# Holes in Magnets: A Revolutionary Approach Transforming Magnetic Engineering
This article delves into the surprisingly impactful field of incorporating holes within magnets. It explores how strategically placed voids can drastically alter magnetic fields, enhance performance in various applications, and open up exciting new avenues for innovation in industries ranging from medical devices to high-efficiency motors. Read on to discover how these seemingly simple modifications are poised to revolutionize magnetic engineering.
## Modified Magnetism: The Surprising Power of Holes
The conventional understanding of magnets often focuses on their uniform magnetization. However, introducing holes into a magnet disrupts this uniformity, creating localized variations in the magnetic field. These variations, far from being detrimental, can be precisely engineered to achieve specific functionalities. The shape, size, and position of these holes act as powerful design parameters, allowing for unprecedented control over the magnetic behavior. This opens uppossibilities that were previously unattainable with solid, homogenous magnets. Imagine shaping magnetic fields with the same precision as carving a sculpture, achieving targeted effects within a device.
This concept goes beyond simply reducing the amount of magnetic material. The introduction of air gaps (or voids) dramatically affects the flux path, forcing the magnetic field lines to redistribute themselves. This redistribution can lead to enhanced field strength in specific areas, improved field uniformity in others, and even the creation of entirely new magnetic field patterns. This control unlocks a range of applications, from miniaturized devices with highly focused magnetic fields to large-scale systems with optimized performance.
## Tailoring Magnetic Fields: Precision Engineering Through Voids
One of the primary advantages of incorporating holes into magnets is the ability to tailor the magnetic field to meet specific application requirements. By carefully designing the shape, size, and location of the holes, engineers can precisely control the strength, direction, and uniformity of the magnetic field. This level of control is crucial for optimizing performance in a wide range of applications, from medical imaging to electric motors. Think of it as magnetic sculpting, where the holes act as chisels, refining and shaping the magnetic field to perfection.
For example, in magnetic resonance imaging (MRI) machines, highly uniform magnetic fields are essential for producing clear and accurate images. Incorporating strategically placed holes into the magnets can help to compensate for imperfections in the manufacturing process and to further improve field uniformity. Similarly, in electric motors, optimized magnetic fields can lead to increased efficiency and reduced noise. Holes in the magnets can be used to shape the field to maximize torque production and minimize energy losses.
## Enhancing Magnet Performance: Strength, Uniformity, and Beyond
The inclusion of holes doesn’t necessarily mean a reduction in overall magnetic strength. In some cases, strategically placed holes can actually enhance the field strength in specific regions of the magnet. This can be achieved by concentrating the magnetic flux lines in a smaller area, effectively amplifying the magnetic field. Imagine focusing sunlight with a magnifying glass – a similar principle applies to concentrating magnetic flux with carefully placed voids.
Furthermore, as mentioned earlier, holes can be used to improve the uniformity of the magnetic field. This is particularly important in applications where a consistent magnetic field is required over a large area, such as in magnetic sensors or in certain types of particle accelerators. By distributing the magnetic flux lines more evenly, holes can minimize variations in the magnetic field and improve the overall performance of the device. Beyond strength and uniformity, the presence of holes can also influence the thermal behavior of the magnet, allowing for improved heat dissipation in high-power applications.
## Diverse Applications: From Medical Devices to High-Efficiency Motors
The applications of magnets with holes are incredibly diverse, spanning a wide range of industries. In the medical field, these magnets are finding use in MRI machines, targeted drug delivery systems, and miniaturized medical devices. The ability to precisely control the magnetic field allows for more accurate imaging, more effective drug delivery, and the development of smaller and less invasive medical devices. The precise control allows for targeted therapies hitting only the intended area.
Beyond medicine, magnets with holes are also being used in electric motors, generators, and magnetic sensors. In electric motors, for example, they can be used to optimize the magnetic field for maximum torque production and efficiency. In magnetic sensors, they can be used to improve sensitivity and accuracy. The ongoing development of high-efficiency motors is heavily reliant on improvements in magnetic design and the strategic placement of holes within magnets is a key aspect of these advancements.
## Manufacturing Challenges: Precision is Paramount
While the concept of putting holes in magnets is relatively straightforward, the manufacturing process can be quite challenging. The precision required to accurately create these holes, particularly in small or complex magnets, demands advanced manufacturing techniques. Factors such as the material of the magnet, the size and shape of the holes, and the desired magnetic properties all play a role in determining the appropriate manufacturing method. Small imperfections can drastically change the intended result.
Some of the common manufacturing techniques used to create magnets with holes include machining, laser cutting, and additive manufacturing (3D printing). Machining is a traditional method that involves removing material from a solid block of magnet using cutting tools. Laser cutting offers greater precision and can be used to create more complex hole shapes. Additive manufacturing allows for the creation of highly intricate magnet designs with internal features and complex hole geometries. The choice of manufacturing method depends on the specific requirements of the application and the desired level of precision.
## Emerging Materials: Complementing Hole-Based Designs
The benefits of incorporating holes in magnets are further amplified when combined with the use of advanced magnetic materials. Rare-earth magnets, such as neodymium (NdFeB) and samarium cobalt (SmCo), offer exceptionally high magnetic strength, making them well-suited for applications where a high-performance magnetic field is required. The combination of these materials with sophisticated hole designs allows for the creation of magnets with unparalleled levels of control and performance.
Furthermore, research is ongoing into the development of new magnetic materials with improved properties, such as higher Curie temperatures (the temperature above which a material loses its magnetism) and better corrosion resistance. These new materials, combined with innovative hole-based designs, promise to further expand the capabilities of magnetic engineering. Consider, for example, the potential for high-temperature applications where tailored magnetic fields are crucial, or the development of environmentally friendly magnets with reduced reliance on rare-earth elements.
## Computational Modeling: Predicting and Optimizing Magnetic Behavior
Designing magnets with holes is not simply a matter of intuition. Computational modeling plays a crucial role in predicting and optimizing the magnetic behavior of these complex structures. Software tools based on finite element analysis (FEA) allow engineers to simulate the magnetic field distribution within a magnet with holes, providing valuable insights into the effects of different hole designs. This allows for informed decision-making and reduces the need for costly trial-and-error experimentation.
By using FEA, engineers can explore a wide range of hole shapes, sizes, and positions, and quickly assess their impact on the magnetic field. This allows for the rapid optimization of magnet designs for specific applications. Furthermore, computational modeling can be used to predict the effects of manufacturing tolerances on the magnetic performance of the magnet, helping to ensure that the final product meets the required specifications. The advancements in computational power and software are critical to the continued progress and refinement of hole-based magnetic design.
## Future Directions: Towards Intelligent Magnetic Systems
The field of magnets with holes is rapidly evolving, with new research and development efforts constantly pushing the boundaries of what is possible. One promising area of research is the development of “intelligent” magnetic systems that can adapt their magnetic field in response to changing conditions. This could be achieved by incorporating actuators or sensors that can modify the shape or position of the holes within the magnet, effectively tuning the magnetic field in real-time.
Another exciting area of research is the development of new manufacturing techniques that can create even more complex and intricate hole designs. This could involve the use of advanced additive manufacturing techniques or the development of new methods for precisely controlling the shape and size of the holes. The ultimate goal is to create magnetic systems that are highly customizable, efficient, and adaptable to a wide range of applications. The path forward is paved with innovation and the potential for truly revolutionary advancements in magnetic engineering.
## Conclusion
The strategic incorporation of holes into magnets represents a significant advancement in magnetic engineering. This seemingly simple modification unlocks a powerful ability to tailor magnetic fields, enhance magnet performance, and create innovative solutions for a multitude of applications. From improving the clarity of MRI images to boosting the efficiency of electric motors, the possibilities are vast. While manufacturing challenges remain, ongoing research in materials science, computational modeling, and advanced manufacturing techniques are paving the way for even more sophisticated and intelligent magnetic systems. The future of magnetic engineering is undoubtedly shaped by the surprising power of strategically placed voids.
## FAQ
### What are the main advantages of using magnets with holes?
Magnets with holes provide greater control over the magnetic field, allowing for tailored field strength, improved uniformity, and enhanced performance in specific applications. They can also lead to more efficient and compact devices.
### How are holes created in magnets?
Common methods include machining, laser cutting, and additive manufacturing (3D printing). The choice of method depends on the desired precision, complexity, and material of the magnet.
### What types of magnets are best suited for incorporating holes?
Rare-earth magnets, such as neodymium (NdFeB) and samarium cobalt (SmCo), are often preferred due to their high magnetic strength. However, the specific material choice depends on the application requirements.
### Are magnets with holes weaker than solid magnets?
Not necessarily. While introducing holes reduces the amount of magnetic material, strategically placed holes can concentrate the magnetic flux, actually enhancing the field strength in specific regions.
### What industries benefit from using magnets with holes?
A wide range of industries benefit, including medical, automotive, aerospace, and electronics. Specific applications include MRI machines, electric motors, magnetic sensors, and targeted drug delivery systems.
### How does computational modeling help in designing magnets with holes?
Computational modeling allows engineers to simulate the magnetic field distribution within a magnet with holes, predicting the effects of different hole designs and optimizing the magnet for specific performance requirements.
### What are some of the future trends in magnets with holes?
Future trends include the development of intelligent magnetic systems that can adapt their magnetic field in response to changing conditions, and the use of advanced manufacturing techniques to create even more complex and intricate hole designs.
### Is incorporating holes into magnets more expensive than using traditional solid magnets?
The cost depends on the manufacturing method, the complexity of the hole design, and the required precision. In some cases, the benefits of improved performance and efficiency can outweigh the increased manufacturing cost.
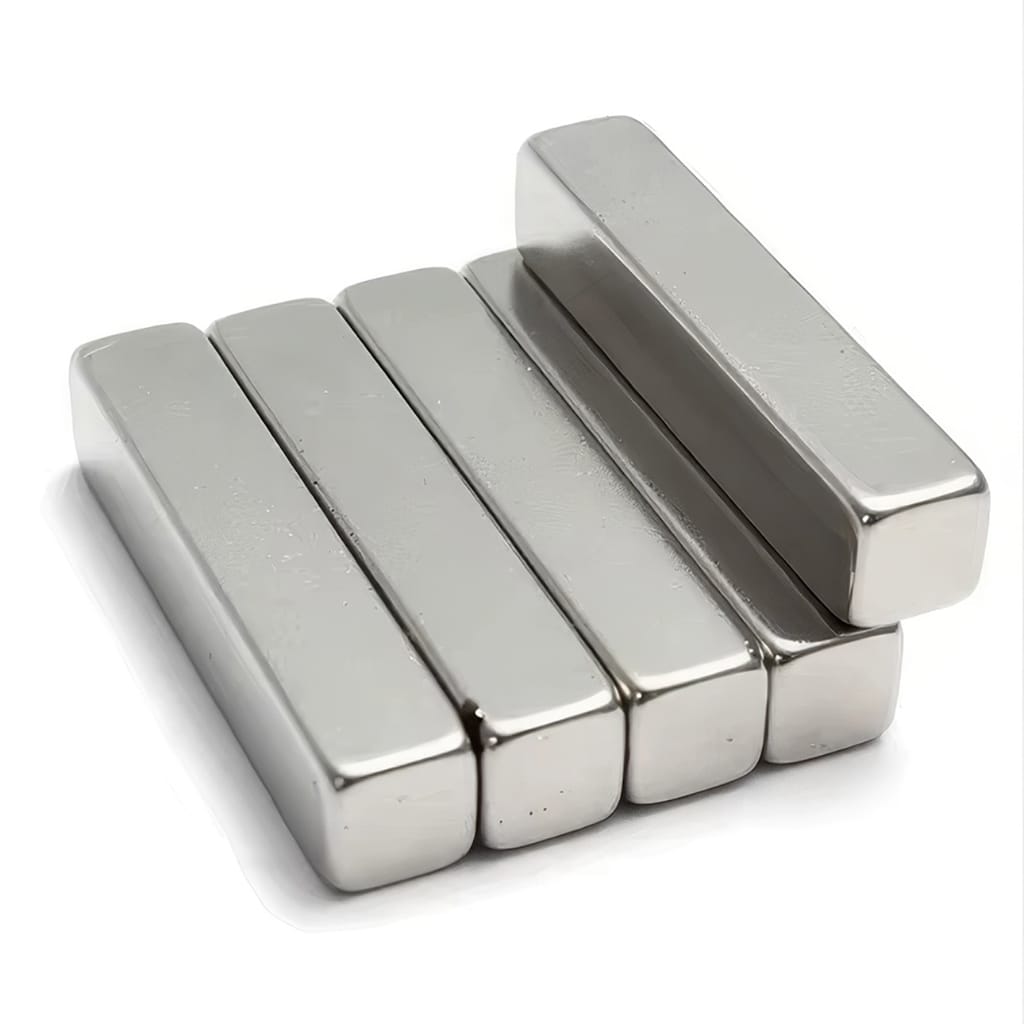