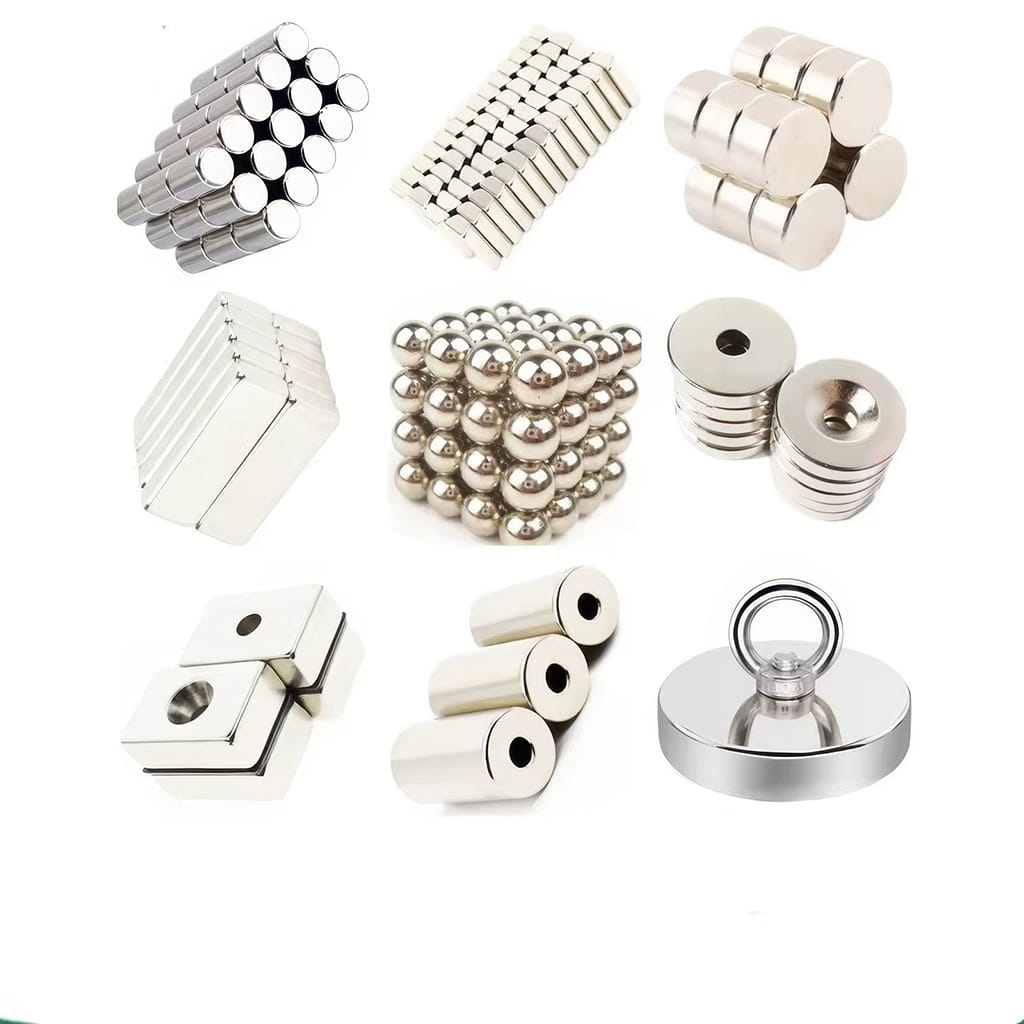