# Go Magnetic! Unveiling the Strength and Versatility of Magnetic Fastening Solutions
**Summary:** Tired of screws, bolts, and adhesives that fail under pressure or ruin your surfaces? Discover the revolutionary world of magnetic fastening! This article explores why magnets offer a superior solution for a vast array of applications, providing unmatched strength, convenience, and versatility. Learn about the different types of magnets, their advantages over traditional fasteners, and how to “go magnetic” for projects big and small.
## The Unmatched Holding Power of Magnets: A Deep Dive
Magnets, especially rare-earth magnets like neodymium, offer incredibly high holding power relative to their size. This means you can achieve a strong, secure connection without bulky hardware or extensive surface preparation. The force of attraction between two magnets can be precisely engineered, allowing for tailored solutions that range from delicate closures to heavy-duty industrial applications. This precision allows for designs that are both aesthetically pleasing and functionally robust, something often difficult to achieve with mechanical fasteners.
The magic behind this holding power comes down to the atomic alignment within the magnet material. Rare-earth magnets, in particular, have their atoms arranged in a way that creates a powerful magnetic field. This field interacts with other magnetic materials, creating a strong attractive force. This force isn’t just about brute strength; it’s also about control. The design of the magnetic circuit, including the shape, size, and placement of the magnets, can significantly influence the strength and distribution of the magnetic field.
Moreover, the holding power of magnets is generally consistent over time, especially when protected from corrosion and extreme temperatures. Unlike adhesives that can dry out or mechanical fasteners that can loosen due to vibration, magnets maintain their grip, providing long-lasting reliability. This longevity makes them an excellent choice for applications where maintenance and replacement are difficult or costly, such as in aerospace or automotive industries.
## Magnetic Simplicity: Ease of Installation and Removal
One of the most compelling advantages of magnetic fastening is its remarkable ease of installation and removal. No drilling, screwing, or gluing is required. Simply bring the magnets into contact, and they instantly snap together. This simplicity significantly reduces installation time and labor costs, especially in large-scale projects. It also minimizes the risk of damage to the materials being joined, as there’s no need for potentially destructive processes like drilling.
The reversibility of magnetic connections is another key benefit. Unlike permanent adhesives or mechanical fasteners that require tools and effort to remove, magnets can be detached and reattached as needed. This makes them ideal for applications that require frequent adjustments, maintenance, or modifications. Think of access panels, modular structures, or temporary signage – magnets offer a quick and effortless way to connect and disconnect components.
Furthermore, the clean and seamless aesthetic of magnetic fasteners is often preferred over traditional methods. With no visible screws or glue lines, magnetic connections create a more refined and professional look. This is particularly important in applications where appearance is a key factor, such as in furniture design, retail displays, or architectural elements. The hidden nature of magnetic fasteners allows for a focus on the overall design aesthetic, rather than being distracted by visible hardware.
## Versatility Unleashed: A Magnetic Solution for Every Need
Magnetic fastening solutions are incredibly versatile, finding applications across a wide range of industries and projects. From holding cabinet doors closed to securing heavy machinery, magnets can be tailored to meet specific needs in terms of size, shape, and holding power. This adaptability makes them a truly universal fastening solution, capable of replacing traditional methods in numerous situations.
Consider the possibilities in manufacturing. Magnets can be used to hold parts in place during assembly, to create jigs and fixtures, or to secure safety guards and access panels. In the construction industry, they can be used for temporary scaffolding, attaching decorative elements, or even holding insulation in place. The possibilities are virtually limitless, constrained only by our imagination.
The versatility extends to the materials that can be joined magnetically. While magnets primarily attract ferrous materials (iron, steel, nickel, and cobalt), they can also be used to attach non-magnetic materials by incorporating a steel plate or other ferrous component into the design. This allows for the creation of magnetic connections between wood, plastic, aluminum, and even glass, expanding the range of applications even further.
## Precision Alignment: Achieving Perfect Positioning Every Time
Magnets offer an inherent advantage in achieving precise alignment during assembly. The magnetic field itself acts as a guide, drawing the components together and ensuring they are perfectly aligned. This is particularly useful in applications where accuracy is critical, such as in electronics manufacturing, scientific instrumentation, or medical devices.
The self-aligning properties of magnets can also simplify complex assembly processes. Instead of relying on intricate jigs and fixtures to hold components in place, magnets can be used to automatically align and secure them. This not only reduces the cost of tooling but also speeds up the assembly process and improves the overall accuracy of the finished product.
Moreover, the controlled attraction force of magnets can prevent damage to delicate components during assembly. Unlike mechanical fasteners that can crush or deform parts if over-tightened, magnets apply a consistent and predictable force, minimizing the risk of damage. This is particularly important when working with sensitive materials or intricate designs.
## Durability & Longevity: Investing in a Long-Term Solution
Magnets, particularly rare-earth magnets, boast exceptional durability and longevity. When properly protected from corrosion and extreme temperatures, they can maintain their magnetic strength for decades, providing a long-lasting and reliable fastening solution. This makes them a worthwhile investment, especially in applications where reliability and maintenance are critical factors.
The resistance of magnets to vibration and impact is another significant advantage. Unlike mechanical fasteners that can loosen or break under stress, magnets remain securely attached, even in harsh environments. This is particularly important in applications such as automotive, aerospace, and industrial machinery, where vibration and impact are common occurrences.
To ensure optimal durability, it’s important to choose magnets that are coated or plated with a protective layer. Nickel plating, for example, provides excellent resistance to corrosion and abrasion, extending the lifespan of the magnet. Similarly, protecting magnets from extreme temperatures (above their Curie temperature) is crucial to prevent demagnetization.
## A Cleaner Alternative: Reducing Waste and Environmental Impact
Magnetic fastening offers a cleaner and more environmentally friendly alternative to traditional methods. By eliminating the need for adhesives, screws, and bolts, magnets reduce waste and minimize the use of harmful chemicals. This contributes to a more sustainable and eco-conscious approach to manufacturing and construction.
The reusable nature of magnetic fasteners further enhances their environmental benefits. Unlike single-use adhesives or mechanical fasteners that often end up in landfills, magnets can be detached and reused multiple times, reducing the demand for new resources. This promotes a circular economy model, where materials are kept in use for as long as possible.
Furthermore, the ease of disassembly facilitated by magnetic fasteners makes it easier to recycle components at the end of their life. This is particularly important for electronics and other products that contain valuable materials that can be recovered and reused. By facilitating easy disassembly, magnetic fasteners contribute to a more sustainable product lifecycle.
## Cost-Effectiveness: A Surprisingly Economical Choice
While the initial cost of magnets may be slightly higher than some traditional fasteners, the long-term cost-effectiveness of magnetic fastening solutions is often significantly better. The reduced installation time, lower maintenance costs, and increased lifespan of magnets can result in substantial savings over time.
The elimination of the need for specialized tools and equipment is another cost-saving factor. Magnetic fasteners can be installed and removed quickly and easily without the need for drills, screwdrivers, or other tools. This reduces labor costs and simplifies the assembly process.
Moreover, the increased durability and reliability of magnetic fasteners can prevent costly repairs and replacements. By minimizing the risk of failure, magnets can reduce downtime and improve the overall efficiency of operations. This makes them a wise investment, especially in applications where reliability is paramount.
## Choosing the Right Magnet: A Guide to Types and Applications
Selecting the right type of magnet is crucial for achieving optimal performance in any application. Different types of magnets offer varying levels of strength, temperature resistance, and corrosion resistance. Understanding these differences is essential for making informed decisions and ensuring that the chosen magnet meets the specific requirements of the project.
**Neodymium Magnets:** These are the strongest commercially available magnets, offering exceptional holding power in a small size. They are ideal for applications where high strength is required, such as in motors, generators, and magnetic closures. However, they are susceptible to corrosion and should be coated with a protective layer.
**Ferrite Magnets:** These are a cost-effective alternative to neodymium magnets, offering good strength and excellent corrosion resistance. They are commonly used in speakers, holding devices, and magnetic separation equipment.
**Samarium Cobalt Magnets:** These magnets offer high strength and excellent temperature resistance, making them suitable for applications in high-temperature environments, such as in aerospace and automotive industries. However, they are more brittle and expensive than neodymium and ferrite magnets.
**Alnico Magnets:** These magnets offer good temperature resistance and are relatively easy to magnetize. They are commonly used in electric motors, sensors, and holding devices. However, they are more susceptible to demagnetization than other types of magnets.
When selecting a magnet, it’s important to consider the following factors: holding power, size and shape, temperature resistance, corrosion resistance, and cost. Consulting with a magnet expert can help you choose the optimal magnet for your specific application.
## Conclusion: Embrace the Future of Fastening with Magnets
Magnets are revolutionizing the world of fastening, offering a superior alternative to traditional methods in terms of strength, convenience, versatility, durability, and cost-effectiveness. From simplifying assembly processes to creating cleaner and more sustainable solutions, magnets are transforming industries and enabling innovative new designs. It’s time to embrace the power of magnets and “go magnetic” for your next project! The benefits are clear: stronger, simpler, and more sustainable fastening solutions that will improve efficiency and reduce costs.
## Frequently Asked Questions (FAQ)
### What are the strongest magnets available?
Neodymium magnets are the strongest type of commercially available magnet. They offer exceptional holding power relative to their size, making them ideal for applications where high strength is required. These are rare-earth magnets, and the specific grade (N35, N42, N52, etc.) dictates their strength.
### Can magnets be used underwater?
Yes, magnets can be used underwater, but it’s important to choose magnets that are corrosion-resistant or coated with a protective layer. Ferrite magnets are naturally corrosion-resistant, while neodymium magnets can be coated with nickel, epoxy, or other materials to prevent corrosion. The specific coating will depend on the type of water (freshwater, saltwater, etc.) and the duration of exposure.
### How do I protect magnets from corrosion?
The best way to protect magnets from corrosion is to coat them with a protective layer, such as nickel, epoxy, or rubber. The choice of coating will depend on the type of magnet and the environment in which it will be used. Regularly inspecting and cleaning magnets can also help to prevent corrosion.
### What is the Curie temperature of a magnet?
The Curie temperature is the temperature at which a magnet loses its magnetism. Above the Curie temperature, the magnetic properties of the material are lost. The Curie temperature varies depending on the type of magnet. For example, neodymium magnets have a Curie temperature of around 310-400°C, while ferrite magnets have a Curie temperature of around 450°C.
### Can magnets interfere with electronics?
Yes, strong magnetic fields can interfere with some electronics. Magnets can damage magnetic storage devices, such as hard drives and floppy disks. They can also interfere with the operation of some electronic sensors and compasses. However, most modern electronics are designed to be resistant to magnetic interference. Keeping sensitive electronics away from strong magnets is always a good practice.
### Are magnetic fasteners more expensive than traditional fasteners?
The initial cost of magnetic fasteners may be slightly higher than some traditional fasteners, but the long-term cost-effectiveness is often better. The reduced installation time, lower maintenance costs, and increased lifespan of magnets can result in substantial savings over time. The elimination of the need for specialized tools and equipment is another cost-saving factor.
### Can magnets be used to hold items that are not metal?
Yes, magnets can be used to hold non-metallic items by incorporating a steel plate or other ferrous component into the design. This allows for the creation of magnetic connections between wood, plastic, aluminum, and even glass. The steel plate provides a surface for the magnet to attract to, creating a secure connection.
### How do I choose the right size magnet for my application?
The size of the magnet will depend on the weight and size of the items you need to hold, as well as the desired holding force. It’s important to consider the air gap between the magnet and the surface it will be attracting to, as this can significantly reduce the holding force. Consulting with a magnet expert can help you determine the optimal magnet size for your specific application. Formulas and online calculators can assist with this, but real-world testing is often recommended for critical applications.
### Are magnetic fasteners reusable?
Yes, magnetic fasteners are highly reusable. Unlike adhesives or mechanical fasteners that are often single-use, magnets can be detached and reattached multiple times, providing a flexible and cost-effective fastening solution. This reusability makes them a more sustainable and environmentally friendly alternative to traditional methods.
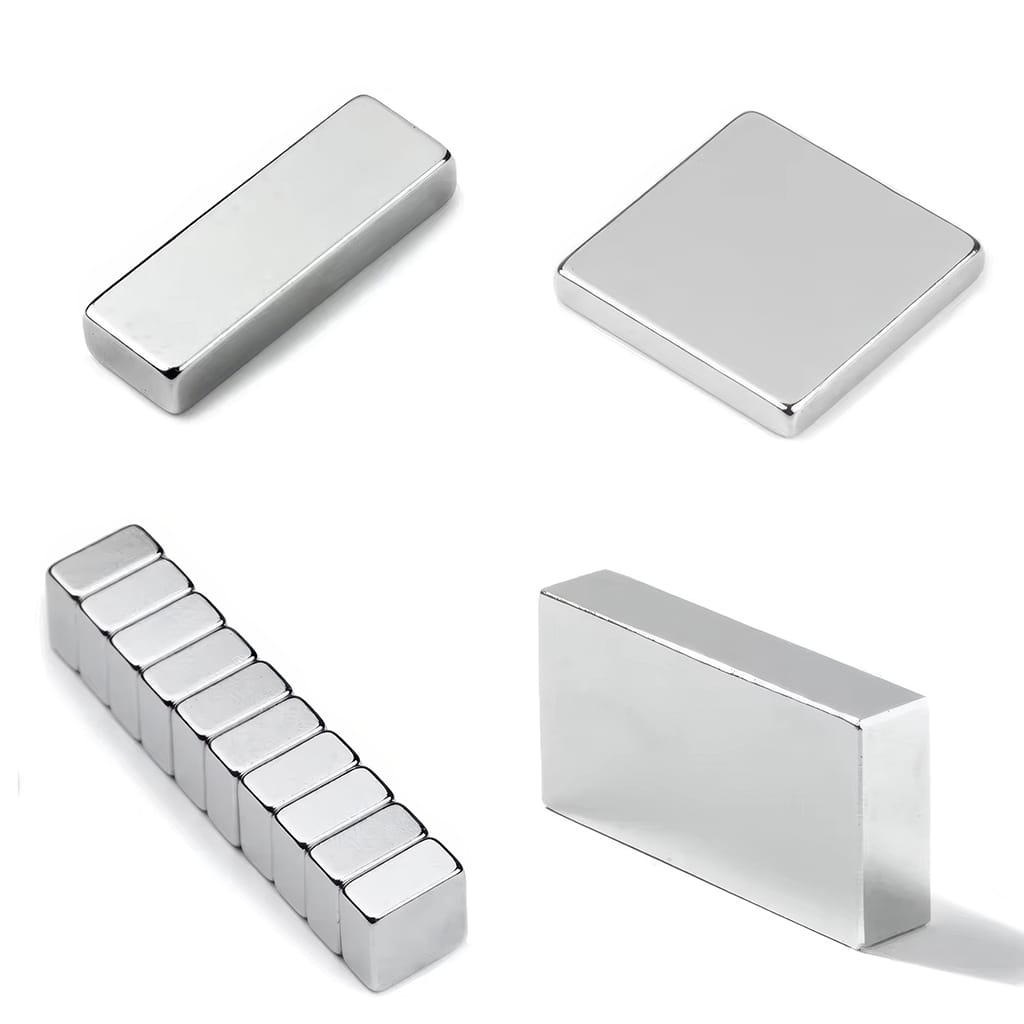